The
tuning circuits has a large knob potentiometers tuning system
which use voltage controlled capacitances such as varactor diodes as
the frequency determining elements.
How AFC Circuit Works in B/W Analog Television Receiver:

Push-Button tuning on u.h.f. while being very convenient often leaves a margin of mistuning, especially after some wear and tear has occurred on the mechanism. Even dial tuning can lead to errors due to the difficulty many people experience in judging the correct point. Oscillator drift due to temperature changes can also cause mistuning. Automatic frequency control (a.f.c.) will correct all these faults. The vision carrier when the set is correctly tuned on u.h.f. is at 39.5MHz as it passes down the i.f. strip. Thus if at the end of the i.f. strip a discriminator tuned circuit is incorporated centred on 39.5MHz the discriminator output will be zero at 39.5MHz and will move positively' one side of 39.5MHz and negatively the other as the tuning drifts. This response is shown in Fig. 1.
If the tuning is not correct then the discriminator output is not zero and if this output is applied to change the reverse bias on a tuning diode mounted in the oscillator section of the u.h.f. tuner it will correct most of the error. Tuning, varicap or varactor diodes-to give them a few of their names-are junction diodes normally operated with reverse bias but not sufficient to bias them into the breakdown region in which zener diodes operate. The greater the reverse bias the lower their capacitance: a typical curve, for the PHILIPS BB105 or STC BA141 tuning diode, is shown in Fig. 2. All diodes e

xhibit this basic type of characteristic but special diodes have to be used for u.h.f. because they must not introduce any excessive loss into the tuned circuits they control. In other words, just as a coil has to have a good Q so does a varicap diode. Normally, we don't worry about the Q of a capacitor as it is usually very good. However, a tuning diode is not a true capacitor. It has, for example, leakage current so the Q of the diode is a factor which has to be considered. The diode manufacturer however will have considered these points and if you buy a diode specified for u.h.f. use you will have no trouble. These points have been mentioned to clear up any misunderstandings and to show why any old diode won't do.
Basic AFC SystemTo return to our TV set, if the oscillator frequency is too high then the vision carrier frequency will also be too high and in the simple arrangement shown in Fig. 3 the discriminator will give a negative signal to decrease the bias on the tuning diode thus increasing its

capacitance and in turn reducing the oscillator frequency and correcting the error. Note that in this diagram the reverse bias on the diode is applied to its cathode. It is therefore positive with respect to ground so that a negative signal from the discriminator will reduce the positive voltage on the diode thus reducing its bias and increasing its capacitance. In this arrangement the diode is biased somewhere near the mid point of its characteristic by the positive d.c. bias fed into one side of the discriminator. The discriminator thus adds to or subtracts from this d.c. bias.
AFC Loop Gain:The amount by which the error is reduced depends on the gain of the circuit. An estimate of the gain required must first be made by guessing how much error is likely to be given by your push -buttons or hand tuning: 1MHz would be an outside figure as a tuning error of that magnitude would produce a very bad picture of low definition in one direction and badly broken up in the other. This error should be reduced to

about 100kHz to be really unnoticeable, indicating a required gain of ten. In fitting a.f.c. to an existing set some measure- ments should be done as an experiment before finally deciding on the circuit gain. The first thing to do is to add the suggested discriminator to the i.f. strip. As the circuit (Fig. 4) shows a Foster -Seeley type discriminator is used and with the coils specified and the driver circuit shown it should give ±4V for 0.5MHz input variation.
EXAMPLE of Circuit Description:The driver stage Tr1 takes a small sample signal from the i.f. strip but this should be large enough to drive Tr1 into saturation. That is to say Tr1 is a limiter stage so that the signal amplitude applied to the discriminator coil L2 stays constant over the normal range of signal levels. Trl is biased at approximately 7mA which, according to the original report ("Simple a.f.c. system for 625 -line TV receivers" by P. Bissmire, PHILIPS Technical Communications, March, 1970), gives the best limiting performance. C1, R

14 and R3 damp the stage to prevent oscillation. C2 decouples the power feed and should be close to the circuit. The coil former and can are the normal ones used for TV sets and so should be easily obtainable: the former diameter is 5mm. and length 40mm. and winding details are given in Fig. 5.
The invention being thus described, it will be obvious that the same may be varied in many ways. Such variations are not to be regarded as a departure from the spirit and scope of the invention, and all such modifications as would be obvious to one skilled in the art are intended to be included within the scope of the developed apparates both tubes or transistors.
Therefore a stable AFC circuit is developed:

A
superheterodyne receiver having an automatic intermediate
frequency control circuit with means to prevent the faulty
regulation thereof. The receiver has means for receiving a radio
frequency signal and mixing the same with the output of a
superheterodyne oscillator. This produces an intermediate frequency
signal which is coupled to a frequency or phase discriminator to
produce an error signal for controlling the frequency of the
superheterodyne oscillator. A regulation circuit is provided having
an electronic switch to interrupt the feedback circuit when only
unwanted frequencies tend to produce faulty regulation of the
superheterodyne oscillator.
Power supply
is realized with mains transformer and Linear transistorized power
supply stabilizer, A DC power supply apparatus includes a rectifier
circuit which rectifies an input commercial AC voltage. The
rectifier output voltage is smoothed in a smoothing capacitor.
Voltage stabilization is provided in the stabilizing circuits by the
use of Zener diode circuits to provide biasing to control the
collector-emitter paths of respective transistors.A linear regulator
circuit according to an embodiment of the present invention has an
input node receiving an unregulated voltage and an output node
providing a regulated voltage. The linear regulator circuit includes a
voltage regulator, a bias circuit, and a current control device.

In
one embodiment, the current control device is implemented as an
NPN bipolar junction transistor (BJT) having a collector electrode
forming the input node of the linear regulator circuit, an emitter
electrode coupled to the input of the voltage regulator, and a base
electrode coupled to the second terminal of the bias circuit. A
first capacitor may be coupled between the input and reference
terminals of the voltage regulator and a second capacitor may be
coupled between the output and reference terminals of the voltage
regulator. The voltage regulator may be implemented as known to
those skilled in the art, such as an LDO or non-LDO 3-terminal
regulator or the like.
The bias circuit may include a bias
device and a current source. The bias device has a first terminal
coupled to the output terminal of the voltage regulator and a
second terminal coupled to the control electrode of the current
control device. The current source has an input coupled to the first
current electrode of the current control device and an output
coupled to the second terminal of the bias device. A capacitor may
be coupled between the first and second terminals of the bias
device.

In the bias device and current source embodiment, the
bias device may be implemented as a Zener diode, one or more
diodes coupled in series, at least one light emitting diode, or any
other bias device which develops sufficient voltage while
receiving current from the current source. The current source may
be implemented with a PNP BJT having its collector electrode
coupled to the second terminal of the bias device, at least one
first resistor having a first end coupled to the emitter electrode
of the PNP BJT and a second end, a Zener diode and a second resistor.
The Zener diode has an anode coupled to the base electrode of the
PNP BJT and a cathode coupled to the second end of the first
resistor. The second resistor has a first end coupled to the anode
of the Zener diode and a second end coupled to the reference
terminal of the voltage regulator. A second Zener diode may be
included having an anode coupled to the cathode of the first Zener
diode and a cathode coupled to the first current electrode of the
current control device.

A circuit is disclosed for improving
operation of a linear regulator, having an input terminal, an
output terminal, and a reference terminal. The circuit includes an
input node, a transistor, a bias circuit, and first and second
capacitors. The transistor has a first current electrode coupled to
the input node, a second current electrode for coupling to the
input terminal of the linear regulator, and a control electrode. The
bias circuit has a first terminal for coupling to the output
terminal of the linear regulator and a second terminal coupled to
the control electrode of the transistor. The first capacitor is for
coupling between the input and reference terminals of the linear
regulator, and the second capacitor is for coupling between the
output and reference terminals of the linear regulator. The bias
circuit develops a voltage sufficient to drive the control terminal
of the transistor and to operate the linear regulator. The bias
circuit may be a battery, a bias device and a current source, a
floating power supply, a charge pump, or any combination thereof.
The transistor may be implemented as a BJT or FET or any other
suitable current controlled device.

Power Supply: The examples chosen are taken from manufacturers' circuit diagrams and are usually simplified to emphasise the fundamental nature of the circuit. For each example the particular transistor properties that are exploited to achieve the desired performance are made clear. As a rough and ready classification the circuits are arranged in order of frequency: this part is devoted to circuits used at zero frequency, field frequency and audio frequencies. Series Regulator Circuit Portable television receivers are designed to operate from batteries (usually 12V car batteries) and from the a.c. mains. The receiver usually has an 11V supply line, and circuitry is required to ensure that the supply line is at this voltage whether the power source is a battery or the mains. The supply line also needs to have good regulation, i.e. a low output resistance, to ensure that the voltage remains constant in spite of variations in the mean current taken by some of the stages in the receiver. Fig. 1 shows a typical circuit of the power -supply arrangements. The mains transformer and bridge rectifier are designed to deliver about 16V. The battery can be assumed to give just over 12V. Both feed the regulator circuit Trl, Tr2, Tr3, which gives an 11V output and can be regarded as a three -stage direct -coupled amplifier. The first stage Tr 1 is required to give an output current proportional to the difference between two voltages, one being a constant voltage derived from the voltage reference diode D I (which is biased via R3 from the stabilised supply). The second voltage is obtained from a preset potential divider connected across the output of the unit, and is therefore a sample of the output voltage. In effect therefore Tr 1 compares the output voltage of the unit with a fixed voltage and gives an output current proportional to the difference between them. Clearly a field-effect transistor could do this, but the low input resistance of a bipolar transistor is no disadvantage and it can give a current output many times that of a field-effect transistor and is generally preferred therefore. The output current of the first stage is amplified by the two subsequent stages and then becomes the output current of the unit. Clearly therefore Tr2 and Tr3 should be current amplifiers and they normally take the form of emitter followers or common emitter stages (which have the same current gain). By adjusting the preset control we can alter the fraction of the output voltage' applied to the first stage and can thus set the output voltage of the unit at any desired value within a certain range. By making assumptions about the current gain of the transistors we can calculate the degree of regulation obtainable. For example, suppose the gain of Tr2 and Tr3 in cascade is 1,000, and that the current output demanded from the unit changes by 0.1A (for example due to the disconnection of part of the load). The corresponding change in Tr l's collector current is 0.1mA and, if the standing collector current of Tr 1 is 1mA, then its mutual conductance is approximately 4OmA/V and the base voltage must change by 2.5mV to bring about the required change in collector current. If the preset potential divider feeds one half of the output voltage to Tr l's base, then the change in output voltage must be 5mV. Thus an 0.1A change in output current brings about only 5mV change in output voltage: this represents an output resistance of only 0.0552.
TDA1170 vertical deflection FRAME DEFLECTION INTEGRATED CIRCUITGENERAL DESCRIPTION f The TDA1170 and TDA1270 are monolithic integrated
circuits designed for use in TV vertical deflection systems. They are manufactured using
the Fairchild Planar* process.
Both devices are supplied in the 12-pin plastic power package with the heat sink fins bent
for insertion into the printed circuit board.
The TDA1170 is designed primarily for large and small screen black and white TV
receivers and industrial TV monitors. The TDA1270 is designed primarily for driving
complementary vertical deflection output stages in color TV receivers and industrial
monitors.
APPLICATION INFORMATION (TDA1170)
The vertical oscillator is directly synchronized by the sync pulses (positive or negative); therefore its free
running frequency must be lower than the sync frequency. The use of current feedback causes the yoke
current to be independent of yoke resistance variations due to thermal effects, Therefore no thermistor is
required in series with the yoke. The flyback generator applies a voltage, about twice the supply voltage, to
the yoke. This produces a short flyback time together with a high useful power to dissipated power
ratio.
GENERAL BASIC TRANSISTOR LINE OUTPUT STAGE OPERATION:
The
basic essentials of a transistor line output stage are shown in Fig.
1(a). They comprise: a line output transformer which provides the d.c.
feed to the line output transistor and serves mainly to generate the
high -voltage pulse from which the e.h.t. is derived, and also in
practice other supplies for various sections of the receiver; the line
output transistor and its parallel efficiency diode which form a
bidirectional switch; a tuning capacitor which resonates with the line
output transformer primary winding and the scan coils to determine the
flyback time; and the scan coils, with a series capacitor which provides
a d.c. block and also serves to provide slight integration of the
deflection current to compensate for the scan distortion that would
otherwise be present due to the use of flat screen, wide deflection
angle c.r.t.s. This basic circuit is widely used in small -screen
portable receivers with little elaboration - some use a pnp output
transistor however, with its collector connected to chassis.
Circuit Variations:
Variations
to the basic circuit commonly found include: transposition of the scan
coils and the correction capacitor; connection of the line output
transformer primary winding and its e.h.t. overwinding
in series; connection of the deflection components to a tap on the
transformer to obtain correct matching of the components and conditions
in the stage; use of a boost diode which operates in identical manner to
the arrangement used in valve line output stages, thereby increasing
the effective supply to the stage; omission of the efficiency diode
where the stage is operated from an h.t. line, the collector -base
junction of the line output transistor then providing the efficiency
diode action without, in doing so, producing scan distortion; addition
of inductors to provide linearity and width adjustment; use of a pair of
series -connected line output transistors in some large -screen colour
chassis; and in colour sets the addition of line convergence circuitry
which is normally connected in series between the line scan coils and
chassis. These variations on the basic circuit do not alter the basic
mode of operation however.
Resonance

The
most important fact to appreciate about the circuit is that when the
transistor and diode are cut off during the flyback period - when the
beam is being rapidly returned from the right-hand side of the screen to
the left-hand side the tuning capacitor together with the scan coils
and the primary winding of the line output transformer form a parallel
resonant circuit: the equivalent circuit is shown in Fig. 1(b). The line
output transformer primary winding and the tuning capacitor as drawn in
Fig. 1(a) may look like a series tuned circuit, but from the signal
point of view the end of the transformer primary winding connected to
the power supply is earthy, giving the equivalent arrangement shown in
Fig. 1(b).
The Flyback Period:
Since the operation of the
circuit depends mainly upon what happens during the line flyback period,
the simplest point at which to break into the scanning cycle is at the
end of the forward scan, i.e. with the

beam deflected to the right-hand side of the screen, see Fig. 2. At
this point the line output transistor is suddenly switched off by the
squarewave drive applied to its base. Prior to this action a linearly
increasing current has been flowing in the line output transformer
primary winding and the scan coils, and as a result magnetic fields have
been built up around these components. When the transistor is switched
off these fields collapse, maintaining a flow of current which rapidly
decays to zero and returns the beam to the centre of the screen. This
flow of current charges the tuning capacitor, and the voltage at A rises
to a high positive value - of the order of 1- 2k V in large -screen
sets, 200V in the case of mains/battery portable sets. The e

nergy
in the circuit is now stored in the tuning capacitor which next
discharges, reversing the flow of current in the circuit with the result
that the beam is rapidly deflected to the left-hand side of the screen -
see Fig. 3. When the tuning capacitor has discharged, the voltage at A
has fallen to zero and the circuit energy is once more stored in the
form of magnetic fields around the inductive components. One half -cycle
of oscillation has occurred, and the flyback is complete.
Energy Recovery:
First
Part of Forward Scan The circuit then tries to continue the cycle of
oscillation, i.e. the magnetic fields again collapse, maintaining a
current flow which this time would charge the tuning capacitor
negatively (upper plate). When the voltage at A reaches about -0.6V
however the efficiency diode becomes forward biased and switches on.
This damps the circuit, preventing further oscillation, but the magnetic
fields continue to collapse and in doing so produce a linearly decaying
current flow which provides the first part of the forward s

can,
the beam returning towards the centre of the screen - see Fig. 4. The
diode shorts out the tuning capacitor but the scan correction capacitor
charges during this period, its right-hand plate becoming positive with
respect to its left-hand plate, i.e. point A. Completion of Forward Scan
When the current falls to zero, the diode will switch off. Shortly
before this state of affairs is reached however the transistor is
switched on. In practice this is usually about a third of the way
through the scan. The squarewave applied to its base drives it rapidly
to saturation, clamping the vol

tage
at point A at a small positive value - the collector emitter saturation
voltage of the transistor. Current now flows via the transistor and the
primary winding of the line output transformer, the scan correction
capacitor discharges, and the resultant flow of current in the line scan
coils drives the beam to the right-hand side of the screen see Fig. 5.
Efficiency:
The
transistor is then cut off again, to give the flyback, and the cycle of
events recurs. The efficiency of the circuit is high since there is
negligible resistance present. Energy is fed into the circuit in the
form of the magnetic fields that build up when the output transistor is
switched on. This action connects the line output transformer primary
winding across the supply, and as a result a linearly increasing current
flows through it. Since the width is
dependent on the supply voltage, this must be stabilised.
Harmonic Tuning:
There
is another oscillatory action in the circuit during the flyback period.
The considerable leakage inductance between the primary and the e.h.t.
windings of the line output transformer, and the appreciable self
-capacitance present, form a tuned circuit which is shocked into
oscillation by the flyback pulse. Unless this oscillation is controlled,
it will continue into and modulate the scan. The technique used to
overcome this effect is to tune the leakage inductance and the
associated capacitance to an odd harmonic of the line flyback
oscillation frequency. By doing this the oscillatory actions present at
the beginning of the scan cancel. Either third or fifth harmonic tuning
is used. Third harmonic tuning also has the effect of increasing the
amplitude of the e.h.t. pulse, and is generally used where a half -wave
e.h.t. rectifier is employed. Fifth harmonic tuning results in a
flat-topped e.h.t. pulse, giving improved e.h.t. regulation, and is
generally used where an e.h.t. tripler is employed to produce the e.h.t.
The tuning is mainly built into the line output transformer, though an
external variable inductance is commonly found in colour chassis so that
the tuning can be adjusted. With a following post I will go into the
subject of modern TV line timebases in greater detail with other models
and technology shown here at Obsolete Technology Tellye !
RCA CA920 CA920AE / TBA920 line oscillator combination
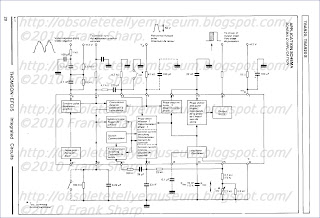
DESCRIPTION
The line oscillator combination CA920 TBA920 is a monolithic
integrated circuit intended for the horizontal deflection of the black and white
and colour TV sets
picture tube.
FEATURES:
SYNC-PULSE SEPARATION
OPTIONAL NOISE INVERSION
GENERATION OF A LINE FREQUENCY VOL-
TAGE BY MEANS OF AN OSCILLATOR
PHASE COMPARISON BETWEEN SYNC-

PULSE AND THE OSCILLATOR WAVEFORM
PHASE COMPARISON BETWEEN THE OS-
CILLATOR WAVEFORM AND THE MIDDLE OF
THE LINE FLY-BACK PULSE
AUTOMATIC SWITCHING OF THE VARIABLE
TRANSCONDUCTANCE AND THE VARIABLE
TIME CONSTANT TO ACHIEVE NOISE SUP-
PRESSION AND, BY SWITCHING OFF, POS-
SIBILITY OF TAPE-VIDEO-REGISTERED RE-
PRODUCTION
SHAPING AND AMPLIFICATION OF THE OS-
CILLATOR WAVEFORM TO OBTAIN PULSES
FOR THE CONTROL OF DRIVING STAGES IN
HORIZONTAL, DEFLECTION CIRCUITS
USING EITHER TRANSISTORS OR THYRISTORS.
In a conventional line scan circuit, such as in the Plessey or Mullard TBA920 integrated circuit, a phase-locked oscillator is synchronized with the incoming horizontal synchronization (H-sync) pulses to provide a control signal to the line output circuit. This ensures that oscillation is maintained in the absence of the H-sync signal, for example, during maintenance in the case of a display terminal, or, in the case of a TV receiver, when untuned, and noise on the incoming signal is smoothed out. The phase relationship between the output and input is very precisely maintained to prevent line tearing and other picture defects.
Flyback voltage pulses occur at the terminals of the yoke of the cathode ray tube (CRT) between successive horizontal scans of the electron beam while the screen is blanked. Due to component tolerances and temperature effects, the flyback voltage pulses may be broadened and unless the broadened pulse falls within the blanking period, picture defects can occur. Conventionally, this problem has been overcome by designing the CRT circuits to allow a broad blanking period between the line scans: however, this has a deleterious effect on the efficiency of the display.

The design of the driver and horizontal output transistor stages is
very critical. In typical circuits the horizontal output transistor
conducts during the last half of the trace interval and is sharply
cut-off to initiate retrace. During retrace a large retrace or flyback
voltage appears at the collector of the horizontal output transistor. If
the transistor is conducting when this voltage appears, the retrace
current will be altered and the transistor will dissipate excessive
power which generally will result in damage to the transistor. Since the
horizontal output transistor is conducting heavily immediately before
retrace is initiated, the stored charge in the base and collector
regions of the transistor must be removed before the transistor will
cease conducting collector current. Normally this stored charge is
removed by applying a negative pulse to the base of an NPN transistor to
cause a reverse base current to flow. This negative pulse, however,
should be applied only as long as necessary to alleviate the voltage
stress on the collector-base junction during retrace. R. J. Walker and
R. Yu, "Horizontal Output Transistor Base Circuit Design," IEEE
Transactions on Broadcast and Television Receivers, Vol. BTR-20, Aug.
1974, pp. 185-192, describe the various design requirements for the
base circuit of the horizontal output transistor.
The above
design requirements place severe limitations on the horizontal driver
transistor and transformer design. In typical circuits conduction by the
driver transistor during retrace and the first half of trace switches
the output transistor off. The driver transformer stores energy during
conduction by the driver transistor which is used to provide forward
base current to the horizontal output transistor during the following
conduction interval of the output transistor. Accordingly, the drive
current in the primary winding must be of the proper amplitude and
duration to maintain the horizontal output transistor in conduction in
saturation during the second half of trace. When the driver transistor
turns on again, the initial current flow through the primary winding of
the driver transformer provides a turn-off pulse to the base of the
output transistor. The amplitude and duration of the turn-off pulse are
dependent on the inductances and the turns ratio of the driver
transformer windings.

THE TBA920 SYNC/TIMEBASE IC It has been quite common for some time for sync separation to be carried out in an i.c. but until 1971 this was as far as i.c.s had gone in television receiver timebase circuitry. With the recent introduction of the delta featured 110° colour series however i.c.s have gone a step farther since this chassis uses a TBA920 as sync separator and line generator. A block diagram of this PHILIPS /Mullard i.c. is shown in Fig. 1.
The video signal at about 2-7V peak -peak is fed to the sync separator section at pin 8, the composite sync waveform appearing at pin 7.
The noise gate switches off the sync separator when a positive -going input pulse is fed in at pin 9, an external noise limiter circuit being required .
The line sync pulses are shaped by R1 /C1 /C2/R2 and fed in to the oscillator phase detector section at pin 6.
The line oscillator waveform is fed internally to the oscillator phase detector circuit which produces at pin 12 a d.c. potential which is used to lock the line oscillator to the sync pulse frequency, the control potential being fed in at pin 15. The oscillator itself is a CR type whose waveform is produced by the charge and discharge of the external capacitor (C7) connected to pin 14. The oscillator frequency is set basically by C7 and R6 and can be varied by the control potential appearing at pin 15 from pin 12 and the external line hold control. Internally the line oscillator feeds a triangular waveform to the oscillator and flyback phase detector sections and the pulse width control section. The coincidence detector section is used to set the time constant of the oscillator phase detector circuit. It is fed internally with sync pulses from the sync separator section, and with line flyback pulses via pin 5. When the flyback pulses are out of phase with the sync pulses the impedance looking into pin 11 is high (21(Q). When the pulses are coincident the impedance falls to about 150Q and the oscillator phase detector circuit is then slow acting. The effect of this is to give fast pull -in when the pulses are out of sync and good noise immunity when they are in sync. The coincidence detector is controlled by the voltage on pin 10. When the sync and flyback pulses are in sync C3 is charged: when they are out of sync C3 discharges via R3. VTR use has been taken into consideration here. With a video recorder it is necessary to be able to follow the sync pulse phase variations that occur as a result of wow and flutter in the tape transport system, while noise is much less of a problem. For use with a VTR therefore the network on pin 10 can simply be left out so that the oscillator phase detector circuit is always fast acting. A second control loop is used to adjust the timing of the pulse output obtained from pin 2 to take into account the delay in the line output stage. The fly back phase detector compares the frequency of the flyback pulses fed in at pin 5 with the oscillator signal which has already been synchronised to the sync pulse frequency.
Any phase difference results in an output from pin 4 which is integrated and fed into the pulse width control section at pin 3. The potential at pin 3 sets the width of the output pulse obtained at pin 2: with a high positive voltage (via R11 and R12) at pin 3 a 1:1 mark -space ratio out- put pulse (32/us on, 32/us off) will be produced while a low potential at pin 3 (negative output at pin 4) will give a 16us output pulse at the same frequency. The action of this control loop continues until the fly- back pulses are in phase with a fixed point on the oscillator waveform: the flyback pulses are then in phase with the sync pulses and delays in the line output stage are compensated. The output obtained at pin 2 is of low impedance and is suitable for driving valves, transistors or thyristors: R9 is necessary to provide current limiting.