





The digital CHASSIS SCC-K43A-A (AE-4) was introduced by SONY in September 1996.
It's quite complex in all parts.
The power supply has the first place of complexity after the Digital Board Unit.
CHASSIS SCC-K43A-A (AE-4) Switching power supply circuit:A power supply circuit has a so-called composite resonance type switching converter equipped with a primary resonance circuit for forming a voltage resonance type converter at a primary side, and a secondary resonance circuit comprising a secondary winding and a secondary parallel resonance capacitor at a secondary side. The secondary side is equipped with active clamp means for stabilizing a DC output low voltage taken out from an intermediate tap of the secondary winding to control the conduction angle of an auxiliary main switching element in accordance with the level of the DC output low voltage, whereby the power loss due to the cross-regulation of the DC output low voltage can be reduced, and the power conversion efficiency can be enhanced.


1. A switching power supply circuit, characterized by comprising: switching means having a main switching element for conducting a switching operation on a DC input voltage and outputting a switching result; an insulating converter transformer that is designed so as to provide a coupling coefficient required for the loose coupling between a primary side and a secondary side, and transmits the output of said switching means achieved at the primary side to the secondary side; a primary parallel resonance circuit constructed by connecting a primary parallel resonance capacitor to a primary winding wound around said converter transformer in parallel equivalently; a first secondary parallel resonance circuit constructed by connecting a first secondary parallel resonance capacitor to a secondary winding wound around the insulating converter transformer in parallel; first DC output voltage generating means for receiving an alternating voltage achieved at said secondary winding wound around said insulating converter transformer and conducting a rectifying operation on the alternating voltage thus received to a DC output main voltage; first stabilized voltage control means for performing voltage-stabilizing control on the DC output main voltage by controlling the switching frequency and conduction angle of said main switching element in accordance with the level of the DC output main voltage; a second secondary parallel resonance circuit constructed by connecting, in parallel, a second secondary parallel resonance capacitor to the winding portion between an intermediate tap of said secondary winding wound around said insulating converter transformer and the earth at the secondary side; second DC output voltage generating means for receiving an alternating voltage achieved at the intermediate tap of said secondary winding wound around said insulating converter transformer and conducting a rectifying operation on the alternating voltage thus received to achieve a DC output low voltage; active clamp means constructed by connecting, in parallel, a series connection circuit comprising a clamp capacitor and an auxiliary switching element to the winding portion between the intermediate tap of said secondary winding wound around said insulating converter transformer and the earth at the secondary side; and second voltage-stabilizing control means for executing the conduction angle control of said auxiliary switching element in accordance with the level of the DC output low voltage to perform the voltage-stabilizing control on the DC output low voltage. 2. The switching power supply circuit as claimed in claim 1, wherein there are provided a plurality of constructing portions each of which comprises said second secondary parallel resonance circuit, said second DC output voltage generating means, said active clamp means and said second voltage-stabilizing control means.
BACKGROUND OF THE INVENTION

1. Field of the Invention
The present invention relates to a switching power supply circuit equipped to various types of equipment as a power supply source.
2. Description of the Related Art
The applicant of this application previously proposed a technique of constructing a composite resonance type converter as a switching power supply circuit by combining a voltage resonance type converter of one stone at a primary side and a half-wave rectifying type voltage resonance circuit at a secondary side, providing an active clamp circuit at the secondary side and stabilizing the DC output voltage thereof by controlling the conduction angle of the switching element of the active clamp circuit.
FIG. 10 is a circuit diagram of a conventional switching power supply circuit which can be constructed on the basis of the invention previously proposed by the applicant of this application.
In the power supply circuit shown in FIG. 10 , a full-wave rectifying circuit comprising a bridge rectifying circuit Di and a smoothing capacitor Ci is equipped as a rectifying and smoothing circuit to which commercial alternating power (alternating input voltage VAC) is input to achieve a DC input voltage, whereby the rectified and smoothed voltage Ei corresponding to the once level of the alternating input voltage VAC is achieved.
At the primary side of the power supply circuit, a self-excited type is constructed as a voltage resonance type converter circuit which carries out a single-end operation on the basis of a one-stone switching element Q 1 . In this case, a bipolar transistor having high resistance to voltage (BJT; junction type transistor) is used as the switching element Q 1 .
The base of the switching element Q 1 is connected to the anode of the smoothing capacitor Ci (rectified and smoothed voltage Ei) through a starting resistor Rs to achieve base current at the starting time from a rectifying and smoothing line.
A drive winding NB which is provided at the primary side of an insulating converter transformer PIT so as to have a turn number of 1T (turn), and a series resonance circuit for self-excited resonance driving which comprises a series an inductor LB, a resonance capacitor CB and a base current limiting resistor RB is connected between the base of the switching element Q 1 and the earth at the primary side. A switching frequency fs for turning on/off the switching element Q 1 is generated by the self-excited circuit. For example, the switching frequency fs is set to 66 KHz by the series resonance circuit.

A parallel resonance capacitor Cr is connected between the collector and emitter of the switching element Q 1 in parallel. In this case, a primary series resonance circuit of the voltage resonance type converter is formed by the capacitance of the parallel resonance capacitor Cr itself and the leakage inductance L 1 of the primary winding N 1 side of the insulating converter transformer PIT.
The insulating converter transformer PIT transmits the switching output of the switching element Q 1 to the secondary side. The insulating converter transformer PIT is equipped with an EE-type core comprising two E-type cores of ferrite material or the like which are assembled such that both the magnetic legs thereof are confronted to each other, and the primary winding N 1 and the secondary winding N 2 are wound around the center magnetic leg of the EE-type core by using a divisional bobbin so as to be separated from each other. Further, the EE-type core is assembled so that a gap is formed in the center magnetic leg thereof, whereby loose coupling based on a required coupling coefficient is achieved.
One end of the primary winding N 1 of the insulating converter transformer PIT is connected to the switching element Q 1 , and the other end thereof is connected to the anode of the smoothing capacitor Ci (rectified and smoothed voltage Ei). Accordingly, an alternating voltage having the period corresponding to the switching frequency occurs at the primary winding N 1 when the switching output of the switching element Q 1 is supplied to the primary winding Ni.
Further, at the secondary side of the insulating converter transformer PIT, an alternating voltage induced by the primary winding N 1 is generated at the secondary winding N 2 . In this case, a secondary parallel resonance capacitor C 2 is connected to the secondary winding N 2 in parallel, so that a parallel resonance circuit is formed by the leakage inductance L 2 of the secondary winding N 2 and the capacitance of the secondary parallel resonance capacitor C 2 . The parallel resonance circuit sets the alternating voltage induced in the secondary winding N 2 to a resonance voltage, so that a voltage resonance operation can be achieved at the secondary side. That is, the power supply circuit described above has the construction of a “composite resonance type switching converter” in which a parallel resonance circuit for setting the switching operation to a voltage resonance type is provided at the primary side and a parallel resonance circuit for achieving the voltage resonance operation is provided at the secondary side.
The secondary side of the power supply circuit thus constructed is equipped with a half-wave rectifying circuit comprising a secondary rectifying diode D 01 and a smoothing capacitor C 01 2 , thereby achieving a main secondary DC output voltage E 01 corresponding to substantially the once level as the alternating voltage induced in the secondary winding N 2 . which are connected to the secondary winding N
Further, in this case, an intermediate tap is provided to the secondary winding N 2 , and a half-wave rectifying circuit comprising a rectifying diode D 02 and a smoothing capacitor C 02 is connected to the winding between the tap output line of the secondary winding N 2 and the earth at the secondary side as shown in FIG. 10 to generate and output a low secondary DC output voltage E 02 .
In the power supply circuit, an active clamp circuit is equipped to the secondary side. That is, an auxiliary switching element Q 2 of MOS-FET, a clamp capacitor C 3 and a clamp diode DD 2 are equipped as the secondary active clamp circuit. Further, a drive winding Ng 1 , a capacitor Cg 1 1 are equipped as a driving circuit system for driving the auxiliary switching element Q 2 . and a resistor Rg
A clamp diode DD 2 is connected between the drain and source of the auxiliary switching element Q 2 in parallel. As a connection manner, the anode of the clamp diode DD 2 is connected to the source, and the cathode is connected to the drain.
The drain of the auxiliary switching element Q 2 is connected to the connection point between the tap output line of the secondary winding N 2 and the anode of the rectifying diode D 02 3 . Further, the source of the auxiliary switching element Q 2 is connected to the earth at the secondary side. through a clamp capacitor C
Accordingly, the secondary active clamp circuit is constructed by connecting the clamp capacitor C 3 to the parallel connection circuit comprising the auxiliary switching element Q 2 and the clamp diode DD 2 in series. The circuit thus formed is further connected to the secondary winding N 2 in parallel.

Accordingly, the voltage induced by the alternating voltage achieved at the primary winding N 1 1 . Further, in this case, voltages achieved at the secondary winding N 2 and the drive winding Ng 1 are opposite in polarity because of the relationship of the winding direction between the windings N 2 and Ng 1 . occurs at the drive winding Ng
In this embodiment, PWM control is carried out on the switching operation of the auxiliary switching element Q 2 by a control circuit 1 equipped to the secondary side. That is, the secondary DC output voltage E 01 , E 02 is supplied to the control circuit of an error amplifier, and the control circuit 1 applies the DC control voltage corresponding to E 01 , E 02 to the gate of the auxiliary switching element Q 2 to control the conduction angle of the auxiliary switching element Q 2 , whereby the DC output voltage is stabilized with respect to variations of the alternating input voltage VAC and the load power Po. For example, the main DC output voltage E 01 is stabilized to 135V.
In the circuit construction described above, the insulating converter transformer PIT may be EE-40 under the condition that the gap is set to 1 mm, the number of turns of the primary winding N 1 is set to 50T, the number of turns of the secondary winding N 2 is set to 55T and the number of turns of the drive winding NB=Ng 1 is set to 1T. Further, the resistance of the starting resistor Rs is set to 330 KΩ, the resistance of the resistor RB is set to 1Ω, the capacitance of the capacitor CB is set to 0.33 μF, the inductance of the inductor LB is set to 10 μH, the capacitance of the resonance capacitor Cr is set to 0.012 μF, the resistance of the resistor Rg 1 is set to 10Ω, the capacitance of the resonance capacitor C 2 is set to 0.012 μF, the capacitance of the clamp capacitor C 3 is set to 0.47 μF, and the switching frequency fs is equal to 66 KHz.
FIG. 11 shows the operation waveforms of the respective parts at the alternating input voltage VAC of 100V and the load power Po of 200 W. FIG. 12 shows the operation waveforms of the respective parts under no load and at the alternating input voltage VAC of 100V. It is apparent from FIGS. 11 and 12 that the conduction angle (TON period) of the auxiliary switching element Q 2 is controlled in accordance with the variation of the load power Po.
FIG. 13 shows the characteristic of the conduction angle (TON) and the AC/DC power conversion efficiency ηAC/DC with the variation of the load power Po, and FIG. 14 shows the characteristic of the conduction angle (TON) and the AC/DC power conversion efficiency ηAC/DC with the variation of the alternating input voltage VAC. As is apparent from FIGS. 13 and 14 , the conduction angle (TON) of the auxiliary switching element Q 2 with respect to the variation of the load power Po and the alternating input voltage VAC is controlled over the range from 4.6 μs to 13 μs.
As the conduction angle (TON) is increased due to reduction of the load power Po or increase of the alternating input voltage VAC, the conduction loss of the auxiliary switching element Q 2 is increased and thus the AC/DC power conversion efficiency (ηAC/DC) is lowered.
Further, the primary side voltage resonance pulse voltage V 1 occurring between both the ends of the main switching element Q 1 is equal to 530V to 850V when the alternating input voltage VAC ranges from 90V to 144V, and thus the main switching element Q 1 is required to have a voltage resistance to 900V. Further, the clamp voltage V 2 at the secondary side is equal to 160V to 350V, and thus the auxiliary switching element Q 2 is required to have a voltage resistance to 400V.
Current having a saw-tooth waveform flows in the switching elements Q 1 , Q 2 under the no-load state as indicated by current IQ 1 , IC 3 in FIG. 7 . Therefore, these large amounts of current flow in the primary winding N 1 , the secondary winding N 2 of the insulating converter transformer PIT and each switching element Q 1 , Q 2 , so that invalid current is increased and the input power at this time is equal to 13.5 W.
When stabilization is carried out on the main voltage (DC output main voltage) E 01 =135V with respect to the variations of the alternating input voltage VAC and the load current on the basis of the conduction angle control of the auxiliary switching element Q 2 of the secondary active clamp circuit, the auxiliary DC output voltage (DC output low voltage) E 02 , which is equal to 15V for example, exhibits cross regulation of 15V±1.5V.
When the load current of the DC output low voltage E 02 is varied by 0.5 A to 1.5 A, the cross regulation is further magnified to 15V±2.5V.
Therefore, in order to achieve a voltage-stabilized output voltage of 12 V with a three-terminal regulator having a low saturation voltage, the power loss of (17.5−12.0)×1.5=8.25 w at maximum occurs and thus the power conversion efficiency is further lowered.
As is understood from the foregoing description, the following problems (1) to (4) occur in the construction of the power supply circuit of FIG. 10 as described above, that is, in the construction in which the switching frequency of the auxiliary switching element Q 2 of the active clamp circuit is fixed and the DC output voltage is stabilized by controlling the conduction angle.
(1) the conduction time of the secondary auxiliary switching element Q 2 is increased due to reduction of the load power Po and increase of the alternating input voltage VAC, and thus the power loss is also increased, resulting in reduction in efficiency.
(2) The peak value of the voltage resonance pulse voltage VI occurring in the primary switching element Q 1 increases in proportion to the alternating input voltage VAC, so that the switching element Q 1 has a voltage resistance to 900V in the AC 100V system and a voltage resistance to 1800V in the AC 200V system. Therefore, an expensive switching element Q 1 must be prepared.
(3) Under the no-load state, the invalid power is large, and the voltage resonance pulse voltage V 1 is larger than under a load-applied state, so that a heat radiating plate is needed to the auxiliary switching element Q 2 .
(4) Since the cross regulation of the DC output lower voltage E 02 taken out from the secondary side is large, a three-terminal series regulator is required to stabilize the DC output low voltage E 02 , and thus the power loss is further increased. Therefore, the power conversion efficiency is lowered.
SUMMARY OF THE INVENTION
Therefore, in consideration of the foregoing problems, according to the present invention, there is provided a switching power supply circuit comprising: switching means having a main switching element for conducting a switching operation on a DC input voltage and outputting a switching result; an insulating converter transformer that is designed so as to provide a coupling coefficient required for the loose coupling between a primary side and a secondary side, and transmits the output of the switching means achieved at the primary side to the secondary side; a primary parallel resonance circuit constructed by connecting a primary parallel resonance capacitor to a primary winding wound around the converter transformer equivalently and in parallel; a first secondary parallel resonance circuit constructed by connecting a first secondary parallel resonance capacitor to a secondary winding wound around the insulating converter transformer in parallel; first DC output voltage generating means for receiving an alternating voltage achieved at the secondary winding wound around the insulating converter transformer and conducting a rectifying operation on the alternating voltage thus received to a DC output main voltage; first stabilized voltage control means for performing voltage-stabilizing control on the DC output main voltage by controlling the switching frequency and conduction angle of the main switching element in accordance with the level of the DC output main voltage; a second secondary parallel resonance circuit constructed by connecting, in parallel, a second secondary parallel resonance capacitor to the winding portion between an intermediate tap of the secondary winding wound around the insulating converter transformer and the earth at the secondary side; second DC output voltage generating means for receiving an alternating voltage achieved at the intermediate tap of the secondary winding wound around the insulating converter transformer and conducting a rectifying operation on the alternating voltage thus received to achieve a DC output low voltage; active clamp means constructed b
In the switching power supply circuit thus constructed, there is achieved a so-called composite resonance type switching converter in which the primary resonance circuit to form the voltage resonance type converter is provided at the primary side, and the secondary resonance circuit comprising the secondary winding and the secondary parallel resonance capacitor is provided at the secondary side. On the basis of this construction, the active clamp means for stabilizing the DC output low voltage taken from the intermediate tap of the secondary winding is provided at the secondary side, and the conduction angle of the auxiliary main switching element is controlled in accordance with the level of the DC output low voltage, whereby the power loss due to the cross regulation of the DC output low voltage can be reduced and the power conversion efficiency can be enhanced.
BRIEF DESCRIPTION OF THE DRAWINGS
FIG. 1 is a circuit diagram showing the construction of a switching power supply circuit according to an embodiment of the present invention;FIG. 2 is a cross-sectional view showing the construction of an insulating converter transformer;
FIGS. 3A and 3B is an equivalent circuit diagram showing each operation when mutual inductance is equal to +M/−M;
FIG. 4 is a waveform diagram showing the operation of the main part in the power supply circuit of the embodiment of the present invention;
FIG. 5 is a waveform diagram showing the operation of the main part in the power supply circuit of the embodiment of the present invention;
FIG. 6 is a diagram showing characteristics of the power supply circuit of the embodiment with respect to variation of load power;
FIG. 7 is a diagram showing characteristics of the power supply circuit of the embodiment with respect to variation of load power;
FIG. 8 is a circuit diagram showing the construction of a switching power supply circuit according to another embodiment of the present invention;
FIG. 9 is a circuit diagram showing the construction of a switching power supply circuit according to another embodiment of the present invention;

FIG. 11 is a waveform diagram showing the operation of the main part of the conventional switching power supply circuit;


FIG. 14 is a diagram showing the characteristics of the power conversion efficiency and the conduction angle control with respect to variation of an alternating input voltage in the conventional power supply circuit.
DETAILED DESCRIPTION OF THE PREFERRED EMBODIMENTS
Preferred embodiments according to the present invention will be described hereunder with reference to the accompanying drawings.FIG. 1 shows the construction of a switching power supply circuit according to an embodiment of the present invention.

A one-stone switching element Q 1 is equipped as a switching converter for receiving and intermitting the rectified and smoothed voltage Ei (DC input voltage), thereby providing a voltage resonance type converter for performing a switching operation based on a single end system.
In this case, a self-excited type is adopted as the voltage resonance type converter which performs the single end operation with a one-stone switching element Q 1 . A bipolar transistor having a high voltage resistance (BJT: junction type transistor) is used for the switching element Q 1 .
A series resonance circuit for self-excited driving which comprises a series connection circuit of a driving winding NB, a resonance capacitor CB and a base current limiting resistor RB is connected between the base of the switching element Q 1 and the earth at the primary side.
Further, a route for clamp current which flows when the switching element Q 1 is turned off is formed by a clamp diode DD inserted between the base of the switching element Q 1 and the cathode of the smoothing capacitor Ci (the earth at the primary side). A starting resistor RS is inserted to achieve the base current at the starting time from a rectifying and smoothing line.
A parallel resonance capacitor Cr is connected in parallel between the collector and emitter of the switching element Q 1 . A primary parallel resonance circuit of the voltage resonance type converter is formed by the capacitance of the parallel resonance capacitor Cr itself and the leakage inductance L 1 of the primary winding N 1 side of the insulating converter transformer PIT.
An orthogonal control transformer PRT shown in FIG. 1 is a saturable reactor around which a resonance current detecting winding ND, a driving winding NB and a control winding NC are wound. The orthogonal control transformer PRT is used to drive the switching element Q 1 and perform voltage-stabilizing control. As shown in FIG. 1 , the resonance current detecting winding ND and the driving winding NB are wound around the orthogonal control transformer PRT, and also the control winding NC is wound around the orthogonal control transformer PRT in the direction orthogonal to the winding direction of the resonance current detecting winding ND and the driving winding NB.
In the orthogonal control transformer PRT, the switching output achieved at the resonance current detecting winding ND is induced in the driving winding NB through trans-coupling, whereby drive current is output from the series resonance circuit (NB, CB) forming a self-excited oscillation circuit through the base current limiting resistor RB to the base of the switching element Q 1 , whereby the switching element Q 1 carries out the switching operation at the switching frequency determined on the basis of the resonance frequency of the series resonance circuit. The switching output achieved at the collector of the switching element Q 1 is transferred to the primary winding N 1 of the insulating converter transformer PIT.
The insulating converter transformer PIT is provided to transfer the switching output of the switching converter achieved at the primary side to the secondary side.

The gap G can be formed by making the center magnetic leg of each of the E-type cores CR 1 , CR 2 shorter than the two outer magnetic legs thereof. Further, the coupling coefficient k is set to about 0.7 to 0.8 so that loose coupling can be attained, and thus it is harder to achieve the saturation state.
As shown in FIG. 1 , the winding-starting end portion of the primary winding N 1 of the insulating converter transformer PIT is connected to the collector of the switching element Q 1 , and the winding-ending end portion is connected to the anode of the smoothing capacitor Ci (rectified and smoothed voltage Ei) through the detecting winding ND. Accordingly, the switching output of the switching element Q 1 is supplied to the primary winding N 1 , thereby generating an alternating voltage having the period corresponding to the switching frequency.
The alternating voltage induced by the primary winding N 1 occurs in the secondary winding N 2 2 is connected to the secondary winding N 2 in parallel, so that a first parallel resonance circuit is formed by the leakage inductance L 2 of the secondary winding N 2 and the capacitance of the secondary parallel resonance capacitor C 2 . The parallel resonance circuit sets the alternating voltage induced in the secondary winding N 2 to a resonance voltage, and thus the voltage resonance operation is performed at the secondary side. That is, the power supply circuit of this embodiment has the construction of a “composite resonance type switching converter” in which a parallel resonance circuit for setting the switching operation to a voltage resonance type is provided at the primary side, and also a parallel resonance circuit for achieving the voltage resonance operation is provided at the secondary side. at the secondary side of the insulating converter transformer PT. In this case, the secondary parallel resonance capacitor C
At the secondary side of the power supply circuit thus formed, a rectifying diode D 01 and a smoothing capacitor C 01 is connected to the secondary parallel resonance circuit comprising the secondary winding N 2 and the secondary parallel resonance capacitor C 2 in a connection style shown in FIG. 1 to thereby form a half-wave rectifying circuit, and a secondary DC output main voltage E 01 is mainly generated by the half-wave rectifying circuit (D 01 , C 01 ). The secondary DC output main voltage E 01 is equal to about 135V, for example.
The secondary DC output main voltage E 01 is branched and input to a control circuit 1 A, and the control circuit 1 A generates a control signal to stabilize the DC output main voltage E 01 .
That is, in the control circuit 1 A, the level of the control current (DC current) flowing in the control winding NC is varied in accordance with variation of the level of the DC output main voltage E 01 . Accordingly, the inductance LB of the driving winding NB is variable, and the resonance frequency of the series resonance circuit in the self-excited oscillation driving circuit, that is, the switching frequency of the switching element Q 1 is variably controlled, thereby stabilizing the DC output main voltage E 01 .
Here, when the switching frequency is variably controlled, the period TOFF during which the switching element Q 1 is off is set to a fixed value, and under this condition, the period TON during which the switching element Q 1 is on is variably controlled. In this specification, such composite control as described above will be referred to as “composite control system”.
With respect to the operation at the secondary side of the insulating converter transformer PIT, two cases where the mutual inductance M between the inductance L 1 of the primary winding N 1 and the inductance L 2 of the secondary winding N 2 is equal to +M (additive polarity) and where the mutual inductance M is equal to −M (subtractive polarity) exist in accordance with the polarities (winding direction) of the primary winding N 1 and the secondary winding N 2 , the connection relationship between the rectifying diodes D 01 , D 02 and the polarity variation of the alternating voltage excited in the secondary winding N 2 .
For example, when it is equivalent to the circuit shown in FIG. 3A , the mutual inductance M is equal to +M, and when it is equivalent to the circuit shown in FIG. 3B , the mutual inductance M is equal to −M.
Comparing this operation with the operation at the secondary side shown in FIG. 1 , when the alternating voltage achieved at the secondary winding N 2 has positive polarity, the rectified current flows in the secondary rectifying diode (D 01 ) in the half-wave rectifying circuit of the secondary side, and thus this operation can be regarded as an operation mode of +M (forward operation).
The polarities of the primary winding N 1 and the secondary winding N 2 of the insulating converter transformer PIT may be the additive polarity coupling or the subtractive polarity coupling. Further, the winding directions of the primary winding N 1 and the secondary winding N 2 are set to be the same or opposite to each other. In any case, the coupling coefficient is set to 0.7 to 0.8 to achieve the loose coupling.
In the power supply circuit of this embodiment, a tap output is provided to the secondary winding N 2 at the secondary side of the insulating converter transformer PIT as shown in FIG. 1 2 and the earth at the secondary side is set to N 3 . Further, a secondary parallel resonance capacitor C 4 is connected to the winding N 3 between the tap output line and the earth at the secondary side in parallel, so that a second parallel resonance circuit is formed by the leakage inductance L 3 of the winding portion having the winding number N 3 and the capacitance of the secondary parallel resonance capacitor C 4 . . The number of turns of the winding portion between the tap of the secondary winding N
Further, a rectifying diode D 02 and a smoothing capacitor C 02 are connected to the secondary parallel resonance circuit in the connection manner as shown in FIG. 1 to thereby form the half-wave rectifying circuit. An auxiliary DC output voltage, that is, a secondary DC output low voltage E 02 is generated by the half-wave rectifying circuit (D 02 , C 02 ). The secondary DC output low voltage E 02 is set to about 12V, for example.
In the power supply circuit described above, an active clamp circuit is provided at the secondary side. That is, an auxiliary switching element Q 2 of MOS-FET, a clamp capacitor C 3 and a clamp diode DD 2 of a body diode are equipped as the secondary active clamp circuit. Further, a drive winding Ng 1 , a capacitor Cg 1 and a resistor Rg 1 are equipped as a driving circuit system for driving the auxiliary switching element Q 2 .
The clamp diode DD 2 is connected between the drain and source of the auxiliary switching element Q 2 in parallel. The connection style is set so that the anode of the clamp diode DD 2 is connected to the source and the cathode thereof is connected to the drain.
The drain of the auxiliary switching element Q 2 is connected to the connection point between the tap output line of the secondary winding N 2 and the anode of the rectifying diode D 02 3 . The source of the auxiliary switching element Q 2 is connected to the earth at the secondary side. through the clamp capacitor C
Accordingly, the active clamp circuit is constructed by connecting the clamp capacitor C 3 to the parallel connection circuit of the auxiliary switching element Q 2 and the clamp diode DD 2 in series. The circuit thus formed is further connected to the winding portion (winding N 3 ) extending from the intermediate tap of the secondary winding N 2 to the earth at the secondary side in parallel.

In this case, the drive winding Ng 1 is formed at the winding-start end portion side of the secondary winding N 2 , and the number of turns thereof is set to 1T (turn). Accordingly, a voltage induced by the alternating voltage achieved in the primary winding N 2 occurs in the drive winding Ng 1 . In this case, the voltages having the opposite polarities are achieved at the secondary winding N 2 and the drive winding Ng 1 in view of the winding-direction relationship therebetween. The operation of the drive winding Ng 1 is guaranteed if the number of turns thereof is equal to 1T, however, it is not limited to this value.
In this embodiment, the switching operation of the auxiliary switching element Q 2 is subjected to the PWM control by a control circuit 1 B equipped at the secondary side. That is, the secondary DC output low voltage E 02 is supplied to the control circuit 1 B of the error amplifier, and the control circuit 1 B applies the DC control voltage corresponding to the voltage E 02 to the gate of the auxiliary switching element Q 2 to control the conduction angle of the auxiliary switching element Q 2 , whereby the DC output low voltage E 02 is stabilized with respect to the variations of the alternating input voltage VAC and the load power Po.
The power supply circuit thus constructed was tested under the condition that the resonance capacitor Cr=8200 pF, the resonance capacitor C 2 =8200 pF, the resonance capacitor C 4 =0.1 μF, the clamp capacitor C 3 =3.3 μF, and an auxiliary low on-resistance MOS-FET having a voltage resistance to 5 A/50V was used as the auxiliary switching element Q 2 .


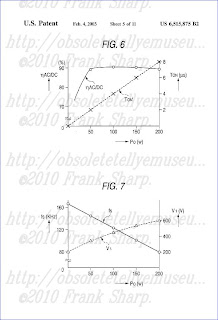
As is apparent from FIGS. 4 and 5 , with respect to the main switching element Q 1 , the switching frequency fs and the conduction angle TON are subjected to composite control, and with respect to the auxiliary switching element Q 2 , the conduction angle (TON′) is controlled.
As is apparent from the comparison between FIGS. 6 , 7 and FIG. 13 for the prior art, this embodiment enhances the AC/DC power conversion efficiency ηAC/DC to 90% or more when the power load Po ranges from 50 W to 200 W.
The resonance voltage V 1 is equal to 750V at the alternating input voltage VAC of 144V, and a product having a voltage resistance to 800V may be used as the switching element Q 1 . In the AC 200V system, a product having a voltage resistance to 1500V may be used.
With respect to the conduction angle (TON′) control of the auxiliary switching element Q 2 , in order to stabilize the cross-regulation voltage 12.5V to 17.5V of the DC output low voltage E 02 2 is equal to about 2 W when the load current of the DC output low voltage E 02 is equal to 1.5 A, and thus the power loss can be reduced by 6.25 W as compared with the power loss (8.25 W) of the prior art. =15V±2.5V to 12V, the control range may be set to 4 μs to 1 μs, and thus the control range is slight. The power loss of the auxiliary switching element Q
FIG. 8 shows a switching power supply circuit according to a second embodiment of the present invention.
FIG. 8 shows a case where the switching element Q 1 at the primary side is formed of MOS-FET and a separate excitation type oscillating circuit based on IC is provided in connection with the switching element Q 1 . The same elements as shown in FIG. 1 are represented by the same reference numerals, and the description thereof is omitted.
In this case, a one-stone switching element Q 1 is equipped as a switching converter for receiving and intermitting the rectified and smoothed voltage Ei (DC input voltage), and a voltage resonance type converter for performing a so-called single end type switching operation is provided.
The voltage resonance type converter of this embodiment adopts the separate excitation type construction. The drain of the switching element Q 1 of MOS-FET is connected to the anode of the smoothing capacitor Ci through the primary winding N 1 of the insulating converter transformer PIT, and the source of the switching element Q 1 of MOS-FET is connected to the earth at the primary side.
A parallel resonance capacitor Cr is connected between the drain and source of the switching element Q 1 in parallel. A primary parallel resonance circuit is formed by the capacitance of the parallel resonance capacitor Cr and the leakage inductance achieved at the primary winding N 1 1 , whereby the switching operation of the switching element Q 1 is made to be based on the voltage resonance style. of the insulating converter transformer PIT. The resonance operation of the parallel resonance circuit is achieved in accordance with the switching operation of the switching element Q
Further, a clamp diode DD 1 based on a so-called body diode equipped to MOS-FET is connected in parallel between the drain and source of the switching element Q 1 , thereby forming a route for clamp current flowing during the period when the switching element is turned off.
The switching element Q 1 is driven to carry out the switching operation, for example, by a switching driving portion 10 comprising an integrated circuit (IC) integrally equipped with an oscillation circuit 2 and a drive circuit 3 .
The switching driving portion 10 is connected to the line for the rectified and smoothed voltage Ei through a starting resistor Rs. For example when a power source voltage is applied to the switching driving portion 10 through the starting resistor Rs at the power source turn-on time, the switching driving portion 10 is actuated.
The oscillation circuit 2 of the switching driving portion 10 carries out the oscillation operation having the frequency based on a control signal from the control circuit 1 A to output an oscillation signal. The oscillation signal is converted to a drive voltage in the drive circuit 3 , and output to the gate of the switching element Q 1 , whereby the switching element Q 1 is allowed to carry out the switching operation based on the oscillation signal generated in the oscillation circuit 2 . Accordingly, the switching frequency of the switching element Q 1 and the duty of the on/off period in one switching period is dependently determined on the basis of the oscillation signal generated in the oscillation circuit 2 .
The oscillation frequency of the oscillation circuit 2 is set so that the control circuit 1 A is varied in accordance with variation of the level of the DC output main voltage E 01 . That is, the switching frequency and conduction angle of the switching element Q 1 is variably controlled in accordance with the level of the DC output main voltage E 01 , thereby stabilizing the DC output main voltage E 01 .
At the secondary side of the insulating converter transformer PIT, DC output low voltages E 02 , E 03 of two systems are achieved in addition to the DC output main voltage E 01 .
That is, two tap outputs are provided to the secondary winding N 2 as shown in FIG. 8 (the winding portion between the first tap of the secondary winding N 2 and the earth at the secondary side is represented by N 3 and the winding portion between the second tap of the secondary winding N 2 and the earth at the secondary side is represented by N 4 ).
Like the case of FIG. 1 , a parallel resonance capacitor C 4 is connected to the winding N 3 in parallel, and a parallel resonance circuit is formed by the leakage inductance of the winding N 3 4 , and further a rectifying diode D 02 and a smoothing capacitor C 02 are connected to each other in the connection manner

PIT, Like the circuit construction for the winding N 3 , a parallel resonance capacitor C 5 is connected to the winding N 4 in parallel, and a parallel resonance circuit is formed by the leakage inductance of the winding N 4 and the capacitance of the secondary parallel resonance capacitor C 5 . Further, a rectifying diode D 03 and a smoothing capacitor C 03 are connected to each other in the connection manner shown in FIG. 8 to form a half-wave rectifying circuit. The DC output low voltage E 03 is generated by the half-wave rectifying circuit (D 03 , C 03 ). The secondary DC output low voltage E 03 is set to about 5V, for example.
In the power supply circuit, an active clamp circuit is equipped to each of the DC output low voltage E 02 and E 03 lines.
An auxiliary switching element Q 2 of MOS-FET, a clamp capacitor C 3 and a clamp diode DD 2 02 line. Further, a driving circuit system for driving the auxiliary switching element Q 2 comprises a drive winding Ng 1 , a capacitor Cg 1 and a resistor Rg 1 The active clamp circuit is constructed by connecting the series connection circuit of the auxiliary switching element Q 2 and the clamp capacitor C 3 to the winding N 3 in parallel. of a body diode are provided as the active clamp circuit for the DC output low voltage E
The switching operation of the auxiliary switching element Q 2 is subjected to the PWM control by the control circuit 1 B. That is, the secondary DC output low voltage E 02 is supplied to the control circuit 1 B of the error amplifier, and the controller 1 B applies the corresponding DC control voltage to the gate of the auxiliary switching element Q 2 to control the conduction angle of the auxiliary switching element Q 2 , whereby the DC output low voltage E 02 is stabilized with respect to the variations of the alternating input voltage VAC and the load power Po.
The active clamp circuit for the DC output low voltage E 03 line is equipped with an auxiliary switching element Q 3 of MOS-FET, a clamp capacitor C 6 and a clamp diode DD 3 of a body diode. A driving system for the auxiliary switching element Q 3 comprises the drive winding Ng 1 2 ), a capacitor Cg 2 and a resistor Rg 2 . The active clamp circuit is constructed by connecting the series connection circuit of the auxiliary switching element Q 3 and the clamp capacitor C 6 to the winding N 4 in parallel. (commonly used with the driving system of the auxiliary switching element Q
Further, the switching operation of the auxiliary switching element Q 3 is subjected to the PWM control by a control circuit iC. That is, the secondary DC output low voltage E 03 is supplied to the control circuit iC of the error amplifier, and the control circuit iC applies the corresponding DC control voltage to the gate of the auxiliary switching element Q 3 to control the conduction angle of the auxiliary switching element Q 3 , whereby the DC output low voltage E 03 is stabilized with respect to the variations of the alternating input voltage VAC and the load power Po.
FIG. 9 shows a switching power supply circuit according to a third embodiment of the present invention. In this embodiment, the construction of the primary side of the insulating converter transformer PIT is the same as shown in
FIG. 1 . With respect to the construction of the secondary side, the connection manner of each element is the same as the embodiment of FIG. 8 , however, the windings N 3 and N 4 are provided separately from the secondary winding N 2 . The drive winding Ng 1 is formed at the winding-start end portion of the winding N 3 by 1T, for example. This embodiment is suitably applied to a case where the output current of the DC output low voltage E 02 , E 03 is equal to a large current value such as 2 A or more.

In the second and third embodiments, the insulating converter transformer PIT can be implemented in any combination case where the polarities of the primary winding N 1 and the secondary winding N 2 are in additive polarity relationship or subtractive polarity relationship and the winding directions thereof are the same (coaxial) or opposite to each other.
The foregoing description is made on the power supply circuit according to the embodiments of the present invention. However, the present invention is not limited to the above-described embodiments. For example, the main switching element Q 1 is not limited to the bipolar transistor, and it may be formed of MOS-FET, BJT, IGBT or the like. The auxiliary switching element Q 2 may be formed of BJT, IGBT or the like. Further, another element such as SIT (Static Induction Thyristor) or the like may be used.
The secondary rectifying circuit formed so as to contain the secondary resonance circuit is also not limited to the construction of the above-described embodiments, and another circuit construction may be adopted.
As is understood from the foregoing description, in the composite resonance type switching converter having the active clamp means at the secondary side, the AC/DC power conversion efficiency can be enhanced. Particularly, the invalid power when the load power is below ½ (i.e., under a light load) can be reduced. For example, the invalid power can be reduced by about 4 W at the load power of 200 W, and it can be reduced by 11 W under no-load state.
Further, the power loss to stabilize the voltage due to the cross-regulation (voltage variation) of the DC output low voltage can be greatly reduced.
Still further, the voltage resistance of the main switching element can be reduced from 900V to 800V in the case of AC 100V system, and from 1800V to 1500V in the case of AC 200V system. Further, the voltage resistance of the auxiliary switching element can be reduced from 400V to 50V. From this effect, enhancement of the switching characteristics and reduction of the cost of the power supply circuit can be promoted.
SONY TRINITRON CONVERGENCE DEFLECTING DEVICE FOR SINGLE-GUN, PLURAL-BEAM COLOR PICTURE TUBE In a color picture tube of the single-gun, plural-beam type in which a central beam and two side beams originate in a common horizontal plane and are all made to pass through the center of an electron lens for focussing the beams on the color screen with the central beam emerging from the lens along the optical axis of the latter and the side beams emerging from the lens along paths that are oppositely divergent from the axis, the divergent side beams are acted upon by an electrostatic convergence deflecting device constituted by pairs of horizontally spaced plates arranged along the divergent paths and having voltages applied thereacross to produce electric fields by which the divergent side beams passing therethrough are deflected to converge at a common spot with the central beam on the apertured grill or mask associated with the screen, and a main deflection yoke produces magnetic fields by which the beams are deflected horizontally and vertically, respectively, for causing the beams to scan the screen; the horizontal distances between the plates of each pair are varied in the vertical direction from a maximum at the common horizontal plane to minimums at the opposed edges of the plates remote from such common plane so as to correspondingly vary the strengths of the electric fields and thus correct distortions in the rasters of the side beams.

In single-gun, plural-beam color picture tubes of the described type, for example, as specifically disclosed in U.S. Pat. No. 3,448,316, issued June 3, 1969, and having a common assignee herewith, three laterally spaced electron beams are emitted by a beam generating or cathode assmebly and directed in a common substantially horizontal plane with the central beam coinciding with the optical axis of the single electron focussing lens and the two outer or side beams being converged to cross the central beam at the optical center of the lens and thus emerge from the latter along paths that are divergent from the optical axis. Arranged along such divergent paths are respective pairs of convergence deflecting plates constituting a convergence deflecting device and having voltages applied thereacross to produce electric fields which laterally deflect the divergent beams in a substantially horizontal plane for causing all beams to converge at a common spot on the apertured beam selecting grill or shadow mask associated with the color screen. Further, arranged between the convergence de

Accordingly, it is an object of this invention to provide a single-gun, plural-beam color picture tube in which the rasters of the several beams are free of distortion with respect to each other.
Another object is to provide a single-gun, plural-beam color picture tube in which distortions of the rasters of the several beams are avoided by a particular construction of the convergence deflecting device.
In accordance with an aspect of the invention, the described distortions of the rasters of the side beams with respect to the raster of the central beam are avoided by suitably varying, in the direction perpendicular to the common plane in which the beams originate, the distances between the paired plates of the convergence deflecting device, whereby to correspondingly vary the strengths of the electric fields between such plates by which the side beams are convergently deflected.
The above, and other objects, features and advantages of this invention, will be apparent in the following detailed description of illustrative embodiments which is to be read in connection with the accompanying drawing, wherein:
FIG. 1 is a schematic sectional view in a horizontal plane passing through the axis of a single-gun, plural-beam color picture tube of the type to which this invention is preferably applied;
FIG. 2 is a diagrammatic view to which reference is hereinafter made in explaining the invention;
FIG. 3 is a diagrammatic view showing the possible relative distortions of the rasters of the several beams, as seen from the viewer's side of the tube screen, and which are to be avoided by this invention;
FIG. 4 is a diagrammatic, transverse sectional view through the convergence deflecting device of a color picture tube according to a first embodiment of this invention; and
FIGS. 5-8 are views similar to FIG. 4, but showing other embodiments of the invention.

For operation of the electron gun A of FIG. 1, appropriate voltages are applied to the grids G 1 2 and to the electrodes G 3 , G 4 and G 5 . Thus, for example, a voltage of 0 to minus 400V is applied to the grid G 1 , a voltage of 0 to 500V is applied to the grid G 2 , a voltage of 13 to 20KV is applied to the electrodes G 3 and G 5 , and a voltage of 0 to 400V is applied to the electrode G 4 , with all of these voltages being based upon the cathode voltage as a reference. As a result, the voltage distributions between the respective electrodes and cathodes, and the respective lengths and diameters thereof, may be substantially identical with those of a unipotential-single beam type electron gun which is constituted by a single cathode and first and second, single-apertured grids. and G
With the applied voltage distribution as described hereinabove, an electron lens field will be established between grid G 2 and the electrode G 3 to form an auxiliary lens L' as indicated in dashed lines, and an electron lens field will be established around the axis of electrode G 4 , by the electrodes G 3 , G 4 and G 5 , to form a main lens L, again as indicated in dashed lines. In a typical use of electron gun A, bias voltages of 100V, 0V, 300V, 20KV, 200V and 20V may be applied respectively to the cathodes K R , K G and K B , the first and second grids G 1 and G 2 and the electrodes G 3 , G 4 and G 5 .
Further included in the electron gun A of FIG. 1 and electron beam convergence deflecting means F which comprise inner shielding plates P and P' disposed in the depicted spaced, relationship at opposite sides of the gun axis, and axially extending, deflector plates Q and Q' which are disposed, as shown, in outwardly spaced, opposed relationship to shielding plates P and P', respectively. Although depicted as substantially straight, it is to be understood that the deflector plates Q and Q' may, alternatively, be somewhat curved or outwardly bowed, as is well known in the art.
The shielding plates P and P' are equally charged and disposed so that the central electron beam B G will pass substantially undeflected therebetween, while the deflector plates Q and Q' have negative charges with respect to the plates P and P' so that electron beams B B and B R will be convergently deflected as shown by the respective passages thereof between the plates P and Q and the plates P' and Q'. More specifically, a voltage V P which is equal to the voltage applied to the electrode G 5 , may be applied to both shielding plates P and P', and a voltage V Q , which is some 200 to 300V lower than the voltage V P , is applied to the plates Q and Q' to result in the plates P and P' being at the same potential, and in the application of a deflecting voltage difference or convergence deflecting voltages V C between the plates P' and Q' and the plates P and Q and it is, of course, this convergence deflecting voltage V C which will impart the requisite convergent deflection to the electron beams B B and B R .

The voltage V P may also be applied to the lens electrodes G 3 and G 5 and to the screen S as an anode voltage as well as to the aperture grill G p . Electron beam scanning of the face of the color phosphor screen is effected in conventional manner, for example, main deflection yoke means indicated in broken lines at D and which receives horizontal and vertical sweep signals to produce horizontal and vertical deflection fields by which the beams are made to scan the screen for providing a color picture thereon. Since, with this arrangement

In the color picture tube as illustrated on FIG. 1, plates P and P' and plates Q and Q' are shown flat and parallel with each other so that the electric fields between plates P and Q and plates P' and Q' are substantially uniform thereacross, that is, in the direction perpendicular to the common horizontal plane of beams B B , B G and B B . Thus, as the beams are vertically deflected by the vertical deflection field of yoke D so as to be directed at the upper or lower portions of screen S and such vertical deflection field vertically displaces the beams within convergence deflecting device F, the deflecting effects on beams B B and B R of the fields between plates P and Q and plates P' and Q', respectively, are substantially unchanged. However, as shown on FIG. 2, when the horizontal deflection field of yoke D deflects the beams toward the left side of the screen as seen from the viewer's side of the latter, that is, downwardly as viewed on FIG. 2, the side beams B B and B R travel distances through such horizontal deflection field that are respectively greater than and smaller than the distance that the central beam B G travels through the horizontal deflection field. Conversely, when the horizontal deflection field of yoke D deflects the beams toward the right side of the screen as viewed from the viewer's side, the distances traveled by the beams B B and B R through the horizontal deflection field are respectively smaller than and greater than the distance that the central beam B G travels through such field. By reason of the foregoing differences between the distances that the beams travel through the horizontal deflection field when deflected by the latter toward one side or the other of the screen S, the raster of beam B B and the raster of beam B R would be displaced toward the left and toward the right, respectively, from the raster of the beam B G , as seen from the viewer's side of the screen. If the horizontal deflection field of yoke D is given a non-uniform flux density thereacross, for example, a greater flux density at the sides than at the middle of the field, the described relative displacements of the rasters can be compensated for so long as the common plane of the beams is substantially horizontal, that is, so long as the beams are directed at the screen substantially midway between the top and bottom of the screen. However, when the horizontal deflection field of yoke D directs the beams toward one side or the other of the screen at a time when the vertical deflection field of yoke D deflects the beams vertically so that the common plane of the beams is substantially inclined from the horizontal to direct the beams toward a corner of the screen, the differences between the distances traveled by the beams through the horizontal deflection field are further increased, as compared with the differences in the distances traveled through the field when the common plane of the beams is horizontal, so that even the mentioned non-uniform flux density across the horizontal deflection field of yoke D would be ineffective to avoid distortions of the rasters of beams B B and B R relative to the raster of beam B G .
Assuming that the raster of central beam B G has a rectangular shape, as indicated at L G on FIG. 3, the raster L B of beam B B , as seen from the viewer's side of the screen, is distorted in the sense that its sides are convex toward the right, while the raster L R of beam B R is oppositely distorted, that is, its sides are convex toward the left.

Since convergence deflecting device F is disposed adjacent the main deflecting yoke D (FIG. 1), it will be apparent that the vertical deflection field of yoke D will extend into device F, and thereby influence the vertical positions of the beams B B , B G and B R in passing through device F. Thus, when the vertical and horizontal deflection fields of yoke D are effective to direct the beams toward a corner of the screen, the vertical deflection field of yoke D will vertically displace beams B R , B G and B B either upwardly or downwardly from plane 21 within convergence deflection device F. By reason of the increased distance betweeen plates P and Q and plates P' and Q' at such displaced positions of beams B B and B R , the parts of the electric fields then acting on such beams will be of relatively reduced intensity thereby to similarly reduce the convergent deflections imparted to beams B B and B R . Thus, for example, when the beams are horizontally and vertically deflected by yoke D so as to be directed at the upper or lower left-hand corner of the screen, as seen from the viewer's side thereof, the left-ward deflection of beam B B by the field between plates P and Q will be reduced and the right-ward deflection of beam B R by the field between plates P' and Q' will be similarly reduced, whereby to bring the left-hand sides of the rasters L B and L R , as seen on FIG. 3, into agreement with the left-hand side of the raster L G . Similarly, when the beams are horizontally and vertically deflected by yoke D so as to be directed at the upper or lower right-hand corner of the screen as viewed on FIG. 3, the left-ward and right-ward deflections of beams B B and B R , respectively, by the fields between plates P and Q and plates P' and Q' will be reduced whereby to bring the right-hand sides of rasters L B and L R into agreement with the right-hand side of raster L G . Thus, distortions of the rasters L B and L R relative to the raster L G can be effectively avoided by suitably selecting the position of convergence deflecting device F relative to yoke D and the shapes of plates Q and Q'.
As shown on FIGS. 5 and 7, the effect described above may also be achieved by providing flat or planar outer plates Q and Q' and outwardly convex inner plates P and P' (FIG. 5), or by providing outer plates Q and Q' that are inwardly convex and inner plates P and P' that are outwardly convex (FIG. 7). In each of these modifictions, the distances between plates P and Q and between P' and Q' vary from a minimum at the horizontal plane passing through the tube axis to maximums at the upper and lower portions of the plates to conversely vary the strengths of the electrical fields between plates P and Q and plates P' and Q'. Since plates P and P' are at equal potential there is no electric field established therebetween, and thus the varying distance between plates P and P' in FIGS. 5 and 7 does not affect beam B G as the latter is vertically deflected.

Of course, in the foregoing, it has been assumed that the distortions of rasters L B and L R relative to raster L G that are to be corrected are those shown on FIG. 3. However, a situation may arise, for example, by reason of a particular configuration of the horizontal deflection field produced by yoke D, in which the raster of beam B B has the shape indicated at L R on FIG. 3 while the raster of beam B R has the shape indicated at L R . In the latter case, the plates P and Q and the plates P' and Q' are shaped so that the distances therebetween are maximum at the horizontal plane containing the axis of the tube and decrease progressively therefrom in the vertical direction, that is, in the direction perpendicular to the common plane in which the beams originate. In achieving such variations in the distances between the plates, plates P and P' may be flat or planar and plates Q and Q' may be outwardly convex (FIG. 6), or plates P and P' may be inwardly convex and plates Q and Q' may be outwardly convex (FIG. 8).
Further, in each of the above described embodiments of this invention, the convergence deflection device F consists of only a single pair of plates P and Q or P' and Q' acting on each of the beams B B and B R to deflect the respective beam in the direction for convergence with the central beam B G . However, the invention can also be applied to color picture tubes, for example, as disclosed in the copending U.S. application Ser. No. 718,738, filed Apr. 4, 1968, and having a common assignee herewith, in which the beams following paths diverging from the tube axis upon emerging from the focussing lens are each successively acted upon by two pairs of deflecting plates, with the first pair of plates establishing an electric field therebetween by which the respective beam is further diverged from the tube axis and the second pair of plates establishing a field therebetween by which the beam is deflected in the direction for converging with the other beams. The foregoing arrangement makes it possible to increase the angles of incidence of the side beams B B and B R at the beam selecting apertured grill or mask G P , whereby to permit a decrease in the distance of the latter from screen S for facilitating the accurate locating and mounting of the grill or mask G P relative to the screen S. Where each of the side beams B B and B R is successively acted upon by two pairs of deflecting plates, as aforesaid, one or the other of such pairs of plates, and preferably the pair of plates closest to the location of the main deflection yoke, is provided with a distance between the plates that varies in the direction perpendicular to the common plane in which the beams originate so as to avoid distortion of the raster of the respective beam in accordance with this invention.
Having described various embodiments of this invention, it is to be understood that the invention is not limited to those precise embodiments, and that various changes and modifications may be effected therein by one skilled in the art without departing from the scope or spirit of the invention.
SONY TRINTRON DYNAMIC CONVERGENCE CIRCUIT

1. Field of the Invention
This invention relates generally to dynamic convergence circuits for plural electron beam display apparatus such as a color television receiver, and is more particularly directed to an improved dynamic convergence circuit of reduced complexity provided together with a horizontal deflection circuit.
2. Description of the Prior Art
In most color cathode ray tubes employed in color television receivers for commercial use at present, plural electron beams, for example, three electron beams are utilized. In such a color cathode ray tube, respective electron beams emitted from its electron gun are deflected for beam scanning by a deflection yoke provided around the neck portion of the tube. An aperture mask is provided in the tube in front of the color phosphor screen for determining the impinging positions of the electron beams on the color phosphor screen. The respective electron beams impinge on the positions corresponding to red, green and blue color phosphors in response to their incident angles to the aperture of the mask. Thus, the electron beams scan the color phosphor screen under the control of the deflection yoke to form separate images of different primary colors and hence to display a full color image on the color phosphor screen. In order to form a correct full color image on the screen it is required that the plural primary color images should be formed on the screen with a superposition relation over all the points on the screen. To this end, arriving positions of the plural electron beams on the screen are required to be in superposition. This superposition is achieved by not only a static correction means but also by a dynamic correction means generally called a convergence means.
The static convergence means is provided for converging the plural electron beams at the center of the screen when the deflection yoke is inoperative. However, when the deflection yoke is operative the plural electron beams are subjected to different degrees of deflection by the deflection yoke because the electron beams pass through the deflection field established by the deflection yoke at different portions thereof. As a result, the electron beams may mis-converge as they move from the center of the screen to its periphery.
To correct or compensate for the misconvergence of the electron beams, an additional dynamic convergence coil is provided as a dynamic convergence means in addition to the deflection yoke for beam scanning. The additional dynamic convergence coil is supplied with a current in accordance with a beam position to correct or compensate for the beam deflection state. To this end, a waveform of a generally parabolic shape with horizontal and/or vertical scanning period repetition is used as the current supplied to the dynamic convergence coil. Thus, the plural electron beams are deflected by the beam deflection field of the dynamic convergence coil to be converged correctly at all of points on the screen.
In the prior art, it has been proposed that the current having a waveform of parabolic shape with a repetition which is the same as the horizontal scanning period and which is fed to the dynamic deflection coil be formed by a circuit in which a horizontal pulse appearing at an output transformer of the horizontal deflection circuit is integrated by a series connection of a coil and a capacitor. The voltage of sawtooth waveform obtained across the capacitor is then fed to the dynamic convergence coil so as to apply the current of parabolic shape waveform. Such a circuit, however, is required to provide means for deriving the horizontal pulse from the horizontal output transformer, means for integrating the thus obtained horizontal pulse, means for adjusting the integrated pulse in amplitude and so on, separately, so that the circuit becomes complicated in construction.
SUMMARY OF THE INVENTION
The above and other disadvantages are overcome by the present invention of a dynamic convergence circuit for a plural beam cathode ray tube comprising a horizontal deflection output device provided for supplying a horizontal beam deflection current of generally sawtoothed waveform to a deflection coil for the horizontal scanning of beams, inductance means connected to the output of the output device, with a horizontal pulse voltage being produced at the inductance means, convergence coil means connected in series with the inductance means, and impedance means connected to the inductance means and in parallel with the convergence coil device, the impedance means being operative to integrate the horizontal pulse voltage in cooperation with the inductance means to supply a sawtoothed waveform voltage across the convergence coil and, by means of the sawtoothed waveform voltage, to have a current of generally parabolic waveform flow through the convergence coil device, thereby to maintain the proper convergence of the plural beams in response to the beam scanning.
In one preferred embodiment the output device comprises a transistor performing the switching operation in response to a horizontal driving signal supplied thereto. The impedance means comprises a series connection of a capacitor and a resistor. Furthermore in some embodiments the resistor comprises a variable resistor for varying the tilt of the sawtoothed waveform voltage supplied to the convergence coil device.
Accordingly, it is an object of this invention to provide an improved dynamic convergence circuit of reduced complexity for a plural beam color cathode ray tube.
Another object of this invention is to provide an improved dynamic convergence circuit which is simplified by being designed together with a horizontal deflection circuit.
The foregoing and other objectives, features, and advantages of the invention will be more readily understood upon consideration of the following detailed description of certain preferred embodiments of the invention, taken in conjunction with the accompanying drawings.
BRIEF DESCRIPTION OF THE DRAWINGS
FIG. 1 is a schematic circuit diagram showing one embodiment of a dynamic convergence circuit according to the present invention;
FIGS. 2 and 4 show waveforms used for explanation of the present invention; and
FIGS. 3, 5, 6 and 7 are schematic circuit diagrams respectively showing other embodiments of dynamic convergence circuits according to the present invention.
DESCRIPTION OF CERTAIN PREFERRED EMBODIMENTS

The dynamic convergence coil 13 is connected in series between the power source terminal 4 and the end of the horizontal output winding 3 remote from the transistor 2. A series circuit of a capacitor 11 and a variable resistor 12 is connected in parallel with the dynamic convergence coil 13. A variable resistor 14 for correction of the amplitude of a parabolic waveform current is also connected in parallel with the dynamic convergence coil 13. In this case, the capacitance of the capacitor 11 may be selected, for example, as 0.022 micro-Farads (μF), the resistance value of the variable resistor 12 may be selected within a range of from 220 ohms (Ω ) to 500 ohms (Ω ) and the inductance value of the dynamic convergence coil 13 may be selected to be 14 milli-Henries (mH) to resonate with a signal with a frequency of 15.75 KHz.
With the circuit constructed as above, a horizontal pulse obtained at the horizontal output winding 3 is substantially integrated by the horizontal output winding 3 and the capacitor 11 and then a sawtooth waveform current flows from the power source terminal 4 to the circuit ground through the capacitor 11, the variable resistor 12 and the horizontal output winding 3 to impress a sawtooth waveform voltage across the dynamic convergence coil 13. This results in a parabolic shape waveform current i c with the horizontal scanning period repetition, which is shown in FIG. 2, flowing through dynamic convergence coil 13 to achieve the horizontal dynamic convergence compensation.
As mentioned above, with the circuit shown in FIG. 1 the parabolic shape waveform current flows through the dynamic convergence coil 13 without the provision of a separately provided coil for integration, so that the circuit construction is simplified.
Further, according to this invention if the resistance value of the variable resistor 12 is adjusted the phase or tilt of the parabolic shape waveform current i c can be controlled as shown in FIG. 2 by a dotted line. If the resistance value of the variable resistor 14 is adjusted the amplitude of the parabolic shape waveform current i c for the dynamic convergence compensation is controlled. In this case, it should be noted that, it is possible to adjust the amplitude and the tilt of the parabolic shape waveform current independently, which is an advantage of this invention.

In the embodiment of FIG. 3, the collector electrode of the transistor 2 for the horizontal output circuit is connected directly to the power source terminal 4 and the parallel circuit of the damper diode 5 and capacitor 6 is connected between the collector and emitter electrodes of the transistor 2. The series circuit of the horizontal deflection coil 7 and capacitor 8 for deflection current wave compensation is also connected between the emitter and collector electrodes of the transistor 2. The emitter electrode of the transistor 2 is grounded through the series circuit of the horizontal output winding 3 and dynamic convergence coil 13. The connection point between the winding 3 and the coil 13 is grounded through the series circuit of the capacitor 11 and variable resistor 12 and also through the variable resistor 14. Thus, a parabolic shape waveform current flows through the horizontal dynamic convergence coil 13 in the same manner as in FIG. 1. The connection point between the horizontal output winding 3 and the dynamic convergence coil 13 is further connected to a coil 15, which servies as a horizontal frequency stopper, such that a parabolic shape waveform current with horizontal scanning period repetition is obtained at the coil 15 and is blocked from being applied to a point a.
In FIG. 3 reference numeral 16 indicates a vertical driving circuit whose output terminal is connected to base electrode of an NPN-type transistor 17. The collector electrode of the transistor 17 is connected through the base-collector junction of a transistor 18 to the base electrode of a transistor 21, which forms a SEPP-type output stage together with a transistor 20. The collector electrode of transistor 17 is also connected to the cathode of a diode 19 whose anode is connected to the base electrode of the transistor 20. The connection point between the emitter electrode of the transistor 20 and the collector electrode of the transistor 21 is connected to the emitter electrode of transistor 18 and through a series circuit of a vertical deflection coil 22, capacitors 23 and 24 to the emitter electrode of the transistor 17. A sawtooth waveform current flows through the vertical deflection coil 22 so that a parabolic shape waveform current with a vertical scanning period repetition is delivered to the connection point a between the two capacitors 23 and 24.
With the circuit shown in FIG. 3 a current i' c , in which the parabolic shape waveform current with the vertical scanning period repetition for vertical dynamic convergence compensation is superimposed on the parabolic shape waveform current with the horizontal scanning period repetition for horizontal dynamic convergence compensation is obtained as shown in FIG. 4 to perform both vertical and horizontal dynamic convergence compensation.

FIGS. 6 and 7, respectively show further embodiments of this invention in which reference numerals similar to those of the foregoing figures indicate similar elements. In these embodiments a pin-cushion compensation signal, which is applied to the horizontal deflection circuit for compensation of pin-cushion distortion of the raster, is used for vertical dynamic convergence.
In the embodiment of FIG. 6, the connection point between the horizontal output winding 3 and the dynamic convergence coil 13 is grounded through the series circuit of the coil 15 serving as a horizontal frequency stopper and a capacitor 27. The connection point between the coil 15 and the capacitor 27 is connected to the collector electrode of an NPN-type transistor 28 whose emitter electrode is grounded. An input terminal 28a for a pin-cushion compensation signal is connected to the base electrode of the transistor 28. The input terminal 28a may be supplied with a parabolic shape waveform current with a vertical scanning period repetition for pin-cushion compensation. The dynamic convergence coil 13 is grounded through a capacitor 29 and the connection point between them is grounded through a series circuit of a variable resistor 30 and a capacitor 31 for amplitude compensation of the parabolic shape waveform current with the vertical scanning period repetition.
In the embodiment constructed as above, the parabolic shape waveform current with the vertical scanning period repetition for pin-cushion compensation is applied to the base electrode of the transistor 28, which is connected in parallel to the dynamic convergence coil 13, through the input terminal 28a, so that a first parabolic shape waveform current with a vertical scanning period repetition such as, for example, shown in FIG. 4, flows through the dynamic convergence coil 13 where a second parabolic shape waveform current, with the horizontal scanning period, is superimposed on the first parabolic shape waveform current. Accordingly, it should be apparent that the vertical and horizontal convergence compensations are achieved by this embodiment as in the embodiments shown in FIGS. 3 and 5.
Since the parabolic shape waveform current with the vertical scanning period repetition for pin-cushion compensation is used in the embodiment of FIG. 6 as mentioned above, a separate circuit for producing the parabolic shape waveform current can be dispensed with.

The terms and expressions which have been employed here are used as terms of description and not of limitation, and there is no intention in the use of such terms and expressions, of excluding equivalents of the features shown and described, or portions thereof, it being recognized that various modifications are possible within the scope of the invention claimed.
SONY TRINTRON Convergence means for color cathode ray tube
The beam forming means and static convergence correcting means in a color cathode ray tube are arranged to provide for proper convergence of the beams at regions remote from the center of the screen and closer to the corners. The resulting misconvergence at the center of the screen is then corrected by dynamic convergence correcting means which produces less beam distortion then if it had to correct misconvergence at the corners.

1. A convergence correction system for a color cathode ray tube comprising a fluorescent screen and means to produce three electron beams, said system comprising a deflection yoke to deflect said beams at line repetition rate in a raster pattern repeated at field repetition rate on said screen, and system further comprising:
static convergence correction means to cause said beams to be substantially fully converged to common points at certain outer regions of said screen and to be only partially converged at the central region of said screen; and
magnetic, dynamic, convergence correction means comprising a coil and current-generating means connected thereto to supply to said coil a magnetic convergence correction current that has a repetitive waveform with a maximum magnitude when said beams strike the central region of said screen and a lesser magnitude when said beams are deflected to strike said certain outer regions of said screen to cause said coil to produce a magnetic convergence field of greatest intensity when said beams strike said central region, whereby said beams are substantially fully converged at said central region.
2. The convergence correction system of claim 1 in which said static convergence correction means comprises:
electrostatic deflection means within said tube and positioned therein between said means to produce said beams and the location of said deflection means; and
substantially constant voltage means connected to said electrostatic deflection means to apply thereto deflection voltages of magnitudes sufficient to cause said beams to converge to common points at the outer region of said raster pattern and less than sufficient to cause said beams to converge to a common point at the center of said raster pattern.
3. The convergence correction system of claim 1 in which said vurrent-generating means comprises means to generate a correction current in which said repetitive waveform comprises parabolic segments of substantially equal amplitude and the same repetition rate as said line repetition rate. 4. The convergence correction system of claim 3 in which said current-generating means generates a current having second substantially parabolic waveform segments at a repetition rate equal to the field repetition rate of said raster, said first-named correction current and said second current being connected additively to said magnetic dynamic convergence correction means and the additive value of said first-named current and said second current being substantially equal to zero when said beams are deflected substantially to the corners of said raster. 5. A convergence correction system for a color cathode ray tube comprising a fluorescent screen and means to produce three electron beams directed generally toward said screen, said system comprising a magnetic deflection yoke located on said tube in a region between said means to produce said beams and said screen to deflect said beams in a raster pattern on said screen in response to deflection currents applied to said deflection yoke, said deflection yoke producing an electron lens with a strength that is a function of the deflection current and is substantially zero at the center of said raster, said system further comprising:
electrostatic static convergence deflection plates in said tube in a region between said means to produce said beams and said region on which said deflection yoke is located, said deflection plates having a fixed voltage applied thereto to produce a static convergence field to converge said beams in combination with the focusing effect of said yoke when said beams are deflected by said yoke to the outermost parts of said raster;
magnetic dynamic convergence means defining a lens field and comprising a coil; and
means to generate a convergence correction current to be applied to said coil to cause said magnetic dynamic convergence means to produce a magnetic electron lens having different horizontal and vertical strengths, the magnitudes of said strengths being a function of the magnitude of said current and varying from substantially zero when said beams are deflected to the outermost parts of said raster to a maximum when said beams are not deflected from the center of said raster, whereby said beams are converged at the center of said raster by the combined effects of said statis convergence field and said lens field of said magnetic dynamic convergence means when said deflection current in said yoke is substantially zero.
6. A convergence correction system for a color cathode ray tube comprising a fluorescent screen and means to produce three electron beams, sais system comprising a deflection yoke to produce a deflection field to deflect all of said beams simultaneously in a rectangular raster pattern comprising a plurality of substantially parallel lines generated on said screen at line repetition rate, said system further comprising:

static convergence means to produce, in cooperation with the deflection field of said yoke, a convergence field to cause said beams to be substantially fully converged to common points only when said beams are deflected to outer regions of said raster pattern;
magnetic dynamic convergence correction means comprising a coil and current generating means connected thereto to supply to said coul a convergence correction current comprising a parabolic waveform repetitive at said line repetition rate, said current having a maximum magnitude when said beams are directed to the central region of said screen and substantially zero magnitude when said beams are deflected to said outer regions of said raster pattern.
7. The method of correcting convergence of electron beams on a color cathode ray tube screen, said method comprising the steps of:
statically converging the beams near outer regions of the screen; and
imposing additional dynamic magnetic convergence fields on selective ones of said beams, said dynamic magnetic convergence fields having maximum intensity when the beams are in the central region of the screen to converge the beams in said central region.
8. The method of correcting convergence of a plurality of electron beams disposed in spaced relation substantially in a common plane and deflected along a series of lines defining a rectangular raster, said lines being substantially parallel to said plane and being the points of interception of said beams with a cathode ray tube screen, said method comprising:
statically deflecting said beams selectively parallel to said plane to cause all of said beams to converge at the corners of said raster; and
selectively imposing on said beams dynamic magnetic convergence fields having maximum intensity when the beams strike the central region of the raster, said dynamic convergence fields applying converging force to said beams in a direction parallel to said plane and substantially perpendicular to said beams.
9. The method of claim 8 in which said dynamic, magnetic, convergence fields have minimum intensity when beams are deflected to each end of each of said lines. 10. The method of claim 8 in which said dynamic magnetic convergence fields have minimum intensity only when said beams are deflected to the corners of said raster.
1. Field of the Invention
This invention relates to convergence correction apparatus for color cathode ray tubes and particularly to apparatus that includes static and dynamic convergence correcting devices, at least the latter of which is a magnetic correcting device.
2. Description of the Prior Art
It has been the practice heretofore to provide proper focusing and convergence of the electron beams of a color cathode ray tube at the center of the screen when the magnetic deflection fields are not present and therefore are not contributing to any distortion of the beam or to any misconvergence. However, as the beams are deflected away from the center of the screen and particularly at the most distant locations in the four corners of the screen, the beams are subjected to magnetic fields and in some cases to electrostatic fields that cause the beams to strike different locations instead of being converged to a small area and further cause the cross sections of the beams to be distorted. Both of these effects cause the quality of the image to be deteriorated at the corners of the picture.
In addition, the change of beam size due to distortion affects the current density. Steps taken to correct the misconvergence at the corners still may leave the current density uncorrected. Since the luminance of the different phosphors is relatively linear only up to a certain maximum amount and is then saturated, and the point of saturation is different for the different phosphors, the hue of the image will be incorrect at the corners due to the fact that one of the phosphors will start to saturate first.
OBJECTS AND SUMMARY OF THE INVENTION
It is one of the objects of this invention to provide a simpler and better convergence arrangement for a color cathode ray tube.
Another object is to provide more uniform color balance over the entire cathode ray tube screen.
A further object is to provide improved convergence of the beams of a multibeam color cathode ray tube without producing high distortion of the beams.
Further objects will become apparent from the following description including the drawings.
In accordance with this invention a multibeam color cathode ray tube, particularly a tube of the general type shown and described in U.S. Pat. No. Re 27,751, has a static convergence correction device, such as a set of electrostatic deflection plates with applied voltages of the magnitude to cause static convergence of the beams at the corners of the cathode ray tube. The result is misconvergence at the center. However, the misconvergence at the center is corrected by a dynamic correction device that causes the beams to converge at a time when the beams are not also being subjected to the magnetic deflection fields.
BRIEF DESCRIPTION OF THE DRAWINGS
FIG. 1 is a simplified cross sectional view of the electron gun region and part of the convergence and deflection coils of a color cathode ray tube.
FIG. 2 illustrates the relationship between the dynamic convergence apparatus and the electron beams in the device in FIG. 1 when operated according to the prior art.
FIGS. 3 and 4 illustrate two types of misconvergence of electron beams on a cathode ray tube screen in a tube of the type represented in FIG. 1.
FIG. 5 is a waveform of correction current applied to the dynamic correction device in FIG. 1 according to the prior art.
FIG. 6 is a waveform of a modified correction current to correct for the misconvergence shown in FIG. 4.
FIG. 7 illustrates the proper cross sectional shape of an electron beam in a tube of the type shown in FIG. 1.
FIG. 8 shows a typical distortion of the cross sectional shape of the beam in FIG. 7.
FIG. 9 shows a beam pattern similar to that in FIG. 3 but with static correction applied according to the present invention.
FIG. 10 shows a beam pattern corresponding to that in FIG. 4 but with proper static convergence according to the present invention.
FIG. 11 is a waveform of dynamic convergence correction current to effect convergence of the beams having the type of misconvergence shown in FIG. 9.
FIG. 12 is a waveform of the current applied to a dynamic convergence correction device according to the present invention to correct misconvergence of the type illustrated in FIG. 10.
FIG. 13 is a graph of luminance versus beam current for different phosphors .
DETAILED DESCRIPTION OF THE EMBODIMENTS

Beyond the electrode G 5 is an electrostatic convergence structure 1 comprising an inner pair of deflection plates 2 and 3 juxtaposed, respectively, with a pair of outer deflection plates 4 and 5. The plates 2 and 3 are electrically connected together to a voltage terminal E b and the plates 4 and 5 are electrically connected together to a terminal E c .
External to the tube in FIG. 1 are an electromagnetic convergence device 6 and part of a deflection yoke 7. The latter is arranged to deflect the electron beams, for the most part, after they have been subjected to convergence forces by the structure 1 and the structure 6.
The cathodes K R , K G and K B are preferably located in the same plane, which may be considered to be the plane of the drawing. The cathode K G is at the center at the axis of the tube and the other two cathodes are parallel to the cathode K G and equally spaced from it on opposite sides. The beams originally emitted from the cathodes are substantially parallel until they reach a lens identified as L S , formed generally by electrostatic fields in the region between the second grid G 2 and the anode, or third grid, G 3 . This lens is commonly called an auxiliary lens. The focal length of the auxiliary lens is such that it causes the three beams to intersect in the lens region L M approximately centrally located in the three-element lens formed by the electrodes G 3 -G 5 . As is now well known, this permits the three beams identified as R, G and B to be focused by nearly the same electrostatic field in the three-electrode lens so as to minimize distortion of the spots produced by the electron beams at the screen (not shown). After passing through the lens field L M and being focused thereby (an action which is not illustrated), the beams diverge along continuations of the lines by which they entered the lens field L M . The beam that will eventually strike green phosphor elements and is therefore identified by the reference character G, continues along the tube axis midway between the deflection plates 2 and 3. Since these plates are at the same voltage, the beam G is not substantially affected by the voltage on those plates. The beam B passes between the plates 2 and 4 and the beam R passes between the plates 3 and 5. Since these beams originate at points that are symmetrically displaced with respect to the beam G, and since the deflection plates of the structure 1 are also substantially symmetrically arranged, voltages applied to the terminals E b and E c deflect the beams B and R to intersect the beam G once more at the region of the screen of the cathode ray tube. In accordance with prior technology, if the screen has a 22 inch size, the voltage E b , which is

The dynamic convergence correction device 6 is located at substantially the same point on the Z-axis of the cathode ray tube as the static convergence correction device 1. As shown in FIG. 2, the dynamic convergence correction device 6 comprises two U-shaped magnetic cores 8 and 9. A coil 10 is wound on the core 8 and a similar core 11 is wound on the core 9. The coils are connected in series and are polarized so that the current of a given polarity following through them will produce magnetic fields in the cores 8 and 9 to result in north and south magnetic poles N and S as illustrated in FIG. 2. The direction of flux across the poles of the core 8 and across the poles of the core 9 is indicated by the reference character H 1 . Flux between the upper ends of the cores 8 and 9 and between the lower ends of these cores is denoted by reference character H 2 . The arrangement of the cores 8 and 9 is called a four-pole construction. The forces produced by magnetic fields of the cores 8 and 9 acting on electron beams B, G and R are indicated as the forces F 1 and F 2 . The force F 1 is produced by the flux H 1 and the force F 2 is produced by the flux H 2 . In the simplified representation in FIG. 2, these forces are illustrated as being substantially perpendicular to the respective magnetic fields that cause them, and the combined effect of these forces is to flatten the beams vertically and to spread them apart horizontally.

FIG. 4 shows another typical misconvergence pattern, and FIG. 6 shows the prior art convergence correction current applied to the coils 10 and 11 in FIG. 2. The misconvergence illustrated in FIG. 4 has both a horizontal and a vertical component and therefore the correction current waveform in FIG. 6 includes a parabolic horizontal component 1H and a parabolic vertical component 1V. The combined currents reach a maximum when the beams are deflected to the four corners of the screen S.
FIG. 7 represents the cross section of any one of the beams R, B or G when the current flowing through the dynamic convergence correction structure 6 in FIG. 2 is zero under the conditions of the prior art. That is, the correction current applied to the coils 10 and 11 in the structure 6 is zero and the beams are not deflected from the center of the screen S. However, when the beams are deflected toward the corners under the conditions of the prior art, which requires that the current through the coils 10 and 11 be at the peak values shown in FIG. 5 to correct the type of misconvergence in FIG. 3 or at the peak values shown in FIG. 6 to correct the type of misconvergence in FIG. 4, the beams are flattened as illustrated in FIG. 8. This is due to the force F 1 pulling the electron beams horizontally so as to spread them apart and the force F 2 compressing the beams vertically. This distortion of the beams adversely affects the quality of the television picture, mainly by adversely affecting the focus of the beams at the outer part of the screen.

In the case of a tube having both horizontal and vertical components of misconvergence, the reduction in the voltage difference between the inner deflection plates 2 and 3 and the outer deflection plates 4 and 5 eliminates misconvergence at the corners of the screen S as shown in FIG. 10. The correction current applied to the coils 10 and 11 from a source 12 must be of the type illustrated in FIG. 12. This current has the same waveform as the correction current shown in FIG. 6 but reaches zero value at the corners of the screen and a maximum negative value at the center of the middle line of the raster.
The current values required for dynamic convergence correction in accordance with this invention and as illustrated in FIGS. 11 and 12 do not necessarily have the same magnitudes as the current values in FIGS. 5 and 6. When the beams are in the exact center of the screen, they are not subjected to any deflection fields, which, when present, have not only a deflecting effect but a focusing effect that is a function of the deflection current and of the configuration of the deflection yoke 7. As a result dynamic convergence current may be less than in the case of the maximum dynamic convergence current in FIGS. 5 or 6. The magnetic field produced in the structure 6 in FIG. 2 is, in effect, a magnetic lens that has unequal horizontal and vertical effects on the beams. In the case of the present invention, this lens has maximum power due to maximum current when the beams are at the center of the screen and are thus not subjected to the combined lens and prism effects of the deflection yoke 7 shown in FIG. 1. As a result the beams B, G and R are not distorted in the manner shown in FIG. 8 or at least are distorted less than under the conditions of the prior art. This produces a picture of relatively uniform high resolution, not only at the outer part of the screen, but in the central region.
FIG. 13 shows the relationship between luminance and beam current for three typical phosphors used in color cathode ray tubes. For low beam currents the luminance of all three phosphors varies substantially linearly with the beam current. At a certain beam current the green phosphor begins to saturate so that additional current does not produce a corresponding additional green luminance. In the absence of any correcting circuits, if the beam current extends to a high enough value for all three phosphors so that the green phosphor is saturated, an image of a white object would take on a magenta hue due to an excess of red and blue light with respect to the green.
When t

By correcting the beam convergence according to the present invention, there is relatively little distortion of the beams at any part of the screen S and thus there is less tendency to have a high density that will adversely effect the color balance.
SONY DST EHT FBT TRANSFORMER Bobbin structure for high voltage transformers EHT Output.A coil bobbin for a fly-back transformer or the like having a bobbin proper. A plurality of partition members or flanges are formed on the bobbin proper with a slot between adjacent ones. At least first and second coil units are formed in the bobbin proper, each having several slots, formed between the flanges, and first and second high voltage coils are wound on the first and second coil units in opposite directions, respectively. A rectifying means is connected in series to the first and second coil units, and a cut-off portion or recess is provided on each of the partition members. In this case, a wire lead of the coil units passes from one slot to an adjacent slot through the cut-off portion which is formed as a delta groove, and one side of the delta groove is corresponded to the tangent direction to the winding direction.
1. A fly-back transformer comprising a coil bobbin comprising a plurality of parallel spaced discs with a first adjacent plurality of said disc formed with delta shaped slots having first edges which extend tangentially to a first winding direction and a first winding wound on said first adjacent plurality of said discs in said first winding direction, a second adjacent plurality of said discs formed with delta shaped slots having first edges which extend tangentially to a second winding direction opposite said first winding direction and a second winding wound on said second adjacent plurality of said discs in said second winding direction, a third adjacent plurality of said discs formed with delta shaped slots having first edges which extend tangentially to said first winding direction and a third winding woun

1. Field of the Invention
The present invention relates generally to a bobbin structure for high voltage transformers, and is directed more particularly to a bobbin structure for high voltage transformer suitable for automatically winding coils thereon.
2. Description of the Prior Art
In the art, when a wire lead is reversely wound on a bobbin separately at every winding block, a boss is provided at every winding block and the wire lead is wound on one block, then one end of the wire lead is tied to the boss where it will be cut off. The end of the wire lead is tied to another boss, and then the wire lead is wound in the opposite direction. Therefore, the prior art winding method requires complicated procedures and the winding of the wire lead cannot be rapidly done and also the winding can not be performed automatically. Further, the goods made by the prior art method are rather unsatisfactory and have a low yield.
OBJECTS AND SUMMARY OF THE INVENTION
Accordingly an object of the invention is to provide a coil bobbin for a fly-back transformer or the like by which a wire lead can be automatically wound on winding blocks of the coil bobbin even though the winding direction is different among the different winding blocks.
Another object of the invention is to provide a coil bobbin for a fly-back transformer or the like in which a bridge member and an inverse engaging device for transferring a wire lead from one wiring block to an adjacent wiring block of the coil bobbin and wiring the wire lead in opposite wiring directions between adjacent wiring blocks, and a guide member for positively guiding the wire lead are provided.
According to an aspect of the present invention, a coil bobbin for a fly-back transformer or the like is provided which comprises a plurality of partition members forming a plurality of slots, a first coil unit having several slots on which a first high voltage coil is wound in one winding direction, a second coil unit having several slots on which a second high voltage coil is wound in the other direction, a rectifying means connected in series to the first and second coil units, and a cut-off portion provided on each of the partition members, a wire lead passing from one slot to an adjacent slot through the cut-off portions, each of the cut-off portions being formed as a delta groove, and one side of the delta groove corresponding to a tangent to the winding direction.
The other objects, features and advantages of the present invention will become apparent from the following description taken in conjunction with the accompanying drawings through which the like reference numerals and letters designate the same elements and parts, respectively.
BRIEF DESCRIPTION OF THE DRAWINGS
FIG. 1 is a schematic diagram showing the construction of a fly-back transformer;
FIG. 2 is a connection diagram showing an example of the electrical connection of the fly-back transformer shown in FIG. 1;
FIG. 3 is a schematic diagram showing an example of a device for automatically winding a wire lead of the fly-back transformer on its bobbin;
FIG. 4 is a perspective view showing an example of the coil bobbin according to the present invention;
FIG. 5 is a plan view of FIG. 4;
FIGS. 6 and 7 are views used for explaining recesses or cut-off portions shown in FIGS. 4 and 5; and FIGS. 8A and 8B cross-sectional views showing an example of the inverse engaging means according to the present invention.
DESCRIPTION OF THE PREFERRED EMBODIMENT
When the high voltage winding of a fly-back transformer used in a high voltage generating circuit of a television receiver is divided into plural ones and then wound on a bobbin, the divided windings (divided coils) are connected in serie

When the winding is divided into, for example, three portions, such as divided coils La, Lb and Lc, they are wound on a bobbin proper 1 from, for example, left to right sequentially in this order as shown in FIG. 1. In this case, if the divided coils La and Lc are selected to have the same sense of turn and the middle coil Lb is selected to have the opposite sense of turn from the coils La and Lc, the distance between the terminal end of coil La and the start of coil Lb and the distance between the terminal end of coil Lb and the start of coil Lc can be got relatively long. Therefore, diodes Da and Db can be mounted by utilizing the space above the block on which the middle coil Lb is wound as shown in FIG. 1, so that it becomes useless to provide spaces for diodes between the divided coils La and Lb and between the divided coils Lb and Lc and hence the bobbin proper 1 can be made compact.
FIG. 2 is a connection diagram showing the connection of the above fly-back transformer. In FIG. 2, reference numeral 2 designates a primary winding (Primary coil) of the fly-back transformer, reference letter L designates its high voltage winding (secondary coil), including divided coils La, Lb and Lc, 3 an output terminal, and 4 a lead wire connected to the anode terminal of a cathode ray tube (not shown), respectively.
An example of the bobbin structure according to the invention, which is suitable to automatically wind coils, which are different in sense of turn in each winding block as shown in FIG. 1, on the bobbin, will be hereinafter described with reference to the drawings.
FIG. 3 is a diagram showing an automatic winding apparatus of a wire lead on a coil bobbin. If it is assumed that the wire lead is wound in the order of w

Turning to FIG. 4, an example 10 of the bobbin structure or coil bobbin according to the present invention will be described now. In this example, the winding blocks A, B and C for the divided coils La, Lb and Lc are respectively divided into plural slots or sections by plural partition members or flanges 11, and a cut-off portion or recess 12 is formed on each of the flanges 11 through which the wire lead in one section is transferred to the following winding section.
As shown in FIG. 6, each recess 12 is so formed that its one side extends in the direction substantially coincident with the tangent to the circle of the bobbin proper 1 and its direction is selected in response to the sense of turn of the winding or wire lead. In this case, the direction of recess 12 means the direction of the opening of recess 12, and the direction of recess 12 is selected opposite to the sense of turn of the wi

Now, recesses 12A, which are formed in the winding block A, will be now described by way of example. The positions of recesses 12A formed on an even flange 11Ae and an odd flange 11A 0 are different, for example, about 180° as shown in FIGS. 6A and 6B. Since the bobbin proper 1 is rotated in the counter-clockwise direction in the winding block A and hence the sense of turn of the wire lead is in the clockwise direction, the recess 12A is formed on the even flange 11Ae at the position shown in FIG. 6A. That is, the direction of recess 12A is inclined with respect to the rotating direction of bobbin proper 1 as shown in FIG. 6A. In this case, one side 13a of recess 12A is coincident with the tangent to the circle of bobbin proper 1, while the other side 13b of recess 12A is selected to have an oblique angle with respect to the side 13a so that the recess 12A has a predetermined opening angle.
The opening angle of recess 12A is important but the angle between the side 13a of recess 12A and the tangent to the circle of bobbin proper 1 is also important in the invention. When the wire lead is bridged or transferred from one section to the following section through the recess 12A, the wire lead in one section advances to the following section in contact with the side 13a of recess 12A since the bobbin proper 1 is rotated. In the invention, if the side 13a of recess 12A is selected to be extended in the direction coincident with the tangent to the circle of bobbin proper 1, the wire lead can smoothly advance from one section to the next section without being bent.
In the invention, since the middle divided coil Lb is wound opposite to the divided coil La, a recess 12B provided on each of flanges 11B of the winding block B is formed to have an opening opposite to that of recess 12A formed in the winding block A as shown in FIGS. 6C and 6D.
As shown in FIG. 5, terminal attaching recesses 14 are provided between the winding blocks A and B to which diodes are attached respectively. In the illustrated example of FIG. 5, a flange 15AB is formed between the flanges 11A 0 and 11B 0 of winding blocks A and B, and the recesses 14 are formed between the flanges 11A 0 and 15AB and between 15AB and 11B 0 at predetermined positions. Then, terminal plates 16, shown in FIG. 4, are inserted into the recesses 14 and then fixed there to, respectively. The terminal plates 16 are not shown in FIG. 5. Between the winding blocks B and C and between the blocks A and B, similar terminal attaching recesses 14 are formed, and terminal plates 16 are also inserted thereinto and then fixed thereto.
As described above, since the divided coil Lb is wound opposite to the divided coils La and Lc, it is necessary that the winding direction of the wire lead be changed when the wire lead goes from the block A to block B and also from the block B to block C, respectively.
Turning to FIG. 7, an example of the winding or wire lead guide means according to the present invention will be now described. In FIG. 7, there are mainly shown a bridge member for the wire lead and an inve

Next, an inverse engaging means 22 will be now described with reference to FIGS. 7 and 8. If the flange 11B 0 of FIG. 7 is viewed from the right side, the inverse engaging means 22 can be shown in FIG. 8A. In this case, the tip end of one side 13a of recess 12B 1 is formed as a projection which is extended outwards somewhat beyond the outer diameter of flange 11B 0 . The inverse engaging means 22 may take any configuration but it is necessary that when the rotating direction of the bobbin proper 1 is changed to the clockwise direction, the wire lead can be engaged with the recess 12B 1 or projection of one side 13a and then suitably transferred to the next station.
Another guide means 23 is provided on a bridge section X B at the side of winding block B in close relation to the inverse engaging means 22. The guide means 23 is formed as a guide surface which is a projected surface from the bottom surface of section X B and extended obliquely in the winding direction. This guide means or guide surface 23 is inclinded low into the means 22 and has an edge 23a which is continuously formed between the middle flange 15AB and the flange 11B 0 .
In this case, it is possible that the guide means 21 and guide surface 23 are formed to be the same in construction. That is, both the guide means 21 and 23 can be made of either the guide piece, which crosses the winding section or guide surface projected upwards from the bottom surface of the winding section. It is sufficient if the guide means 21 and 23 are formed to smoothly transfer the wire lead from one section to the next section under the bobbin proper 1 being rotated.
Although not shown, in connection with the middle flange 15BC between the winding blocks B and C, there are provided similar bridge means 20, guide means 21, inverse engaging means 22 and another guide means 23, respectively. In this case, since the winding direction of the wire lead is reversed, the forming directions of the means are reverse but their construction is substantially the same as that of the former means. Therefore, their detailed description will be omitted.
According to the bobbin structure of the invention with the construction set forth above, the wire lead, which is transferred from the block A to the section X A by the rotation of bobbin proper 1, is wound on the section X B from the section X A after being guided by the guide piece 21 to the recess 20 provided on the middle flange 15AB, and then transferred to the recess 22 provided on the flange 11B 0 guide surface 23, bridged once to the first section of winding block B through the recess 22 (refer to dotted lines b in FIG. 7). Then, if the rotating direction of the bobbin proper 1 is reversed, the wire lead is engaged with the bottom of recess 22 (refer to solid lines b in FIG. 7). Thus, if the above reverse rotation of bobbin proper 1 is maintained, the wire lead is wound on the block B in the direction reverse to that of block A. When the wire lead is transferred from the block B to block C, the same effect as that above is achieved. Therefore, according to the present invention, the wire lead can be automatically and continuously wound on the bobbin proper 1.
After the single wire lead is continuously wound on blocks A, B and C of bobbin proper 1 as set forth above, the wire lead is cut at the substantially center of each of its bridging portions. Then, the cut ends of the wire lead are connected through diodes Da, Db and Dc at the terminal plates 16, respectively by solder.
In the present invention, the projection piece, which has the diameter greater than that of the flange 11B, is provided in the bridge recess 12 to form the inverse engaging means 22 as described above, so that when the winding direction is changed, the wire lead engages with the inverse engaging means 22 without errors when reversing the winding direction of the wire lead.
If the diameter of the projection piece of means 22 is selected, for example, to be the same as that of the flange 11B, it will not be certain that the wire lead engages with the means 22 because it depends upon the extra length of the wire lead and hence errors in winding cannot be positively avoided.
Further, in this invention, the bridge means is provided on the flange positioned at the bridging portion of the bobbin which has a number of dividing blocks separated by flanges, and the inverse engaging means is provided and also the guide means is provided at the former winding section to cooperate with the inverse engaging means. Therefore, the wire lead can be positively fed to the bridge means, and the transfer of the wire lead to the following winding section can be carried out smoothly.
Furt

The above description is given for the case where the present invention is applied to the coil bobbin for the high voltage winding of a fly-back transformer, but it will be clear that the present invention can be applied to other coil bobbins which require divided windings thereon with the same effects.
It will be apparent that many modifications and variations could be effected by one skilled in the art without departing from the spirits or scope of the novel concepts of the present invention, so that the spirits or scope of the invention should be determined by the appended claims only.
SONY CHASSIS AE4 (AE-4) FAULT / REPAIR LIST:
AE4 SONY KV25C3D
AE4 SONY KV25K1D
AE4 SONY KV28WS4D
AE4 SONY KV28WX2D
AE4 SONY KV29C3D
AE4 SONY KV32WS4D
AE4 SONY KV32WS4U
AE4 SONY KV32WX2D
AE4 SONY KV32WX4U
AE4 Sony KV25C3A
AE4 Sony KV25C3D
AE4 SONY KV25C3D
AE4 Sony KV25C3E
AE4 Sony KV25K1D
AE4 Sony KV25K1K
AE4 SONY KV25K1K
AE4 Sony KV25X3D
AE4 SONY KV25X3D
AE4 Sony KV28WF3D
AE4 Sony KV28WS4D
AE4 SONY KV28WS4K
AE4 Sony KV28WX10D
AE4 SONY KV28WX10D
AE4 Sony KV28WX2D
AE4 SONY KV28WX2D
AE4 Sony KV29C3D
AE4 Sony KV29C3K
AE4 SONY KV29C3K
AE4 SONY KV29K1D
AE4 Sony KV32WS4K
AE4 SONY KV32WS4K
AE4 SONY KV32WX10D
AE4 Sony KV32WX2
AE4 Sony KV32WX2D
AE4 Sony KV32WX2D
AE4 SONY KV32WX2K
AE-4 SONY KV-29C3
REFERENCES LIST:
A. Semiconductor Devices and Physics
1. J. Baliga and D. Y. Chen (Eds.), Power Transistors: Device Design and Applications, IEEE
Press, New York, 1984.
2. J. Biliga, Modern Power Devices, John Wiley, New York, 1987.
3. Blicher, Thyristor Physics, Springer-Verlag New York Inc.,1976.
4. K. Ghandhi, Semiconductor Power Devices Physics of Operation and Fabrication Technology,
John Wiley & Sons, Inc.,New York, 1977.
5. G. Hoft, Semiconductor Power Electronics, Van Nostrand Reinhold Company Inc.,1986.
(ISBN: 0-442-22543-1)
6. P .
L. Hower, Power semiconductor devices: an overview, IEEE Proc., Wvol. 76, no. 4, pp.
335-342, April 1988.
7. C. Lee and D. Y. Chen (Ed.), Power Devices and Their Applications, Virginia Power
Electronics Center, 1990.
8. Ohmi, Power static induction transistor technology," Technical Digest, IEEE Electron Devices
International Meeting, Washington, D.C., pp. 84-87, 1979.
9. Shockley, A unipolar field-effect transistor ,"
Proc. IRE, vol. 40, pp. 1365-1376, Nov. 1952.
10. Shockley, How we invented the transistor," New Scientist, vol. 689, Dec. 21, 1972.
11. Shockley, The path to the conception of the junction transistor," IEEE Trans. Electron Devices
23, vol. 597, 1976.
12. G. Streetman, Solid State Electronic Devices, Prentice-Hall, Inc., 1980.
13. M. SZE, Semiconductor Devices: Physics and Technology, Bell Telephone Lab., Inc., 1985.
14. Teszner and R. Giqual, Gridistor - a new field-effect device," Proc. IEEE, vol. 52, pp. 1502-
1513, 1964.
15. M. Warner and B. L. Grung, Transistors: Fundamentals for the Integrated-Circuit Engineer
,
1983.
16. Wood, Fundamentals and Applications of Gate Turn-off Thyristors, Electric Power Research
Institute, Palo Alto, 1988.
17. S. Yang, Fundamental of Semiconductor Devices, McGraw-Hill Book Company, 1978.
18. Zuleeg, Multi-Channel field-effect transistor, theory and experiment," Solid-State Electronics,
vol. 10, pp. 559-576, 1967.
B. Power Electronics
19. D. Bedford and R. G. Hoft, Principles of Inverter Circuits, 1985 Reprint Edition, Robert E.
Krieger Publishing Company, Malabar, Florida, 1964.
20. M. Bird and K. G. King, An Introduction to Power Electronics,1983. (ISBN: 0-471-10430-
2)
21. B. K. Bose, Adjustable Speed A C Drive Systems, IEEE Press, New York, 1982.
22. B. K. Bose, "Power electronics - an emerging technology", IEEE Trans. on Ind. Electron., vol.
36, no. 3, pp. 404-412, Aug. 1989.
23. B. K. Bose, Microcomputer Control of Power Electronics and Drives, IEEE Press, New
York, 1987.
24. B. K. Bose., Modern Power Electronics, Evolution, Technology and Applications, IEEE
Press, New York, 1991.
25. B. K. Bose,"Power electronics - an emerging technology," IEEE Trans. on Ind. Electron., vol.
36, no. 3, pp. 403-412, 1989.
26. B. K. Bose, Power Electronics and A C Drives, Prentice Hall, Englewood Cliffs, 1986.
27. B. K. Bose, Power Electronics and A C Drives, Prentice-Hall, New Jersey, 1987.
(TK7881.15.B67).
28. B. K. Bose, "Power electronics and motion control technology," IEEE, pp. 1-10, 1992.
29. B. K. Bose, "Technology trends in microcomputer control of electrical machines," IEEE
Trans. on Ind. Electron., vol. 35, no. 1, pp. 160-177, Feb. 1988.
30. A. Coekin, High-Speed Pulse Techniques, Pergamon, 1975. (TK7835.C56 1975).
31. Csaki, I. Hermann, I. Ipsits, A. Karpati, and P .
Magyar, Power Electronics Akademiai Kiado,
Budapest, 1979. (ISBN 963-05-1671-3).
32. B. Dewan and A. Straughen, Power Semiconductor Circuits, John Wiley & Sons, Inc., 1975.
33. K. Dubey, Power Semiconductor Controlled Drives, Prentice Hall, Englewood Cliffs, 1985.
34. Hans-Peter Hempel, Power Semiconductor Handbook, SEMIKRON, 1980. (ISBN 3-
9800346-1-5).
35. R. G. Hoft, Semiconductor Power Electronics, Van Nostrand, New York, 1986.
(TK7871.85.H65).
36. L. Kusic, Computer-Aided Power Systems Analysis, Prentice-Hall, 1986. (TK1005.K87
1986).
37. W. Lander ,
Power Electronics, McGraw-Hill, 1981. (ISBN: 0-07-084123-3).
38. M. Miller, Is power electronics a national priority ?, Power Conversion & Intelligent
Motion Control, March 1987.
39. Mohan, T. M. Undeeland, and P .
Robbins, Power Electronics, John Wiley, New York, 1989.
40. M. D. Murphy and F. G. Turnbull, Power Electronic Control of A C Motors, Pergamon, New
York, 1988.
41. E. Newell and J. W. Motto, Introduction to Solid State Power Electronics, Youngwood:
Westinghouse Electric Corporation, 1977.
42. S. Oxner, Power FETs and Their Applications, Prentice-Hall Inc., 1982.
43. Pearman, Power Electronics: Solid State Motor Control, Reston Publishing Company, Inc.,
1980.
44. Pearman, Solid State Industrial Electronics, Reston Publishing Company, Inc., 1984. (ISBN:
0-8359-7041-8) (TK7881.P43).
45. Rajagopalan, Computer Aided Analysis of Power Electronic Systems, Marcel Dekker, New
York, 1987.
46. H. Rashid, Power Electronics, Prentice Hall, Englewood Cliffs, 1988.
47. H. Seidman, H. Mahrous, and T. G. Hicks, Handbook of Electric Power Calculations, 1983.
(ISBN 0-07-056061-7).
48. P .
Severns and G. E. Bloom, Modern DC-to-DC Switchmode Power Converter Circuits,
Van Nostrand Reihold Company Inc..
49. E. Tarter ,
Principles of Solid State Power Conversion, Howard W. Sams, 1985.
50. W. Williams, Power Electronics, John Wiley, New York, 1987.
C. Power Supplies
D. Electronic51. Chryssis, High-Frequency Switching Power Supplies Theory and Design, McGraw-Hill,
1984. (ISBN 0-07-010949-4) (TK868.P6C47).
52. Gottlieb, Regulated Power Supplies, third edition, Howard W. Sams & Co., Inc., 1984.
53. Gottlieb, Power Supplies: Switching Regulators Inverters & Converters, 1984.
54. Griffith, Uninterruptible Power Supplies, Marcel Dekker, New York, 1989.
55. Hnatek, Design of Solid State Power Supplies, Van Nostrand, New York, 1981.
56. Lee (Ed.), High-Frequency Resonant, Quasi-Resonant, and Multi-Resonant Converters,
Virginia Power Electronics Center, 1989.
57. Lee (Ed.), Modeling, Analysis, and Design of PW M Converters, Virginia Power
Electronics Center, 1990.
58. Middlebrook and S. Cuk (Eds.), Advances in Switching Mode Power Conversion, vols. I &
II, TESL A Co., Pasadena, California 1983.
59. M OTOROL A, Switchmode Application Manual, Motorola Inc., 1981.
60. M OTOROL A, Linear/Switchingmode Voltage Regulator Handbook: Theory and
Practice, 1981.
61. Pressman, Switching and Linear Power Supply, Power Converter Design, Hayden,
Rochelle Park, 1977.
62. Rensink, Switching Regulator Configurations and Circuit Realization, Ph.D Thesis by
Loman Rensink, California, 1979.
63. Severns and G. E. Bloom, Modern DC - to - DC Switch Mode Power Converter Circuits,
Van Nostrand, New York, 1985.
64. Sum, Switch Mode Power Conversion: Basic Theory and Design, Marcel Dekker, New
York, 1984.
65. Wood, Switching Power Converters, Van Nostrand, New York, 1981.
66. UNITRODE, Unitrode Switching Regulated Power Supply Design Seminar Manual,
Unitrode Corporation, 1985.
67. UNITRODE, Applications Handbook, Unitrode Corporation, 1985.
Equipment Thermal Design, Package Design
68. N. Ellison, Thermal Computations for Electronic Equipment, Van Nostrand Reinhold
Company, New York, 1984.
69. D. Kraus and Avram Bar-Cohen, Thermal Analysis and Control of Electronic Equipment,
Hemisphere Publishing Corporation, Washington, 1983. (ISBN 0-07-035416-2)
(TK7870.25.K73).
70. S. Matisoff, Handbook of Electronics Packaging Design and Engineering, Van Nostrand
Reinhold Company, 1982.
71. S. Steinberg, Cooling Techniques for Electronic Equipment, John Wiely & Sons, Inc., 1980.
(TK7870.25.S73).
E. Noise Reduction Techniques
72. W. Denny, Grounding for the Control of E MI.
73. J. Geogopoulos, Fiber Optics and Optical Isolators.
74. N. Ghose, E MP Environment and System Hardness Design.
75. C. Hart and E. W. Malone, Lighting and Lighting Protection.
76. Mardiguian, Electrostatic Discharge - Understand, Simulate and Fix ESD Problems.
77. Mardiguian, Interference Control in Computers and Microprocessor-Based Equipment.
78. Mardiguian, How to Control Electrical Noise.
79. Morrison, Grounding and Shielding Techniques in Instrumentation, second edition, John
Wiley & Sons, Inc., 1977.
80. Morrison, Instrumentation Fundamentals and Applications, John Wiley & Sons, Inc., 1984.
81. W. Ott, Noise Reduction Techniques in Electronic Systems, Wiley-Interscience Publication,
1976.
82. A. Smith, Coupling of External Electromagnetic Fields to Transmission Lines.
83. R. J. White and M. Mardiguian, E MI Control Methodolgy and Procedures.
84. R. J. White, E MI Control in the Design of Printed Circuit Boards and Backplanes, 248 Pages.
85. R. J. White, Shielding Design Methodlogy and Procedures.
86. R. J. White, Electrical Filter
.
87. R. J. White, Electromagnetic Shielding Materials and Performance.
88. E MC E XPO, 1986 Symposium Record, 416 Pages.
89. E MC Library :
vol. 1 Electrical Noise and E MI Specifications
vol. 2 E MI Test Methods and Procedures
vol. 3 E MI Control Methods and Techniques
vol. 4 E MI Test Instrumentation and Systems
vol. 5 E MI Prediction and Analysis Techniques
vol. 6 E MI Specifications, Standards, and Regulations
More References:
[1] Paynter, D.A., AN UNSYMMETRICAL SQUARE-WAVE
POWER OSCILLATOR, IRE transactions on Circuit Theory,
March 1956, pp. 64-65
[2] Dudley, William, UNSYMMETRICAL LOW VOLTAGE CON-
VERTER, 17th Power Sources Conference proceedings, 1963, pp.
155-158
[3] van Velthooven, C., PROPERTIES OF DC-TO-DC CONVERT-
ERS FOR SWITCHED-MODE POWER SUPPLIES, Philips
Application Information #472, 18 March 1975, pp. 8-10
[4] G. Wolf, MAINS ISOLATING SWITCH-MODE POWER SUP-
PLY, Philips Electronic Applications Bulleting, Vol. 32, No. 1,
February 1973
[5] La Duca and Massey, IMPROVED SINGLE-ENDED REGU-
LATED DC/DC CONVERTER CIRCUIT, IEEE Power Electronics
Specialists Conference (PESC) record, June 1975, pp. 177-187
[6] Heinicke, Harald, APPARATUS FOR CONVERTING D.C.
VOLTAGE, U.S. patent number 3,921,054, 18 November 1975
(1973 German filing)
[7] Hamata and Katou, DC-TO-DC CONVERTER, U.S. patent
number 3,935,526, 27 January 1976 (1972 Japanese filing)
[8] Peterson, W.A., A FREQUENCY-STABILIZED FREE-RUN-
NING DC-TO-DC CONVERTER CIRCUIT EMPLOYING
PULSE-WIDTH CONTROL REGULATION, IEEE PESC proceed-
ings, June 1976, pp. 200-205
[9] Vermolen, J.V., NON-SATURATING ASYMMETRIC DC/DC
CONVERTER, U.S. patent number 3,963,973, 15 June 1976 (1973
Dutch filing)
[10] Lilienstein and Miller, THE BIASED TRANSFORMER DC-
TO-DC CONVERTER, IEEE PESC proceedings, June 1976, pp.
190-199
[11] Carsten, B., HIGH POWER SMPS REQUIRE INTRINSIC
RELIABILITY, Power Conversion International (PCI) proceedings,
September 1981, pp. 118-133
[12] Kuwabara and Miyachika, A VERY WIDE INPUT RANGE
DC-DC CONVERTER, IEEE INTELEC proceedings, 1987, pp.
228-233
[13] Wittenbreder, Martin and Baggerly, A DUTY CYCLE
EXTENSION TECHNIQUE FOR SINGLE ENDED FORWARD
CONVERTERS, IEEE Applied Power Electronics Conference
(APEC) proceedings, 1992, pp. 51-57
More References:
Buhler H (1986) Sliding mode control (in French: Reglage ́
par mode de glissement). Presses
Polytechniques Romandes, Lausanne
Carpita M, Marchesoni M (1996) Experimental study of a power conditioning system using sliding
mode control. IEEE Trans Power Electron 11(5):731–742
Carrasco JM, Quero JM, Ridao FP, Perales MA, Franquelo LG (1997) Sliding mode control of a
DC/DC PWM converter with PFC implemented by neural networks. IEEE Trans Circuit Syst I
Fundam Theor Appl 44(8):743–749
DeBattista H, Mantz RJ, Christiansen CF (2000) Dynamical sliding mode power control of wind
driven induction generators. IEEE Trans Energy Convers 15(4):728–734
DeCarlo RA, Zak ̇
SH, Drakunov SV (2011) Variable structure, sliding mode controller design. In:
Levine WS (ed) The control handbook—control system advanced methods. CRC Press, Taylor
& Francis Group, Boca Raton, pp 50-1–50-22
Emelyanov SV (1967) Variable structure control systems. Nauka, Moscow (in Russian)
Filippov AF (1960) Differential equations with discontinuous right hand side. Am Math Soc
Transl 62:199–231
Guffon S (2000) Modelling and variable structure control for active power filters (in French:
“Modelisation ́
et commandes `
a structure variable de filtres actifs de puissance”). Ph.D. thesis,
Grenoble Institute of Technology, France
Guffon S, Toledo AS, Bacha S, Bornard G (1998) Indirect sliding mode control of a three-phase
active power filter. In: Proceedings of the 29th annual IEEE Power Electronics Specialists
Conference – PESC 1998. Kyushu Island, Japan, pp 1408–1414
Hung JY, Gao W, Hung JC (1993) Variable structure control: a survey. IEEE Trans Ind Electron
40(1):2–22
Itkis U (1976) Control systems of variable structure. Wiley, New York
Levant A (2007) Principles of 2-sliding mode design. Automatica 43(4):576–586
Levant A (2010) Chattering analysis. IEEE Trans Autom Control 55(6):1380–1389
Malesani L, Rossetto L, Spiazzi G, Tenti P (1995) Performance optimization of Cuk ́
converters by
sliding-mode control. IEEE Trans Power Electron 10(3):302–309
Malesani L, Rossetto L, Spiazzi G, Zuccato A (1996) An AC power supply with sliding mode
control. IEEE Ind Appl Mag 2(5):32–38
Martinez-Salamero L, Calvente J, Giral R, Poveda A, Fossas E (1998) Analysis of a bidirectional
coupled-inductor Cuk ́
converter operating in sliding mode. IEEE Trans Circuit Syst I Fundam
Theor Appl 45(4):355–363
Mattavelli P, Rossetto L, Spiazzi G (1997) Small-signal analysis of DC–DC converters with
sliding mode control. IEEE Trans Power Electron 12(1):96–102
ˇ
Sabanovic A (2011) Variable structure systems with sliding modes in motion control—a survey.
IEEE Trans Ind Inform 7(2):212–223
Sabanovic ˇ
A, Fridman L, Spurgeon S (2004) Variable structure systems: from principles to
implementation, IEE Control Engineering Series. The Institution of Engineering and Technol-
ogy, London
Sira-Ramırez ́ H (1987) Sliding motions in bilinear switched networks. IEEE Trans Circuit Syst 34
(8):919–933
Sira-Ramırez ́
H (1988) Sliding mode control on slow manifolds of DC to DC power converters. Int
J Control 47(5):1323–1340
Sira-Ramırez ́
H (1993) On the dynamical sliding mode control of nonlinear systems. Int J Control
57(5):1039–1061
Sira-Ramırez ́
H (2003) On the generalized PI sliding mode control of DC-to-DC power converters:
a tutorial. Int J Control 76(9/10):1018–1033
Sira-Ramırez ́
H, Silva-Ortigoza R (2006) Control design techniques in power electronics devices.
Springer, London
Slotine JJE, Sastry SS (1983) Tracking control of non-linear systems using sliding surface, with
application to robot manipulators. Int J Control 38(2):465–492
Spiazzi G, Mattavelli P, Rossetto L, Malesani L (1995) Application of sliding mode control to
switch-mode power supplies. J Circuit Syst Comput 5(3):337–354
Tan S-C, Lai YM, Cheung KHM, Tse C-K (2005) On the practical design of a sliding mode
voltage controlled buck converter. IEEE Trans Power Electron 20(2):425–437
Tan S-C, Lai Y-M, Tse C-K (2011) Sliding mode control of switching power converters:
techniques and implementation. CRC Press, Taylor & Francis Group, Boca Raton
Utkin VA (1972) Equations of sliding mode in discontinuous systems. Autom Remote Control 2
(2):211–219
Utkin VA (1977) Variable structure systems with sliding mode. IEEE Trans Autom Control 22
(2):212–222
Utkin V (1993) Sliding mode control design principles and applications to electric drives. IEEE
Trans Ind Electron 40(1):23–36
Venkataramanan R, Sabanovic ˇ
A, Cuk ́
S (1985) Sliding mode control of DC-to-DC converters. In:
Proceedings of IEEE Industrial Electronics Conference – IECON 1985. San Francisco,
California, USA, pp 251–258
Young KD, Utkin VI, Ozguner U (1999) A control engineer’s guide to sliding mode control. IEEE
Trans Control Syst Technol 7(3):328–342
References
[1] Nave, M. J.; “The Effect of Duty Cycle on SMPS Common Mode Emissions: Theory
and Experiment”, IEEE 1989 National Symposium on 23-25 May, 1989
[2] Cochrane, D.; Chen, D. Y.; Boroyevic, D.; “Passive Cancellation of Common-Mode
Noise in Power Electronic Circuits”, IEEE Transactions on Power Electronics,
Volume 18, Issue 3, May 2003
[3] Qu, S.; Chen, D. Y.; “Mixed-Mode EMI Noise and Its Implications to Filter Design in
Offline Switching Power Supplies”, Applied Power Electronics Conference and
Exposition, 2000, Fifteenth Annual IEEE, Volume 2, 6-10 Feb. 2000
[4] “Mounting Considerations For Power Semiconductors”, On Semiconductor Application
Note AN1040/D, May 2001-Rev. 3
[5] Mardiguian, M.; “Controlling Radiated Emissions by Design”, Chapman & Hall,
ISBN 0442009496
[6] Mardiguian, M.; “How To Control Electrical Noise”, 2nd Edition, 1983, Don White
Consultants, Inc., State Route #625, P.O. Box D, Gainesville, Virginia 22065, USA
[7] Hayt, H. W. JR.; “Engineering Electromagnetics”, Fourth Edition, McGraw-Hill Book
Company, ISBN 0070273952
[8] Collett, P. C. E.; “Investigations into Aspects Affecting the Design of Mains Filters for
Frequencies in the Range 10kHz-30MHz”, ERA Report No. 82-145R, 1983, ERA
Technology Ltd., Cleeve Road, Leatherhead, Surrey KT22 7SA, England
[9] “Capacitors for RFI Suppression of the AC Line: Basic Facts”, Fourth Edition,
Evox-Rifa Application Notes, Evox-Rifa Inc., 300 Tri-State International, Su. 375,
Lincolnshire, IL 60069, USA
[10] “Conducted Emission Performance of Ericsson DC/DC power modules:
Characterization and System Design”, Ericsson Design Note 009, April 2000, Ericsson
Microelectronics AB
[11] Ott, H. W.; “Noise Reduction Techniques in Electronic Systems”, Second Edition,
1987, John Wiley & Sons, ISBN 0471850683
[12] Ott, H. W.; “Understanding and Controlling Common-Mode Emissions in High-Power
Electronics”, Applied Power Electronics Conference and Exposition, 2002
[13] Basso, C.; “Conducted EMI Filter Design for the NCP1200”, On Semiconductor
Application Note AND8032/D
More listed References
[14] Armstrong, K.; Williams, T.; “EMC Testing”, Parts 1 through 6; Cherry Clough
Consultants and Elmac Services, UK
[15] Bergh, K.; “CISPR 22 Telecom Ports”, NEMKO Seminar, 2001
[16] “EMC of Monitors”, Philips Semiconductors Application Note AN 00038
[17] “EMI Testing Fundamentals”, Steward Technical Information
[18] Savino, S. E.; Suranyi, G. G.; “Application Guidelines for On-Board Power
Converters”, Tyco Electronics Application Note, June 1997
[19] “Input System Instability”, Synqor Application Note PQ-00-05-01 Rev.01-5/16/00
[20] Collett, P. C. E.; “Investigations into Aspects Affecting the Design of Mains Filters
for Frequencies in the Range 10kHz-30MHz”, ERA Report No. 82-145R, 1983,
ERA Technology Ltd., Cleeve Road, Leatherhead, Surrey KT22 7SA,
England
[21] “Capacitors for RFI Suppression of the AC Line: Basic Facts”, Fourth Edition,
Evox-Rifa Application Notes, Evox-Rifa Inc., 300 Tri-State International, Su. 375,
Lincolnshire, IL 60069, USA
[22] Snelling, E. C.; “Soft Ferrites, Properties and Applications”, Second Edition, ISBN
0408027606; Butterworths & Co.
[23] “Power Factor Corrector, Application Manual”, 1st Edition, October 1995;
SGS-Thomson Microelectronics
[24] “Data Handbook, Aluminum Electrolytic Capacitors”, PA01-A, 1993 N.A. Edition;
Philips Components
[25] “Understanding Aluminum Electrolytic Capacitors”, nd Edition, 1995; United
2Chemi-Con Inc.
[26] Micro Linear Corporation Data Book, 1995
[27] “Fair-Rite Soft Ferrites”, Databook, 13th Edition; Fair-Rite Products Corp. NY 12589
[28] “Magnetics Designer”, Supplementary Information, 1997; Intusoft
[29] “UC3842/3/4/5 Provides Low-cost Current-mode Control”, Application Note, U-100A;
Unitrode Integrated Circuits
[30] Billings, K. H.; “Switchmode Power Supply Handbook”, 1989, ISBN 0070053308;
McGraw-Hill Inc.
[31] Pressman, A. I.; “Switching Power Supply Design”, 1991, ISBN 0070508062,
McGraw Hill Inc.
[32] McLyman, W. T.; “Transformer and Inductor Design Handbook”, nd Edition, 1988,
2ISBN 0824778286; Marcel Dekker, Inc.
[33] Unitrode Power Supply Design Seminar, SEM-500, Unitrode Integrated Circuits
[34] “3C85 Handbook”, 1987, Ordering Code 9398 345 90011; Philips Electronic
Components and Materials
[35] Sum, K. K.; “Intuitive Magnetic Design”, Nov 15-16, 2000, Electronic Design
Workshops; Penton Media, Inc.
Others References list
[36] Bloom, G. E.; “DC-DC Switchmode Power Converters, Circuits and Converters”,
April 25, 2002, National Semiconductor Corporation Seminar Presentation; Bloom
Associates Inc., CA-94903
[37] Mulder, S. A.; “Application Note on the design of low profile high frequency
transformers, a new tool in SMPS design”, 1990, Ordering Code 9398 074 80011;
Philips Components Corporate Innovation Materials
[38] Ahmadi, H.; “Calculating Creepage and Clearance Early Avoids Design Problems
Later”, March/April 2001; Compliance Engineering Magazine
[39] Redl, R.; “Low-Cost Line-Harmonics Reduction”, 1995 Seminar in Bremen, Germany;
Power Quality Conference
[40] Carsten, B.; “Calculating Skin and Proximity Effect, Conductor Losses in Switchmode
Magnetics”, 1995, PCIM Conference
[41] “Magnetics® Ferrites”, Databook, 1999; Magnetics Inc., Division of Spang and
Company
[42] Lee, S.; “Thermal Management of Electronic Equipment”, 1996, PCIM Conference
[43] Middlebrook, R. D.; Cuk, S.; “Advances in Switched-Mode Power Conversion:
Volumes I, II, and III”, TESLAco, 10 Mauchly, Irvine, CA 92618
[44] Middlebrook, R. D.; “Topics in Multiple-loop Regulators and Current-mode
Programming”, IEEE 1985
[45] Erickson, R. W.; “Fundamentals of Power Electronics”, Springer, Second Edition,
ISBN 0792372700
[46] “Control Design Lecture Notes”, Center for Power Electronics Systems, June 2-6,
2003, Virginia Polytechnic Institute and State University, Blacksburg, Virginia
[47] Maniktala, S.; “Switching Power Supply Design and Optimization”, McGraw-Hill
Professional, First Edition, ISBN 0071434836
Other References
Buhler H (1986) Sliding mode control (in French: Reglage ́
par mode de glissement). Presses
Polytechniques Romandes, Lausanne
Carpita M, Marchesoni M (1996) Experimental study of a power conditioning system using sliding
mode control. IEEE Trans Power Electron 11(5):731–742
Carrasco JM, Quero JM, Ridao FP, Perales MA, Franquelo LG (1997) Sliding mode control of a
DC/DC PWM converter with PFC implemented by neural networks. IEEE Trans Circuit Syst I
Fundam Theor Appl 44(8):743–749
DeBattista H, Mantz RJ, Christiansen CF (2000) Dynamical sliding mode power control of wind
driven induction generators. IEEE Trans Energy Convers 15(4):728–734
DeCarlo RA, Zak ̇
SH, Drakunov SV (2011) Variable structure, sliding mode controller design. In:
Levine WS (ed) The control handbook—control system advanced methods. CRC Press, Taylor
& Francis Group, Boca Raton, pp 50-1–50-22
Emelyanov SV (1967) Variable structure control systems. Nauka, Moscow (in Russian)
Filippov AF (1960) Differential equations with discontinuous right hand side. Am Math Soc
Transl 62:199–231
Guffon S (2000) Modelling and variable structure control for active power filters (in French:
“Modelisation ́
et commandes `
a structure variable de filtres actifs de puissance”). Ph.D. thesis,
Grenoble Institute of Technology, France
Guffon S, Toledo AS, Bacha S, Bornard G (1998) Indirect sliding mode control of a three-phase
active power filter. In: Proceedings of the 29th annual IEEE Power Electronics Specialists
Conference – PESC 1998. Kyushu Island, Japan, pp 1408–1414
Hung JY, Gao W, Hung JC (1993) Variable structure control: a survey. IEEE Trans Ind Electron
40(1):2–22
Itkis U (1976) Control systems of variable structure. Wiley, New York
Levant A (2007) Principles of 2-sliding mode design. Automatica 43(4):576–586
Levant A (2010) Chattering analysis. IEEE Trans Autom Control 55(6):1380–1389
Malesani L, Rossetto L, Spiazzi G, Tenti P (1995) Performance optimization of Cuk ́
converters by
sliding-mode control. IEEE Trans Power Electron 10(3):302–309
Malesani L, Rossetto L, Spiazzi G, Zuccato A (1996) An AC power supply with sliding mode
control. IEEE Ind Appl Mag 2(5):32–38
Martinez-Salamero L, Calvente J, Giral R, Poveda A, Fossas E (1998) Analysis of a bidirectional
coupled-inductor Cuk ́
converter operating in sliding mode. IEEE Trans Circuit Syst I Fundam
Theor Appl 45(4):355–363
Mattavelli P, Rossetto L, Spiazzi G (1997) Small-signal analysis of DC–DC converters with
sliding mode control. IEEE Trans Power Electron 12(1):96–102
ˇ
Sabanovic A (2011) Variable structure systems with sliding modes in motion control—a survey.
IEEE Trans Ind Inform 7(2):212–223
Sabanovic ˇ
A, Fridman L, Spurgeon S (2004) Variable structure systems: from principles to
implementation, IEE Control Engineering Series. The Institution of Engineering and Technol-
ogy, London
References:
Sira-Ramırez ́
H (1987) Sliding motions in bilinear switched networks. IEEE Trans Circuit Syst 34
(8):919–933
Sira-Ramırez ́
H (1988) Sliding mode control on slow manifolds of DC to DC power converters. Int
J Control 47(5):1323–1340
Sira-Ramırez ́
H (1993) On the dynamical sliding mode control of nonlinear systems. Int J Control
57(5):1039–1061
Sira-Ramırez ́
H (2003) On the generalized PI sliding mode control of DC-to-DC power converters:
a tutorial. Int J Control 76(9/10):1018–1033
Sira-Ramırez ́
H, Silva-Ortigoza R (2006) Control design techniques in power electronics devices.
Springer, London
Slotine JJE, Sastry SS (1983) Tracking control of non-linear systems using sliding surface, with
application to robot manipulators. Int J Control 38(2):465–492
Spiazzi G, Mattavelli P, Rossetto L, Malesani L (1995) Application of sliding mode control to
switch-mode power supplies. J Circuit Syst Comput 5(3):337–354
Tan S-C, Lai YM, Cheung KHM, Tse C-K (2005) On the practical design of a sliding mode
voltage controlled buck converter. IEEE Trans Power Electron 20(2):425–437
Tan S-C, Lai Y-M, Tse C-K (2011) Sliding mode control of switching power converters:
techniques and implementation. CRC Press, Taylor & Francis Group, Boca Raton
Utkin VA (1972) Equations of sliding mode in discontinuous systems. Autom Remote Control 2
(2):211–219
Utkin VA (1977) Variable structure systems with sliding mode. IEEE Trans Autom Control 22
(2):212–222
Utkin V (1993) Sliding mode control design principles and applications to electric drives. IEEE
Trans Ind Electron 40(1):23–36
Venkataramanan R, Sabanovic ˇ
A, Cuk ́
S (1985) Sliding mode control of DC-to-DC converters. In:
Proceedings of IEEE Industrial Electronics Conference – IECON 1985. San Francisco,
California, USA, pp 251–258
Young KD, Utkin VI, Ozguner U (1999) A control engineer’s guide to sliding mode control. IEEE
Trans Control Syst Technol 7(3):328–342
REFERENCES
1. McLyman, Colonel Wm. T., Transformer and Inductor Design Handbook, Marcel Dekker, New York,
1978. ISBN 0-8247-6801-9.
2. McLyman, Colonel Wm. T., Magnetic Core Selection for Transformers and Inductors, Marcel Dekker,
New York, 1982. ISBN 0-8247-1873-9.
3. Kraus, John D., Ph.D., Electromagnetics, McGraw-Hill, New York, 1953.
4. Boll, Richard, Soft Magnetic Materials, Heydon & Sons, London, 1979. ISBN 0-85501-263-3. & ISBN
3-8009-1272-4.
5. Smith, Steve, Magnetic Components, Van Nostrand Reinhold, New York, 1985. ISBN 0-442-20397-7.
6. Grossner, Nathan R., Transformers for Electronic Circuits, McGraw-Hill, New York, 1983. ISBN 0-07-
024979-2.
7. Lee, R., Electronic Transformers and Circuits, Wiley, New York, 1955.
8. Snelling, E. C., Soft Ferrites—Properties and Applications, Iliffe, London, 1969.
9. Middlebrook, R. D., and Cuk, ́
Slobodan, Advances in Switch Power Conversion, Vols. I and II, Teslaco,
Calif., 1983.
́
10. Cuk, Slobodan, and Middlebrook, R. D., Advances in Switchmode Power Conversion, Vol. III, Teslaco,
Calif., 1983.
11. Landee, Davis, and Albrecht, Electronic Designer’s Handbook, McGraw-Hill, New York, 1957.
12. The Royal Signals, Handbook of Line Communications, Her Majesty’s Stationery Office, 1947.
13. Langford-Smith, F., Radio Designer’s Handbook, Iliffe & Son, London, 1953.
14. Pressman, Abraham I., Switching and Linear Power Supply, Power Converter Design, Haydon, 1977.
ISBN 0-8104-5847-0.
15. Dixon, Lloyd H., and Potel Raoji, Unitrode Switching Regulated Power Supply Design Seminar Manual,
1985.
16. Severns, Rudolph P., and Bloom, Gordon E., Modern DC-to-DC Switchmode Power Converter Circuits,
Van Nostrand Reinhold, New York, 1985. ISBN 0-422-21396-4.
17. Hnatek, Eugene R., Design of Solid-State Power Supplies, 2d Ed., Van Nostrand Reinhold, New York,
1981. ISBN 0-442-23429-5.
18. Shepard, Jeffrey D., Power Supplies, Restin Publishing Company, 1984. ISBN 0-8359-5568-0.
19. Chryssis, George, High Frequency Switching Power Supplies, McGraw-Hill, New York, 1984. ISBN
0-07-010949-4.
20. Kit Sum, K., Switchmode Power Conversion, Marcel Dekker, New York, 1984. ISBN 0-8247-7234-2.
21. Oxner, Edwin S., Power FETs and Their Applications, Prentice-Hall, Englewood Cliffs, N.J., 1982.
22. Bode, H., Network Analysis and Feedback Amplifier Design, Van Nostrand, Princeton, N.J., 1945.
23. Geyger, W., Nonlinear-Magnetic Control Devices, Wiley, New York, 1964.
24. Tarter, Ralph E., Principles of Solid-State Power Conversion, Howard W. Sams, Indianapolis, 1985.
25. Hanna, C. R., “Design of Reactances and Transformers Which Carry Direct Current,” Trans. AIEE,
1927.
26. Schade. O. H., Proc. IRE, July 1943.
27. Venable, D. H., and Foster, S. R., “Practical Techniques for Analyzing, Measuring and Stabilizing Feed-
back Control Loops in Switching Regulators and Converters,” Powercon, 7, 1982.
28. Middlebrook, R. D., “Input Filter Considerations in Design and Application of Switching Regula-
tors,” IEEE Industrial Applications Society Annual Meeting Record, October 1976.
REFERENCES:
29.30.31.32.33.34.35.36.37.38.39.40.41.42.43.44.45.46.47.48.49.50.51.52.53.54.55.56.57.58.59.Middlebrook, R. D., “Design Techniques for Preventing Input Filter Oscillations in Switched-Mode
Regulators,” Proc. Powercon, 5, May 1978.
́
Cuk, Slobodan, “Analysis of Integrated Magnetics to Eliminate Current Ripple in Switching Convert-
ers,” PCI Conference Proceedings, April 1983.
Dowell, P. L., “Effects of Eddy Currents in Transformer Windings,” Proc. IEE, 113(8), 1966.
Smith, C. H., and Rosen, M., “Amorphous Metal Reactor Cores for Switching Applications,” Proceed-
ings, International PCI Conference, Munich, September 1981.
Jansson, L., “A Survey of Converter Circuits for Switched-Mode Power Supplies,” Mullard Technical
Communications, Vol. 12, No. 119, July 1973.
“Switchers Pursue Linears Below 100 W,” Electronic Products, September 1981.
Snigier, Paul., “Those Sneaky Switchers,” Electronic Products, March 1980, and “Power Supply Selec-
tion Criteria,” Digital Design, August 1981.
Boschert, Robert J., “Reducing Infant Mortality in Switches,” Electronic Products, April 1981.
Shepard, Jeffrey D., “Switching Power Supplies: the FCC, VDE, and You,” Electronic Products, March 1980.
Royer, G. H., “A Switching Transistor DC to AC Converter Having an Output Frequency Proportional
to the DC Input Voltage,” AIEE, July 1955.
Jensen, J., “An Improved Square Wave Oscillator Circuit,” IERE Trans. on Circuit Theory, September 1957.
IEEE Std. 587-1980, “IEEE Guide for Surge Voltages in Low-Voltage AC Power Circuits,” ANSI/IEEE
C62-41-1980.
“Transformer Core Selection for SMPS,” Mullard Technical Publication M81-0032, 1981.
“Radio Frequency Interference Suppression in Switched-Mode Power Supplies,” Mullard Technical
Note 30, 1975.
Owen, Greg, “Thermal Management Techniques Keep Semiconductors Cool,” Electronics, Sept. 25, 1980.
Pearson, W. R., “Designing Optimum Snubber Circuits for the Transistor Bridge Configuration.” Proc.
Powercon, 9, 1982.
Severns, R., “A New Improved and Simplified Proportional Base Drive Circuit,” Intersil.
Redl, Richard, and Sokal, Nathan O., “Optimizing Dynamic Behaviour with Input and Output Feed-
forward and Current-mode Control,” Proc. Powercon, 7, 1980.
Middlebrook, R. D., Hsu, Shi-Ping, Brown, Art, and Rensink, Lowman, “Modelling and AnalysisSwitching DC-DC Converters in Constant-Frequency Current-Programmed Mode,” IEEE Power Elec-
tronics Specialists Conference, 1979.
Bloom, Gordon (Ed), and Severns, Rudy, “Magnetic Integration Methods for Transformers,” in Isolated
Buck and Boost DC-DC Converters, 1982.
Hetterscheid, W., “Base Circuit Design for High-Voltage Switching Transistors in Power Converters,”
Mullard Technical Note 6, 1974.
Gates, T. W., and Ballard, M. F., “Safe Operating Area for Power Transistors,” Mullard Technical
Communications, Vol. 13, No. 122, April 1974.
Dean-Venable, H., “The K Factor: A New Mathematical Tool for Stability Analysis and Synthesis,” Proc.
Powercon, 10, March 1983.
Dean-Venable, H., and Foster, Stephen R., “Practical Techniques for Analyzing, Measuring, and Stabi-
lizing Feedback Control Loops in Switching Regulators and Converters,” Proc. Powercon, 7, 1980.
Tuttle, Wayne H., “The Relationship of Output Impedance to Feedback Loop Parameters,” PCIM,
November 1986.
Dean-Venable, H., “Stability Analysis Made Simple,” Venable Industries, Torrance, Calif., 1982.
of
Tuttle, Wayne H., “Relating Converter Transient Response to Feedback Loop Design,” Proc. Powercon,
11, 1984.
Dean-Venable, H., “Optimum Feedback Amplifier Design Control Systems,” Proc. IECEC, August 1986.
Tuttle, Wayne H., “Why Conditionally Stable Systems Do Not Oscillate,” Proc. PCI, October 1985.
Jongsma, J., and Bracke, L. P. M., “Improved Method of Power-Coke Design,” Electronic Compo-
nents and Applications, vol. 4, no. 2, 1982.
Bracke, L. P. M., and Geerlings, F. C., “Switched-Mode Power Supply Magnetic Component Require-
ments,” Philips Electronic Components and Materials, 1982.
REFERENCES:
60. Carsten, Bruce, “High Frequency Conductor Losses in Switchmode Magnetics,” PCIM, November 1986.
61. Clarke, J. C., “The Design of Small Current Transformers,” Electrical Review, January 1985.
62. Houldsworth, J. A., “Purpose-Designed Ferrite Toroids for Isolated Current Measurements in Power
Electronic Equipment,” Mullard Technical Publication M81-0026, 1981.
63. Cox, Jim, “Powdered Iron Cores and a New Graphical Aid to Choke Design,” Powerconversion Interna-
tional, February 1980.
64. Cox, Jim, “Characteristics and Selection of Iron Powder Cores for Induction in Switchmode Convert-
ers,” Proc. Powercon, 8, 1981.
65. Cattermole, Patrick A., “Optimizing Flyback Transformer Design.” Proc. Powercon, 1979, PC 79-1-3.
66. Geerlings, F. C., and Bracke, L. P. M., “High-Frequency Ferrite Power Transformer and Choke Design,
Part 1,” Electronic Components and Applications, vol. 4, no. 2, 1982.
67. Jansson, L. E., “Power-handling Capability of Ferrite Transformers and Chokes for Switched-Mode
Power Supplies,” Mullard Technical Note 31, 1976.
68. Hirschmann, W., Macek, O., and Soylemez, A. I., “Switching Power Supplies 1 (General, Basic Circuits),”
Siemens Application Note.
69. Ackermann, W., and Hirschmann, W., “Switching Power Supplies 2, (Components and Their Selection
and Application Criteria),” Siemens Application Note.
70. Schaller, R., “Switching Power Supplies 3, (Radio Interference Suppression),” Siemens Application Note.
71. Macek, O., “Switching Power Supplies 4, (Basic Dimensioning), “Siemens Application Note.
72. Bulletin SFB, Buss Small Dimension Fuses, Bussmann Division, McGraw-Edison Co., Missouri.
73. Catalog #20, Littlefuse Circuit Protection Components, Littlefuse Tracor, Des Plaines, III.
74. Bulletin-B200, Brush HRC Current Limiting Fuses, Hawker Siddeley Electric Motors, Canada.
75. Bulletins PC-104E and PC109C, MPP and Iron Powder Cores, The Arnold Engineering Co., Marengo,
Illinois.
76. Publication TP-25-575, HCR Alloy, Telcon Metals Ltd., Sussex, England.
77. Catalog 4, Iron Powder Toridal Cores for EMI and Power Filters, Micrometals, Anaheim, Calif.
78. Bulletin 59–107, Soft Ferrites, Stackpole, St. Marys, Pa.
79. SOAR—The Basis for Reliable Power Circuit Design, Philips Product Information #68.
80. Bennett, Wilfred P., and Kurnbatovic, Robert A., “Power and Energy Limitations of Bipolar Transistors
Imposed by Thermal-Mode and Current-Mode Second-Breakdown Mechanisms,” IEEE Transactions
on Electron Devices, vol. ED28, no. 10, October 1981.
81. Roark, D. “Base Drive Considerations in High Power Switching Transistors,” TRW Applications Note
#120, 1975.
82. Gates, T. W., and Ballard, M. F., “Safe Operating Area for Power Transistors,” Mullard Technical Com-
munications, vol. 13, no. 122, April 1974.
83. Williams, P. E., “Mathematical Theory of Rectifier Circuits with Capacitor-Input Filters,” Power Con-
version International, October 1982.
84. “Guide for Surge Voltages in Low-Voltage AC Power Circuits,” IEC Publication 664, 1980.
85. Kit Sum, K., PCIM, February 1998.
86. Spangler, J., Proc. Sixth Annual Applied Power Electronics Conf., Dallas, March 10–15, 1991.
87. Neufeld, H., “Control IC for Near Unity Power Factor in SMPS,” Cherry Semiconductor Corp., October 1989.
88. Micro Linear application notes 16 and 33.
89. Micro Linear application note 34.
90. Micrometals’ “Power Conversion & Line Filter Applications” data book.
91. Pressman, Abraham I., Billings, Keith, Morey, Taylor, Switching Power Supply Design, McGraw-Hill,
2009. ISBN 978-0-07-148272-1.
92. Texas Instruments/Unitrode Data Sheet UCC3895 SLUS 157B & application notes U136A & U154.
93. Stanley, William D., Operational Amplifiers with Linear Integrated Circuits, 2d Ed., Merrill, Columbus,
Ohio, 1989. ISBN 067520660-X.
94. “LM13700 Dual Operational Transconductance Amplifiers with Linearizing Diodes and Buffers,”
National Semiconductor Corporation, 2004. http://www.national.com/ds/LM/LM13700.pdf.
Further References:
1. G. Aboud, Cathode Ray Tubes, 1997, 2nd ed., San Jose, CA, Stanford Resources, 1997.
2. G. Aboud, Cathode Ray Tubes, 1997, Internet excerpts, available http://www.stanfordresources.com/
sr/crt/crt.html, Stanford Resources, February 1998.
3. G. Shires, Ferdinand Braun and the Cathode Ray Tube, Sci. Am., 230 (3): 92–101, March 1974.
4. N. H. Lehrer, The challenge of the cathode-ray tube, in L. E. Tannas, Jr., Ed., Flat Panel Displays
and CRTs, New York: Van Nostrand Reinhold, 1985.
5. P. Keller, The Cathode-Ray Tube, Technology, History, and Applications, New York: Palisades Press,
1991.
6. D. C. Ketchum, CRT’s: the continuing evolution, Society for Information Display International
Symposium, Conference Seminar M-3, 1996.
7. L. R. Falce, CRT dispenser cathodes using molybdenum rhenium emitter surfaces, Society for
Information Display International Symposium Digest of Technical Papers, 23: 331–333, 1992.
8. J. H. Lee, J. I. Jang, B. D. Ko, G. Y. Jung, W. H. Kim, K. Takechi, and H. Nakanishi, Dispenser
cathodes for HDTV, Society for Information Display International Symposium Digest of Technical
Papers, 27: 445–448, 1996.
9. T. Nakadaira, T. Kodama, Y. Hara, and M. Santoku, Temperature and cutoff stabilization of
impregnated cathodes, Society for Information Display International Symposium Digest of Technical
Papers, 27: 811–814, 1996.
10. W. Kohl, Materials Technology for Electron Tubes, New York, Reinhold Publishing, 1951.
11. S. Sugawara, J. Kimiya, E. Kamohara, and K. Fukuda, A new dynamic-focus electron gun for color
CRTs with tri-quadrupole electron lens, Society for Information Display International Symposium
Digest of Technical Papers, 26: 103–106, 1995.
12. J. Kimiya, S. Sugawara, T. Hasegawa, and H. Mori, A 22.5 mm neck color CRT electron gun with
simplified dynamically activated quadrupole lens, Society for Information Display International
Symposium Digest of Technical Papers, 27: 795–798, 1996.
13. D. Imabayashi, M. Santoku, and J. Karasawa, New pre-focus system structure for the trinitron gun,
Society for Information Display International Symposium Digest of Technical Papers, 27: 807–810,
1996.
14. K. Kato, T. Sase, K. Sasaki, and M. Chiba, A high-resolution CRT monitor using built-in ultrasonic
motors for focus adjustment, Society for Information Display International Symposium Digest of
Technical Papers, 27: 63–66, 1996.
15. S. Sherr, Electronic Displays, 2nd ed., New York: John Wiley, 1993.
16. N. Azzi and O. Masson, Design of an NIS pin/coma-free 108° self-converging yoke for CRTs with
super-flat faceplates, Society for Information Display International Symposium Digest of Technical
Papers, 26: 183–186, 1995.
17. J. F. Fisher and R. G. Clapp, Waveforms and spectra of composite video signals, in K. Benson and
J. Whitaker, Television Engineering Handbook, Featuring HDTV Systems, New York: McGraw-Hill
Reinhold, 1992.
18. D. Pritchard, Standards and recommended practices, in K. Benson and J. Whitaker, Television
Engineering Handbook, Featuring HDTV Systems, New York: McGraw-Hill Reinhold, 1992.
19. A. Vecht, Phosphors for color emissive displays, Society for Information Display International Sym-
posium Conference Seminar Notes F-2, 1995.
20. Optical Characteristics of Cathode Ray Tube Screens, EIA publication TEP116-C, Feb., 1993.
21. G. Wyszecki and W. S. Stiles, Color Science: Concepts and Methods, Quantitative Data and Formulae,
2nd ed., New York: John Wiley & Sons, 1982.
© 1999 by CRC Press LLC
22. A. Robertson and J. Fisher, Color vision, representation, and reproduction, in K. Benson and J.
Whitaker, Television Engineering Handbook, Featuring HDTV Systems, New York: McGraw-Hill
Reinhold, 1992.
23. M. Maeda, Trinitron technology: current status and future trends, Society for Information Display
International Symposium Digest of Technical Papers, 27: 867–870, 1996.
24. C. Sherman, Field sequential color takes another step, Inf. Display, 11 (3): 12–15, March, 1995.
25. L. Ozawa, Helmet mounted 0.5 in. crt for SVGA images, Society for Information Display Interna-
tional Symposium Digest of Technical Papers, 26: 95–98, 1995.
26. C. Infante, CRT display measurements and quality, Society for Information Display International
Symposium Conference Seminar Notes M-3, 1995.
27. J. Whitaker, Electronic Displays, Technology, Design, and Applications, New York: McGraw-Hill, 1994.
28. P. Keller, Electronic Display Measurement, Concepts, Techniques, and Instrumentation, New York:
John Wiley & Sons, 1997.
Further Information
L. Ozawa, Cathodoluminescence: Theory and Applications, New York: Kodansha, 1990.
V. K. Zworykin and G. A. Morton, Television: The Electronics of Image Transmission in Color and Mono-
chrome, New York: John Wiley & Sons, 1954.
B. Wandell, The foundations of color measurement and color perception, Society for Information Display
International Symposium, Conference Seminar M-1, 1993. A nice brief introduction to color science
(31 pages).
Electronic Industries Association (EIA), 2500 Wilson Blvd., Arlington, VA 22201 (Internet: www.eia.org).
The Electronic Industries Association maintains a collection of over 1000 current engineering publi-
cations and standards. The EIA is an excellent source for information on CRT engineering, standards,
phosphors, safety, market information, and electronics in general.
The Society for Information Display (SID), 1526 Brookhollow Dr., Suite 82, Santa Ana, CA 92705-5421
(Internet: www.display.org). The Society for Information Display is a good source of engineering
research and development information on CRTs and information display technology in general.
Internet Resources:
The following is a brief list of places to begin looking on the World Wide Web for information on CRTs
and displays, standards, metrics, and current research. Also many of the manufacturers listed in Table
91.3 maintain Web sites with useful information.
The Society for Information Display
The Society of Motion Picture and Television Engineers
The Institute of Electrical and Electronics Engineers
The Electronic Industries Association
National Information Display Laboratory
The International Society for Optical Engineering
The Optical Society of America
Electronics & Electrical Engineering Laboratory
National Institute of Standards and Technology (NIST)
The Federal Communications Commission
www.display.org
www.smpte.org
www.ieee.org
www.eia.org
www.nta.org
www.spie.org
www.osa.org
www.eeel.nist.gov
www.nist.gov
www.fcc.gov
No comments:
Post a Comment
The most important thing to remember about the Comment Rules is this:
The determination of whether any comment is in compliance is at the sole discretion of this blog’s owner.
Comments on this blog may be blocked or deleted at any time.
Fair people are getting fair reply. Spam and useless crap and filthy comments / scrapers / observations goes all directly to My Private HELL without even appearing in public !!!
The fact that a comment is permitted in no way constitutes an endorsement of any view expressed, fact alleged, or link provided in that comment by the administrator of this site.
This means that there may be a delay between the submission and the eventual appearance of your comment.
Requiring blog comments to obey well-defined rules does not infringe on the free speech of commenters.
Resisting the tide of post-modernity may be difficult, but I will attempt it anyway.
Your choice.........Live or DIE.
That indeed is where your liberty lies.
Note: Only a member of this blog may post a comment.