
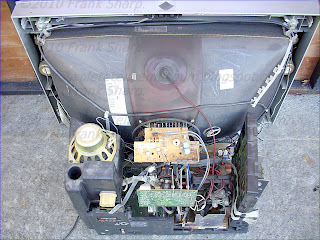
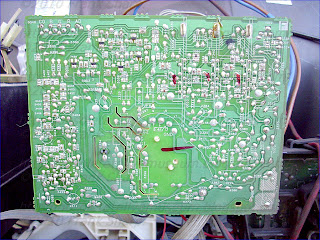

CRT TUBE PHILIPS W76ERF031X044.
These tubes are with Impregnated catode technology for Increased Emission level and Invar MASK and Blackmatrix.
(they have had a discrete failure rate in cathode structure landing to a often faulty tube)
Technology Overview:
The electron emitter of a conventional dispenser
hollow cathode is an impregnated porous tungsten
tube (the insert). The
emitter is contained in a refractory metal cathode
tube with an orifice plate on the downstream
end. A small fraction of the thruster propellant
is injected through the hollow cathode, and the
orifice serves to increase the internal pressure in
the insert region. Electron emission from the inner
surface maintains an internal plasma which
heats the insert to the required operating temperature
and helps conduct the current into the
main discharge. A heater surrounding the cathode
tube is used to preheat the cathode prior to
ignition.
The key to long insert life is to maintain a low
temperature for a given electron emission current
density by establishing a layer of adsorbed
oxygen and barium atoms that lowers the surface
work function. In state-of-the-art impregnated
cathodes Ba and BaO are supplied by barium
calcium aluminate source material (the im-
Figure 2: Thermogravimetric analyses of impregnant
material sensitivity to water vapor in
the environment.
pregnant) incorporated in the pores of the tungsten.
Gaseous Ba and BaO are released in interfacial
reactions between the tungsten matrix
and the impregnant, producing a temperaturedependent
vapor pressure of these species inside
the pores. The Ba and BaO then diffuse through
the pores to the surface and replenish Ba and O
adsorbates lost by evaporation.
The lifetime of these emitters is limited by
exhaustion of the barium- and barium oxideproducing
impregnant [3]. When the supply rate
of barium to the surface drops below the value
needed to balance evaporative losses due to consumption
of the impregnant or reduced transport
rates through product layers or through the
pores, the electron emission capability of the surface
degrades. The emitters are also sensitive to
reactive gases, particularly oxygen and water vapor.
Prior to launch, the impregnant material
absorbs water vapor at room temperature. Figure
(2) shows the mass gain observed for various
impregnant materials in thermogravimetric analyses
[6]. This is to some extent reversible and
absorbed impurities can be baked out prior to
operation, but experience has demonstrated that
only a limited number of air exposure cycles can
be tolerated before irreversible damage is done.
Flight systems therefore typically use inert gas
storage and purges to limit exposure time.
(In the future these tube were failing often with catode shorts to G1, but at least not all)
In beam scan velocity modulation (SVM) system for a television receiver,

a video signal is applied to a differentiator followed by a limiting differential amplifier. A driver amplifier coupled to the limiting amplifier drives an output stage that supplies current to an SVM coil. Certain video signals with large high frequency content may tend to produce excessive dissipation in the devices of the output stage. To prevent this, a current source for the differential amplifier is controlled by a voltage which is a measure of the average current through the output stage. The magnitude of the current source is varied to thereby vary the peak-to-peak signal output from the limiting amplifier to prevent overdissipation of the output devices. The presence of random noise in the video signal can produce unwanted SVM operation which can impair the viewed image. The unwanted noise component in the video signal can be reduced in amplitude by coring. The coring is unaffected by the variable limiting.
Scan velocity modulation apparatus:
A scan velocity modulation (SVM) coil arrangement for a cathode ray tube has SVM coils arranged on a rear portion of the main horizontal deflection coils. The main horizontal coils are of the saddle type and have flat end turns at the rear of the deflection coil, lying along the surface of the picture tube. The SVM coil is placed over the flat rear end turns forward of the static convergence magnets and forward of ferromagnetic materials associated with the electron gun. The sensitivity of the SVM coil is increased to the point that the coil can be efficiently driven in a progressively scanned raster display, at twice the horizontal rate of an interleaved raster display.
1. A scan velocity modulation apparatus for a cathode ray tube, the cathode ray tube including an electron gun adjacent a rear end of the tube, for emitting an electron beam along a beam path from the electron gun through a funnel of the tube to a screen at a front of the tube, the apparatus comprising:
a static convergence magnet assembly disposed over the electron beam path;
a primary deflection yoke including a vertical deflection winding for vertical deflection of the beam and a horizontal deflection coil for horizontal deflection of the beam, the horizontal deflection coil having end turns at a rear end, disposed substantially adjacent to the static convergence magnet; and
a scan velocity modulation coil for modifying said horizontal deflection of the electron beam, the scan velocity modulation coil located along the longitudinal axis of the tube adjacent the horizontal deflection coil, with one of the two coils at least partly overlapping the other coil.
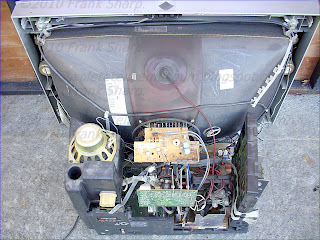
a static convergence magnet assembly disposed over the electron gun;
a primary deflection yoke including a core a vertical deflection coil for vertical deflection of the beam and a horizontal deflection coil for horizontal deflection of the beam, the horizontal deflection coil having end turns at a rear end, disposed substantially adjacent to the static convergence magnet;
a scan velocity modulation coil for modifying said horizontal deflection of the electron beam, the scan velocity modulation coil located along the longitudinal axis of the tube forward and without overlap of the static convergence magnet assembly and rearward and without overlap of the core; and
means for exciting the scan velocity modulation coil for varying a horizontal scan rate of said electron beam.
Scan velocity modulation is known in beam deflection of cathode ray tubes, and is employed in order to obtain improved contrast and sharpness of the picture. The basic idea is to change the horizontal scan velocity of the electron beam during a transition from light to dark or dark to light along the scanning pattern. Assuming, for example, that the scan is to pass across a bright vertical line on a dark background, the objective is to reproduce a display wherein the luminance of the screen for each horizontal scan crossing the line rises instantly from a minimum in the dark area to a maximum at the line, and drops instantly from the maximum to the minimum upon passing the line. However, the rise and fall times of the electron beam current and phosphor light output are not zero. The actual display (with scan velocity modulation not in use) has shades of gray at the transitions, which the viewer perceives as a lack of sharpness or a blurring at the transitions.
With beam scan velocity modulati

The beam velocity modulation is applied using an additional deflection coil operable to modify the horizontal deflection of the beam. The additional deflection coil is excited by a driver circuit that amplifies the luminance video signal, differentiates the luminance and then discards all of the video signal except the level transitions. The SVM coil typically drives a flat wound laminated coil on or within the purity/static convergence magnet holder.
Deflection coils are typically mounted to a glass picture tube on a plastic deflection yoke form. A horizontal deflection field is produced by a saddle shaped coil arrangement placed on the neck of the tube, and a vertical deflection field is produced by a toroidal coil arrangement wound around a core placed around the tube neck. These coils are disposed on the funnel or flaring portion of the tube forward of the electron gun, which is at the extreme rear of the tube.
It is desirable to place the SVM coil as close as possible to the electron beam, so that the available power of the magnetic field generated for scan velocity modulation is applied to the electron beam without decrease in field strength due to spacing. Moreover, spacing is at a premium. A typical SVM coil is mounted in a manner that represents certain compromises. While the SVM coil may be placed close to the beam, it is also close to ferrous and/or conductive materials.
According to the prior art, the SVM coil is mounted on the rear of the deflection yoke form, in close proximity with the electron gun and overlapping portions of the electron gun along the longitudinal or Z-axis. The SVM coil is associated with the static convergence magnets, which are typically defined for a nonadjustable type by means of a tape of plastic binder with embedded ferrous powder (e.g., barium ferrite), placed to the rear of the deflection yoke at the electron gun, and magnetized during initial setup of the deflection yoke to cause the respective beams of the electron gun to converge at a point.
The mounting of the SVM coil to the rear of the deflection yoke also places the SVM coil in immediate proximity with the electron gun structure. The electron gun normally include permeable ferromagnetic material (e.g., steel) that to a certain extent may confine the lines of flux of the SVM field to the permeable material, preventing application to the beam path of the full field strength which the SVM coil otherwise could produce. Insofar as the electron gun includes non-ferromagnetic conductive material, eddy currents may be induced, tending to waste the power of the SVM field in resistive heating of the conductive materials. In short, the ferrous and conductive material of the electron guns tends to reduce the strength of the SVM field interacting with the electron beams.
Although it is possible to combat adverse effects inherent in a particular mounting location of an SVM coil by increasing the drive current, number of coil turns or the like until the resultant magnetic field applied to the beam is sufficient to obtain the required extent of deflection for scan velocity modulation, there are other problems associated with such changes. For example, increasing the number of turns of the SVM coil affects its inductance and operability at the required frequencies for the differentiated video signal. Increasing the current requires improved performance current drivers and/or a higher voltage power supply. These means for resolving needed improvements in SVM performance can be expensive.
The problems mentioned are more difficult in television apparatus using a progressively scanned raster rather than a raster of successive interleaved fields. A progressively scanned raster operates at double the usual horizontal scanning rate in order to scan all the lines of the video frame (e.g., 625 lines in PAL) during the time previously allowed for one of two interleaved fields. The frequencies employed in the video signal, which is differentiated to obtain the SVM drive signal, are twice as fast (2f H ) as the frequencies in the interleaved field arrangement (f H ). Nevertheless, the magnetic field required of the SVM coil to obtain a given amount of deflection must be about the same as before, because the extent of auxiliary deflection of the electrons in the beams is a function of field strength. As a result, the SVM driving circuitry must produce large amplitude current pulses, but due to the higher scanning rate, the current pulses are of shorter duration. This places severe demands on the SVM coil driving circuitry, and may lead to additional expense in the provision of higher powered and faster components.
It is an aspect of the invention to relieve demands on the SVM driving circuitry insofar as possible by maximizing the sensitivity of the SVM coil.
It is a further aspect of the invention to distance the SVM coil arrangement from ferrous and other metallic materials associated with the electron guns.
It is also an aspect of the invention to achieve an improved sensitivity SVM coil mounting in a manner that does not add to the dimensions of the picture tube along the electron beam axis or Z-axis and readily can be accomplished on a short neck tube.
In an inventive arrangement, a scan velocity modulation (SVM) coil arrangement wherein the SVM coils are arranged to overlap a rear portion of the main horizontal deflection coils along the Z-axis. The main horizontal coils may be of the saddle type and have straight end turns, i.e., flat windings at the rear of the deflection coil, lying along the surface of the picture tube. The SVM coil may be placed over the flat rear turns of the main horizontal deflection coil, to the rear of the core around which the vertical deflection coil is wrapped. The SVM coil is thus placed well clear of ferromagnetic and most conductive materials associated with the electron gun, and in relatively close proximity with the electron beam. The sensitivity of the SVM coil is improved to the point that the coil can be driven in a progressive raster display, at twice the horizontal rate(i.e., 2fH) for interleaved raster display, using substantially the same sort of driving circuitry formerly employed with SVM coils used in conjunction with interlaced scanning at fH.
FIG. 1 is a partial side section view in elevation, showing a cathode ray tube, deflection yoke and SVM coil arrangement according to the invention, the tube shown partly cut away to reveal the electron gun structure;
FIG. 2 is a side elevation thereof, showing the full television tube;
FIG. 3 is a vertically exploded perspective view showing the relationship of the electron gun, static convergence magnets, horizontal deflection coils and SVM coil;
FIG. 4 is an elevation view of a television screen, having a contrasting bright bar disposed on a background;
FIG. 5 is a time diagram showing the video drive signal and the SVM drive signal applied in the case of a display as shown in FIG. 4;
FIG. 6 is a schematic circuit diagram showing the beam deflection arrangement driving the SVM coil of the invention.
With reference to FIGS. 1 and 2, a television picture tube 30 is arranged with an electron gun 40 at a rear end 32, emitting a stream of electrons which are accelerated toward the phosphor screen 34 at the opposite or front end. The luminance (brightness) of light emission by the screen is determined in part by the current level of incident electrons emitted by the electron gun 40 and striking the phosphors at any particular point on the screen. The electrons are moving charges and constitute a current, whereby the electrons are deflected by incident magnetic fields. The electron beam is deflected at a horizontal scanning rate to trace successive lines, and at a vertical scanning rate to cause the successive lines to be vertically spaced from one another on the screen, the scanning defining a raster pattern which is repeated in
interleaved fields or in progressive scans of each successive line in turn.
The television tube or cathode ray tube 30 has a funnel shaped or flaring portion 38 between the electron gun end 32 and the screen 34. Deflection coils for vertical deflection and horizontal deflection are mounted on a deflection yoke arrangement 70 on the funnel portion 38 of the tube, typically being wound on a plastic yoke form or liner 72. The vertical and horizontal deflection coils 80, 90 are elongated along the funnel in a longitudinal direction, parallel to the electron beam axis 42, and follow along the flaring surface 38 of the tube 30. The vertical deflection coils or windings are wrapped toroidally on a magnetically permeable core 71 and the horizontal deflection windings rest against the surface 38 of the tube. The vertical windings are disposed in the area of 6 and 12 o'clock as viewed along the beam axis and the horizontal windings are at 3 and 9 o'clock. The vertical deflection coils produce horizontal magnetic flux lines intersecting the beam path (causing vertical displacement) and the horizontal coils produce vertical flux (for horizontal displacement). The horizontal deflection coils operate at a higher frequency than the vertical coils to accomplish line scanning, and for saddle type coils are typically placed on the inside of the deflection yoke liner, adjacent the outer surface 38 of the tube 30, closer to the electron beams, as shown in FIG. 1. The vertical deflection coils are outside the liner on the core, as shown in FIGS. 1 and 2.
Assuming that an electron beam scanning across the screen encounters a change in luminance such as a vertical bright line as shown in FIG. 4 (i.e., when the current of the electron beam is increased or decreased to achieve brighter or darker emission from the phosphors on the screen), the rise and fall time of the electron beam current would normally occur
while horizontal scanning proceeds. This produces, in combination with the effects of beam spot profile, an area of increasing brightness approaching a transition to the brighter shade, and an area of decreasing brightness proceeding away from the transition to the darker shade, in the direction of scanning. To combat the lack of resolution or clarity inherent in such a situation, the video drive signal (e.g., the stepwise variation in luminance as shown in FIG. 5) is processed by a beam scan modulation circuit to obtain a signal used to modify the horizontal deflection of the beam at the transitions. For example, when the beam during horizontal scan line 66 as shown in FIG. 4 passes from a darker background 62 to a brighter area 64, the circuit accelerates the beam approaching the transition and decelerates the beam after the transition. Conversely, when passing from the brighter area 64 to a darker area 62, the beam is decelerated approaching the transition and accelerated upon passing the transition. The net change of the accelerations and decelerations encountered along each scan line is zero, such that the scan rate for each full line is equal to the average scan rate. Circuits for producing the SVM current signal shown in FIG. 5 are known in the art. Such circuits anticipate a transition in luminance, and differentiate the luminance of the video signal. The differentiated signal is AC coupled to an auxiliary horizontal deflection coil provided in addition to the main horizontal deflection coil, to obtain the required scan rate modulation by adding the SVM deflection to the deflection produced by the main horizontal deflection coil.
Scan velocity modulation as known in the art may typically be executed by placing an auxiliary coil on the static convergence magnets disposed adjacent the electron gun of the tube. However, the electron gun includes ferromagnetic and conductive material. A portion of the magnetic flux produced by the SVM coil accordingly is applied in an area where the ferromagnetic material of the electron gun tends to confine the lines of flux to magnetically permeable materials. Part of the magnetic field produced by the SVM coil thus becomes confined to a path that does not intersect the electron beam. Furthermore, much of the structure of the gun is conductive metal. Magnetic field variations produced by the SVM coil therefore induce currents in the conductive elements of the gun. Although the SVM coil is placed close to the source of the electrons (i.e., close to the electron gun), part of its power is wasted on resistive heating via eddy currents in the conductive elements of the gun.
An electron gun arrangement is shown in side elevation in FIG. 1. In a color television apparatus, the electron gun has three spaced inline cathodes disposed at the rear end 32 of the tube 30, for red, blue and green colors, respectively, only one being shown in the drawing. The gun has; a control grid electrode G1; a screen grid electrode G2; a first prefocus lens electrode G3; a second prefocus lens electrode G4; a combined third prefocus lens electrode and first quadrupole (multipole) lens electrode G5B; a combined second quadrupole lens electrode and first main focusing lens electrode G5T; and, a second main focusing lens and an acceleration electrode G6, these items being placed in order proceeding from the rear 32 of the tube. The main focus lens point of the gun is in the gap between the G5T and G6 electrodes. At the front of the electron gun, a shield cup 142 is disposed forwardly of the final electrode or anode G6. Shield cup 142 is provided at the front or exit end of the gun 40 and is open on its front. At various ones of the three apertures, by which the electron beams exit electrode G6 into shield cup 142, shunts and enhancers are provided to shield the emerging beams from stray vertical fields, and correct for a convergence error known as coma error.
The gun electrodes are conductive and certain ones of the electrodes may also be ferromagnetic. Electrode G3 is made, for example, of iron nickel 48, and shields the beams from stray vertical fields to prevent spot coma, i.e., to prevent flaring of the electron beam cross sections. The shield cup 142 as noted is provided with ferromagnetic shunts and enhancers for shielding the emerging beams from vertical fields. The grid electrode G1, which must withstand temperature cycling due to its proximity to the heated cathodes, is made for example of stainless steel 430, for low thermal expansion characteristics. This material is also magnetically permeable.
Static convergence magnets 52 are disposed on the tube in immediate proximity to the electron gun as shown in FIG. 1. The convergence magnets are permanent magnets (i.e., producing static magnetic fields) and are used to adjust the convergence of the three electron beams when initially setting up the television tube. In known arrangements, SVM coils are disposed directly on the static convergence magnets, the magnets being formed by ferromagnetic powder embedded in a plastic, for example a plastic tape attached rearward of the deflection yoke liner.
The present inventive arrangement may also use static convergence magnets, for example in the form of a plastic tape 52 with embedded barium ferrite powder, as shown in FIGS. 1-3. However, the SVM coil, coil 100, is located at a distance from the convergence magnets 52, i.e., forward along the beam axis 42, and also substantially forward relative to most of the metallic structure of electron gun 40. According to an inventive feature, the SVM coil is arranged to at least partly overlap the flat rear end turn windings 94 of the main horizontal deflection coils along the Z-axis. According to a different inventive feature, the SVM coil is arranged longitudinally forward of the gun

In such an arrangement, the magnetic field produced by the SVM coil does not significantly interact with ferromagnetic and most of the conductive elements in the electron gun. More of the current used to excite the SVM coil is used to produce a magnetic flux which intersects the electron beam path. As a result the SVM coil is more sensitive than in an arrangement wherein the SVM coil is placed on the convergence magnets or otherwise over several of the electrodes of the gun 40. More of the available output of the SVM driving circuit is put to advantage toward the objective of varying the horizontal beam scanning velocity, to correct for the rise and fall time of the electron beam and to sharpen the contrast of the display at the edges of transitions in luminance.
The SVM coil 100 is placed substantially clear of the electrodes of the electron gun 40. The SVM coil 100 has an upper coil winding 102 and a lower coil winding 104, arranged to overlap (along the Z-axis) the rear turns of the main horizontal deflection coils at the rear of the deflection yoke. These turns of the main horizontal deflection windings advantageously are laid flat on the surface 38 of the tube, with the SVM coil superimposed or placed thereon. The SVM coils thus need be spaced from the tube 30 (and from the electron beam) by only the thickness of the flat rear windings of the horizontal coil. In this manner the SVM coil produces substantially improved beam deflection distance per unit of driving current).
As shown in FIGS. 1 and 2, the SVM coil 100 is mounted on a bobbin 74 at the rear of the deflection yoke liner 72. The upper SVM coil section 102 and lower SVM coil section 104 are connected in parallel and when energized with a current produce a generally dipole vertically oriented magnetic field operable to deflect the electron beam horizontally, effectively modifying the horizontal scan rate of the beam as obtained using the main horizontal deflection coil 90.
The main horizontal deflection coil 90, the SVM coil windings 102 and 104, and the electron gun 40 with static convergence magnet tape 52 thereon, are shown in FIG. 3 with the respective parts disposed in their relative positions along the Z-axis 42, but in an exploded view radially of the beam axis. The windings of the horizontal coil 90 run along the inner surface of the deflection yoke liner 72 (not shown in FIG. 3), defining loops winding along the funnel shaped portion of the deflection yoke liner and extending in a flat configuration at the rear windings 94 of the deflection coil. Successive rear end turn conductors in the coil pass alongside one another on the surface of the coil as rested on the surface of the tube when the deflection yoke is in place.
The SVM coils overlap the flat rear windings of the horizontal deflection coil along the Z-axis at the rear of the deflection yoke. As seen in FIG. 1, the SVM coils can overlap the extreme front of the electron gun structure in the area of the shield cup 142. However, the SVM coils do not overlap the main body of the gun, and also advantageously do not overlap the rear end of core 71 or the rear of the vertical deflection coil.
The SVM sensitivity is substantially improved as compared to known SVM coil arrangements. This enables the SVM coil apparatus to operate at relatively lower current levels, and eases the demands on the driving circuitry therefor, particularly at 2f H scan rates as used for progressive raster scanning.
Due to the increased sensitivity of the SVM coil according to the invention, the SVM coil even at a 2f H scanning rate can be excited by circuitry having reduced drive or component construction requirements. As shown in FIG. 6, the video signal (in particular the luminance level) is coupled to SVM differentiator and preamplifier 122, which develops the scan modulation signal. The video signal is also coupled to the vertical and horizontal deflection coils 80, 90, to synchronize appropriate vertical and horizontal deflection circuits. Differentiator and preamplifier 122 provides a push-pull output to driver stage 124 of the SVM circuit, which includes a pair of transistors 130, connected to conduct at opposite polarity and biased by series/parallel resistors 126 and capacitors 128. The output of driver 124, coupled between transistors 130, is AC coupled to the SVM coil 100 via capacitor 132.
In an advantageous arrangement, the upper and lower windings 102, 104 of SVM coil 100 are rectangular windings of about six turns, and are simply taped (non-ferromagnetically) to the outer surface of the bobbin 74 at the rear of the deflection yoke liner 72. The bobbin may have an outer diameter, for example of about 4.0 cm, and the upper and lower SVM coil windings can be about 42 mm×25 mm, each wrapped circumferentially part way around the bobbin. Advantageously, the SVM coil windings each occupy more than 90°, and in the illustrated example occupy about 120°, around the circumference of the bobbin, and therefore the tube. The two coil windings in parallel define a resistance of about 0.15 ohm and an inductance of 1.8 microHenries. The coils produce a dynamic sensitivity at the center of the screen of about 1.7 mm deflection per ampere of coil excitation current. It has been determined that good effects in sharpness of transitions in luminance is achieved when the coil is driven to provide a maximum deflection of about 2.2 mm, i.e., at a maximum driving current of about 1.3 amps.
The invention is particularly applicable to a 34 V 16×9 aspect ratio picture tube, and the SVM coil is quite compact along the Z-axis. The SVM coil is disposed on bobbin 74 near the extreme rear of the horizontal deflection yoke. The rear of the yoke is substantially adjacent the static convergence magnet 52. The deflection yoke protrudes rearwardly by a short distance to engage under a clamp for affixing the liner to the tube. To the rear of the liner only about 3 mm distance remains to the edge of the static convergence magnet tape 52, which is about 2.5 cm in width. SVM sensitivity is improved while still maintaining a compact arrangement.
Deflection system for cathode ray tubes:CRT TUBE PHILIPS W76ERF031X044
The present invention relates to a display device comprising a cathode ray index tube (1) having a neck portion (1″) and a screen portion (1). The display device comprises an electron gun assembly (3) for generating a plurality of electron beams (3R,3G,3B), positioned in the neck portion (1″) of the cathode ray index tube (1), a deflection unit (5), placed around the neck portion (1″) of the cathode ray index tube (1), for deflecting said plurality of electron beams (3R,3G,3B), and a convergence unit (6) for converging said plurality of electron beams (3R,3G,3B). The deflection unit (5) is placed at an axial distance from said electron gun assembly (3), closer to said screen portion (1′). The convergence unit (6) is placed in close proximity to the deflection unit (5).


BACKGROUND AND SUMMARY
The present invention relates to a display device comprising a cathode ray index tube and also to a deflection system for use in a cathode ray index tube.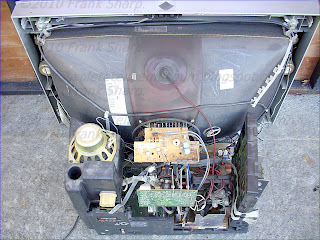
Consequently, cathode ray tubes have also been developed without shadow masks, sometimes referred to as beam indexing CRTs or intelligent tracking CRTs.
In such tubes, known from e.g. U.S. Pat. No. 3,914,641, the different phosphor areas are arranged in groups of strips, normally with a horizontal extension across the screen. The electron beams are deflected to land on the correct strips, commonly by means of a system of electrodes located adjacent and in between the phosphor strips. According to the most commonly used arrangement, two electrodes with elongate finger portions are arranged in such a way that each phosphor strip is located between finger portions belonging to different electrodes. Each electrode is arranged to detect a signal resulting from electron beams landing on the electrode, and the signals from the two electrodes are compared (e.g. subtracted or divided). The relationship between these signals is used to control the beam deflection unit in a feedback position control system.
Basically, there are two different categories of intelligent tracking CRTs, namely:
1) single beam systems, with only one electron gun, alternately illuminating phosphor strips of different colours, and
2) multi-beam systems, where several electron guns are employed, each illuminating one of the phosphor strip groups. The multi-beam systems of course have the advantage of writing red, blue and green information in one sweep.
The present invention is related to the latter category.
U.S. Pat. No. 3,914,641 discloses a multi-beam system having an electron gun assembly is arranged in the neck of a cathode ray tube. The electron gun assembly produces a multiple of, for example three electron beams, each intended to illuminate one of the above-described phosphor strip groups arranged on the inner side of the cathode ray tube screen. In order for each beam to hit the correct phosphor strip, the beams are vertically separated from each other as they hit the screen, i.e. provided with a so-called convergence error, in this case a vertical convergence error, because said strips are horizontally arranged. In order to deflect the beams to the correct spot on the screen, a deflection unit is arranged around the neck of the cathode ray tube, between the electron gun assembly and the screen. To provide said vertical convergence error, a quadrupole (such as a 90-degree quadrupole) is arranged around the neck of the cathode ray tube, close to the electron gun assembly.
A problem with this kind of display is, however, that it is difficult to maintain a constant vertical separation between the electron beams as they hit the screen, after they have been deflected. The reason for this is that the sensitivity of the quadrupole changes as a function of the deflection. This has usually the effect of a degraded picture quality around the edges of the display screen. One way to solve this problem is to operate the quadrupole with a dynamic signal taking the angle of deflection into consideration. This is, however, a somewhat complicated solution, especially since the amplitude of the dynamic signal tends to get large, and consequently there is a need for a simpler and more inexpensive way of attending to this problem.
Thus, it is an object of the present invention to provide a display device that overcomes the above-described problems with the prior-art device.
This and other objects are achieved by a display device comprising a cathode ray index tube having a neck portion and a screen portion, the display device comprising an electron gun assembly for generating a plurality of electron beams, positioned in the neck portion of the cathode ray index tube, a deflection unit, placed around the neck portion of the cathode ray index tube, for deflecting said plurality of electron beams, and a convergence unit for converging said plurality of electron beams, said deflection unit being placed at an axial distance from said electron gun assembly, closer to said screen portion, wherein said convergence unit is placed in close proximity to the deflection unit. Placing the convergence unit close to the deflection unit has the advantage that the uniformity (or effect as a function of the location on the screen) of the vertical beam variations varies with the axial position where the effect is created. The effect is virtually constant near the deflection centre of the deflection unit. Consequently, by placing the deflection unit and the convergence unit close together, a virtually constant vertical convergence error may be achieved. Furthermore, by placing the convergence unit close to the centre of deflection of the deflection field created by the deflection unit, one evades the above-mentioned problem that very large currents are needed, for CRTs with large deflection angles, in order to provide for a constant convergence error on the outskirts of the screen.
In accordance with a preferred embodiment, said convergence unit is placed at essentially the same axial distance from the electron gun assembly as the deflection unit. This embodiment further enhances the system. Moreover, the convergence unit may suitably comprise one or more windings wound around a yoke core in said deflection unit. By winding the windings of the convergence unit around the yoke core of the deflection unit, a very good centring of the deflection and convergence units is achieved. Moreover, a compact construction is obtained. Moreover, said convergence unit may comprise two or more windings wound around separated core parts of a split yoke in said deflection unit. By using two or more separated windings, which may be controlled separately, a very good uniformity can be obtained, resulting in a constant or virtually constant convergence error.
The above-mentioned and other objects are also achieved by a deflection system for use in cathode ray index tubes having a neck portion and a screen portion, the deflection system comprising a deflection unit, intended to be placed around the neck portion of the cathode ray index tube, for deflecting electron beams generated by an electron gun assembly in said index tube, and a convergence unit for converging said plurality of electron beams, wherein said convergence unit is placed in close proximity to the deflection unit. Placing the convergence unit close to the deflection unit has the advantage that the uniformity (or effect as a function of the location on the screen) of the vertical beam variations varies with the axial position where the effect is created. The effect is virtually constant near the deflection centre of the deflection unit. Consequently, by placing the deflection unit and the convergence unit close together, a virtually constant vertical convergence error may be achieved when said unit is used in a cathode ray index tube.
The convergence unit and the deflection unit are preferably positioned in such a way that their respective centre points essentially coincide. In doing so, the above-described effect of the correlation between the sensitivity of the quadrupole and the deflection is minimised. In accordance with a first embodiment of the invention, the convergence unit may comprise one or more windings wound around a yoke core in said deflection unit. By winding the windings of the convergence unit around the yoke core of the deflection unit, a very good centring of the deflection and convergence units is achieved. Moreover, a compact construction is obtained. In accordance with a second embodiment of the invention, said convergence unit may comprise two or more windings wound around separated core parts of a split yoke in said deflection unit. By using two or more separated windings, which may be controlled separately, a very good uniformity can be obtained, resulting in a constant or virtually constant convergence error.
BRIEF DESCRIPTION OF THE DRAWINGS
These and other aspects of the invention are apparent from and will be elucidated with reference to the embodiments described hereinafter.In the drawings,
FIG. 1 is a schematic side view of a display device in accordance with the invention.
FIG. 2 shows a deflection system in accordance with a first embodiment of the invention.
FIG. 3 shows a deflection system in accordance with a second embodiment of the invention.
FIG. 4 shows a deflection system in accordance with a third embodiment of the invention.
DETAILED DESCRIPTION
The colour display device in FIG. 1
The direction of the beams 3 R, 3 G, 3 B and the position of the electron gun assembly 3 are such that the middle electron beam 3 G essentially coincides with the axis of the tube 1 , when the beams are undeflected.
Said screen portion 1 ′ is provided on its inner side with a phosphor layer 2 arranged in horizontal strips (not shown). The electron structure is not relevant to the invention and will therefore not be described in greater detail. In the present case, using a flat index tube, the phosphor layer is constituted by three groups of interspersed horizontal strips, adapted to luminesce in the colours red (R), blue (B) and green (G) respectively, when hit by electron beams 3 R, 3 B and 3 G, respectively. The screen is provided with tracking sensors (not shown) in the form of two comb-shaped electrodes. Each electrode has a number of finger portions, which are arranged in an interdigitated fashion. Each phosphor strip is placed between two finger portions belonging to different electrodes. The electrodes can be formed on the screen by using e.g. lithography. As an example, only one pair of electrodes, covering the entire screen, may be used. However, the electrodes are not of great importance for the invention and will not be further described.
An electromagnetic deflection system 4 is arranged around the neck of the tube 1 , between the electron gun assembly 3 and the screen portion 1 ′ as shown in FIG. 1 . Consequently, the beams that are generated in said electric gun assembly may be deflected by the deflection system 4 on their way to the screen portion, in which they hit a suitable phosphor strip and luminesce in red, green or blue, respectively.
The deflection system 4 comprises a deflection unit 5 for deflecting the three beams in two mutually perpendicular directions, in this case horizontally and vertically, to a respective spot on a corresponding phosphor strip. The deflection unit 5 comprises a number of deflection coils 7 for deflecting the beams 3 R, 3 G, 3 B in known manner. A ring-shaped element 8 , referred to as a yoke ring, is positioned around the deflection coils 7 . The purpose of the yoke ring 8 is to reduce the magnetic flux lines outside the coils 7 . The yoke ring 8 further comprises a first and a second core part 8 ′, 8 ″, the second part 8 ″ being positioned closer to the screen 1 ′ than the first part 8 ′. Together, the two parts 8 ′, 8 ″ form a split yoke ring.
The deflection system also comprises a convergence unit 6 for bending the electron beams in relation to each other, i.e. towards each other or away from each other. The aim of the convergence unit 6 is to provide a constant vertical RB (red and blue, the outermost beams, respectively) convergence error, i.e. a constant vertical separation of the three beams as they hit the screen portion. The convergence unit 6 will hereinafter be described for three different embodiments of the invention. In all other aspects, the embodiments comprise the above-described elements, and these will therefore not be repeated.
According to a first embod

In accordance with a second embodiment of the invention, as shown in FIG. 3, the convergence unit 6 is integrated with the second yoke core part 8 ″ of the deflection unit 5 . In this case, the convergence unit comprises four coils or windings, generally referred to as 10 , wound around the second core part 8 ″, together forming a 90-degree quadrupole. The windings 10 are concentrated at the angles +/−45° and +/−135°, respectively, as shown in FIG. 3 . The windings are arranged to be fed by a DC current in order to generate a magnetic quadrupole field. By precise adjustment of the currents through the quadrupole, thereby adjusting and tuning the magnetic quadrupole field, a good uniformity can be obtained, resulting in a constant or virtually constant RB convergence error.
In accordance with a third embodiment of the invention, as shown in FIG. 4, the convergence unit comprises two parts 11 , 12 , the first 11 of which is integrated with the first yoke core part 8 ′ of the deflection unit 5 as previously described for the first embodiment and the second 12 of which is integrated with the second yoke core part 8 ″ of the deflection unit 5 as previously described for the second embodiment. The respective windings are arranged to be fed by a respective DC current in order to generate a combined magnetic quadrupole field. By precise adjustment of the currents through these two quadrupoles, thereby adjusting and tuning the combined magnetic quadrupole field, a very good uniformity can be obtained, resulting in a constant or virtually constant RB convergence error.
The present invention should not be considered as being limited to the above-described embodiment, but rather includes all possible variations covered by the scope of the appended claims. A person skilled in the art may arrive at alternative embodiments without departing from the scope of the appended claims, particularly if the windings have a plurality of shapes other than those shown in the appended drawings. They may have, for example, a saddle shape. In the present embodiment of the invention, as shown in FIG. 1, the three beams are essentially parallel to each other, as seen from the side, extending from the electron beam assembly 3 to the convergence unit. However, if seen from above, the beams in the present embodiment converge slightly in relation to each other on their way from the electron beam assembly to the defection unit, so that the beams are close to each other in the area of the deflection and convergence units. Moreover, the vertical separation between the beams is small in this area, so that the beams are really close to each other in the area of the deflection centre. After passing through the convergence and deflection units, the beams are diverged slightly from each other under the influence of the convergence unit, in order to provide for the desired convergence error as the beams hit the screen.

The yoke ring may comprise fewer or more parts, some or all of them having convergence coils in accordance with the examples described above. Even if the above-described embodiments show convergence units comprising coils that are wound around the yoke core of the deflection unit, it is possible to create a construction in which the convergence unit is a separate component, placed close to the deflection unit for minimising the deviation from a constant vertical convergence error. For example, the convergence unit may comprise coils wound around a separate ring-shaped element, which is not a part of said deflection yoke.
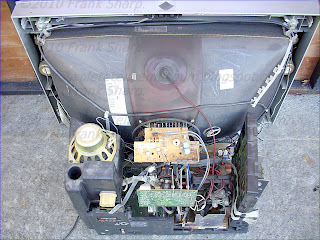
Shadow mask structure for cathode ray tube,CRT TUBE PHILIPS W76ERF031X044.
The present invention relates to a cathode ray tube, and more particularly to a cathode ray tube having a shadow mask for obviating doming phenomenon caused by thermal expansion and deterioration of color purity.
1. A cathode ray tube comprising: a glass panel having a front side; a funnel attached to the glass panel forming a vacuum envelope; a fluorescent screen formed on an inside surface of the glass panel; a shadow mask having a skirt being spaced from the fluorescent screen by a distance, the shadow mask having a short side and a long side; a mask frame coupled to the shadow mask; an electron gun at a neck portion of the funnel; and a deflection yoke for deflecting electron beams emitted from the electron gun in horizontal and vertical directions, wherein a ratio (%) of a length of the skirt (S) to a length of the long side (X) of the shadow mask is in a range of about 4.1%≦S/X≦5.2%, wherein a height of the skirt on the long side of the shadow mask is less than a height of the skirt on the short side of the shadow mask. 2. The cathode ray tube according to claim 1, wherein the mask frame is welded onto the shadow mask and a welding portion of the skirt of the shadow mask for welding the mask frame onto the shadow mask is formed within a distance of 3 mm from an end of the skirt. 3. The cathode ray tube according to claim 3, wherein the shadow mask is welded onto an inside surface of the mask frame. 4. The cathode ray tube according to claim 1, wherein the skirt of the shadow mask includes a slit or an embossment. 5. The cathode ray tube according to claim 1, wherein an inside surface of the panel has a curvature and an outside surface of the panel is substantially flat. 6. The cathode ray tube according to claim 5, wherein an arbitrary point, P (x, y, z) on the outside surface of the panel satisfies a condition of 50,000mm≤(x2+y2)2+z22z≤100,000mm. 7.
The cathode ray tube according to claim 5, wherein a diagonal curvature
radius of the inside surface of the panel is in a range of about 1.5R–4R. 8.
The cathode ray tube according to claim 1, wherein a diagonal curvature
radius of the shadow mask is in a range of about 1.5R–4R. 9. The cathode
ray tube according to claim 1, wherein a thickness of the shadow mask is in a range of about 0.09 mm–0.17 mm. 10. The cathode ray tube according to claim 1, wherein the cathode ray tube is a monitor cathode ray tube. 11. The cathode ray tube according to claim 1, wherein a ratio (%) of a length of the skirt (S) to a length of a short side (Y) of the shadow mask is 5.4%≦S/Y≦6.8%. 12. A cathode ray tube comprising:
a glass panel having a front side; a funnel attached to the glass panel
forming a vacuum envelope; a fluorescent screen formed on an inside
surface of the glass panel; a shadow mask having a skirt being spaced
from the fluorescent screen by a distance, the shadow mask having a
short side and a long side; a mask frame coupled to the shadow mask;
an electron gun at a neck portion of the funnel; and a deflection yoke
for deflecting electron beams emitted from the electron gun in horizontal
and vertical directions, wherein a ratio (%) of a length of the skirt (S)
to a length of the long side (Y) of the shadow mask is in a range of about
5.4%≦S/Y≦6.8%, wherein a height of the skirt on the lone
side of the shadow mask is less than a height of the skirt
on the short side of the shadow mask. 13. The cathode ray
tube according to claim 12, wherein the mask frame is welded
onto the shadow mask and a welding portion of the skirt of the shadow mask for welding the mask frame onto the shadow mask
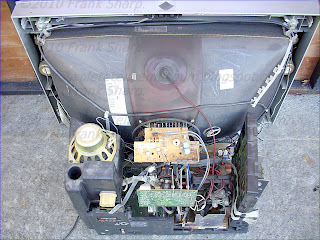
The cathode ray tube according to claim 13, wherein the shadow
mask is welded onto an inside surface of the mask frame. 15.
The cathode ray tube according to claim 12, wherein the skirt of the shadow mask includes a slit or an embossment. 16. The cathode ray tube according to claim 12, wherein an inside surface of the panel has a curvature and an outside surface of the panel is substantially flat. 17. The cathode ray tube according to claim 16, wherein an arbitrary point, P (x, y, z) on the outside surface of the panel satisfies a condition of 50,000mm≤(x2+y2)2+z22z≤100,000mm. 18. The cathode ray tube according to claim 16, wherein a diagonal curvature radius of the inside surface of the panel is in a range of about 1.5R–4R. 19. The cathode ray tube according to claim 12, wherein a diagonal curvature radius of the shadow mask is in a range of about 1.5R–4R. 20. The cathode ray tube according to claim 12, wherein a thickness of the shadow mask is in a range of about 0.09 mm–0.17 mm. 21. The cathode ray tube according to claim 12, wherein the cathode ray tube is a monitor cathode ray tube. 22. A cathode ray tube comprising: a glass panel having a front side; a funnel attached to the glass panel forming a vacuum envelope; a fluorescent screen formed on an inside surface of the glass panel; a shadow mask with a color selection function and having a skirt with a welding portion, the shadow mask being spaced from the fluorescent screen by a distance and having a short side and a long side, wherein a height of the skirt on the long side of the shadow mask is less than a height of the skirt on the short side of the shadow mask; a mask frame in the shadow mask, wherein the mask frame is welded to the shadow mask and the welding portion of the skirt of the shadow mask for welding the mask frame to the shadow mask is formed within a distance of 3 mm from an end of the skirt; an electron gun at a neck portion of the funnel; and a deflection yoke for deflecting electron beams emitted from the electron gun in horizontal and vertical directions, wherein a ratio (%) of a length of the skirt (S) to a length of the long side (X) of the shadow mask is 4.1%≦S/X≦5.2%; wherein a ratio (%) of the length of a skirt (S) to a length of the short side (Y) of the shadow mask is 5.4%≦S/Y≦6.8%. 23. A cathode ray tube comprising: a glass panel having a front side; a funnel attached to the glass panel forming a vacuum envelope; a fluorescent screen formed on an inside surface of the glass panel; a shadow mask having a skirt being spaced from the fluorescent screen by a distance, the shadow mask having a short side and a long side; a mask frame coupled to the shadow mask; an electron gun at a neck portion of the funnel; and means for deflecting electron beams emitted from the electron gun in horizontal and vertical directions, wherein a ratio (%) of a length of the skirt (S) to a length of the long side (X) of the shadow mask is in a range of about 4.1%≦S/X≦5.2%, wherein a height of the skirt on the long side of the shadow mask is less than a height of the skirt on the short side of the shadow mask. 24. A cathode ray tube comprising: a glass panel having a front side; a funnel attached to the glass panel forming a vacuum envelope; a fluorescent screen formed on an inside surface of the glass panel; a shadow mask having a skirt being spaced from the fluorescent screen by a distance, the shadow mask having a short side and a long side; a mask frame coupled to the shadow mask; an electron gun at a neck portion of the funnel; and means for deflecting electron beams emitted from the electron gun in horizontal and vertical directions, wherein a ratio (%) of a length of the skirt (S) to a length of the long side (Y) of the shadow mask is in a range of about 5.4%≦S/Y≦6.8%, wherein a height of the skirt on the long side of the shadow mask is less than a height of the skirt on the short side of the shadow mask.
Description:
BACKGROUND OF THE INVENTION
1. Field of the InventionThe present invention relates to a cathode ray tube, and more particularly, to a cathode ray tube having a shadow mask for obviating doming phenomenon caused by thermal expansion and deterioration of color purity.
2. Discussion of the Related Art
FIG. 1 illustrates the structure of a color cathode ray tube according to a related art.
Referrin

A fluorescent screen 4 is formed on the inside surface of the panel 1 , and an electron gun 8 is mounted on a neck portion 10 of the funnel 2 opposite of the fluorescent screen 4 . A shadow mask 3 with a color selecting function is situated between the fluorescent screen 4 and the electron gun 8 , maintaining a predetermined distance from the fluorescent screen 7 . The shadow mask 3 is supported by a mask frame 14 . Also, the mask frame 14 is elastically supported by a mask spring 5 and connected to a stud pin 6 to be supported by the panel 1 .
The mask frame 14 is joined with an inner shield 7 made of a magnetic material. The inner shield 7 reduces the movement of an electron beam 11 due to external magnetic field during operation of the cathode ray tube. A deflection yoke 9 for deflecting the electron beam 11 emitted from the electron gun 8 is mounted into the neck portion 10 of the funnel 2 . Also, a reinforcing band 12 is included in order to reinforce the front surface glass under the influence of the vacuum state inside the tube.
In operation, the electron beam 11 emitted from the electron gun 8 is deflected vertically and horizontally by the deflection yoke 9 , and the deflected electron beam 11 passes through a beam passing hole on the shadow mask 3 and strikes the fluorescent screen 4 on the front, consequently displaying a desired color image.
FIG. 2 illustrates a shadow mask before it undergoes a press-forming process, and FIG. 3 illustrates the shadow m

Referring to FIGS. 2 and 3, a skirt 15 of the shadow mask 3 (before it undergoes the press-forming process) includes a slit 17 and a guide slit 18 . The slit 17 serves to prevent the skirt 15 fro

After the shadow mask 3 is press-formed, the skirt 15 is bent at right angles to a portion where beam passing holes are formed, and an embossment 16 is formed in order to promote formation of the skirt 15 and reinforce the strength of the skirt 15 .
Then, the shadow mask 3 is fitted in the cathode ray tube by welding a welding portion 19 of the skirt 15 and the mask frame 14 together.
FIG. 4 is a schematic view illustrating a doming phenomenon in which the shadow mask 3 undergoes a deform

FIG. 5 is a schematic view illustrating the thermal deformation of the mask frame and the shifting of the shadow mask position, eventually causing the electron beams to mis-land. The increased temperature (heat) of the shadow mask 3 through energy from the electron beams 11 is transferred to the mask frame 14 , causing the mask frame 14 to thermally expand. This thermally expanded mask frame 14 then causes the shadow mask 3 to be displaced in the opposite direction of the original thermal displacement direction.
FIG. 6 is a diagra

When the electron beams mis-land, color purity of the cathode ray tube deteriorates and it becomes difficult to correct the electron beams' landing problem.
To obviate this problem, a bimetal mask spring was used to compensate for thermal deformation of the mask frame, but this was not sufficient to solve the problem completely. Instead, the highly expensive mask spring only increased manufacturing cost of the cathode ray tube.
SUMMARY OF THE INVENTION
Accordingly, the present invention is directed to a cathode ray tube that substantially obviates one or more of the problems due to limitations and disadvantages of the related art.An advantage of the present invention is to provide a cathode ray tube with a shadow mask capable of suppressing a doming phenomenon caused by thermal deformation and obviating deterioration of color purity.
Additional features and advantages of the invention will be set forth in the description which follows, and in part will be apparent from the description, or may be learned by practice of the invention. The objectives and other advantages of the invention will be realized and attained by the structure particularly pointed out in the written description and claims hereof as well as the appended drawings.
To achieve these and other advantages and in accordance with the purpose of the present invention, as embodied and broadly described, the preferred embodiment of the present invention provides a cathode ray tube including: a front side (or face) glass panel; a funnel welded into the panel forming a vacuum envelope; a fluorescent screen formed on an inside surface of the panel; a shadow mask with a color selection function being spaced out from the fluorescent screen by a predetermined distance, wherein a ratio (%) of a length of a skirt (S) to a length of a long side (X) of the shadow mask preferably satisfies a condition of 4.1%≦S/X≦5.2%; a mask frame welded into the shadow mask; an electron gun fitted in a neck portion of the funnel; and a deflection yoke for deflecting electron beams emitted from the electron gun in horizontal and vertical directions.
In another aspect, the preferred embodiment of the present invention is to provide a cathode ray tube including: a front side (or face) glass panel; a funnel welded into the panel forming a vacuum envelope; a fluorescent screen formed on an inside surface of the panel; a shadow mask with a color selection function being spaced out from the fluorescent screen by a predetermined distance, wherein a ratio (%) of a length of a skirt (S) to a length of a short side (Y) of the shadow mask preferably satisfies a condition of 5.4%≦S/Y≦6.8%; a mask frame welded into the shadow mask; an electron gun fitted in a neck portion of the funnel; and a deflection yoke for deflecting electron beams emitted from the electron gun in horizontal and vertical directions.
It is to be understood that both the foregoing general description and the following detailed description are exemplary and explanatory and are intended to provide further explanation of the invention as claimed.
BRIEF DESCRIPTION OF THE DRAWINGS
The accompanying drawings, which are included to provide a further understanding of the invention and are incorporated in and constitute a part of this specification, illustrate embodiments of the invention and together with the description serve to explain the principles of the invention.In the drawings:
FIG. 1 illustrates the structure of a color cathode ray tube according to a related art;
FIG. 2 is a schematic view illustrating a shadow mask before it undergoes a press-forming process;
FIG. 3 is a schematic view illustrating the shadow mask illustrated in FIG. 2 after it undergoes a press-forming process;
FIG. 4 is a schematic view illustrating a doming phenomenon in which the shadow mask illustrated in FIG. 3 undergoes a deformation due to thermal expansion and electron beams mis-land;
FIG. 5 is a schematic view illustrating the thermal deformation of the mask frame and the shifting of the shadow mask position, eventually causing the electron beams to be mis-landed;
FIG. 6 is a diagram illustrating the mis-landing degree of the electron beams due to the thermal deformation of the shadow mask and the mask frame;
FIG. 7 is a schematic view illustrating a panel having a substantially flat outside surface and a curved inside surface;
FIG. 8 is a schematic view illustrating lengths of the long side and the short side of a shadow mask for a cathode ray tube according to the present invention;
FIG. 9 is a schematic view illustrating a length of a skirt of the shadow mask for the cathode ray tube according to the present invention;
FIG. 10 is a schematic view comparing the shadow mask of the related art to the shadow mask of the present invention where the position of the shadow mask of the present invention is changed because of a deformed mask frame that is welded into a welding portion of the skirt;
FIG. 11 is a schematic view illustrating the shadow mask for the cathode ray tube according to the present invention and showing the length of the skirt and the displacement of the shadow mask, which are inversely proportional to each other, that is, as the length of the skirt increases, the shadow mask moves little; and
FIG. 12 is a diagram comparing the mis-landing degree of the electron beams on the shadow masks of the present invention and the related art.
DETAILED DESCRIPTION OF ILLUSTRATED EMBODIMENTS
Reference will now be made in detail to an embodiment of the present invention, example of which is illustrated in the accompanying drawings.The present invention is directed to obviating a doming phenomenon and deterioration of color purity by changing the length of a

Also, a diagonal curvature radius of the inside surface of the panel is beneficially in the range o
In general, the diagonal curvature radius of the inside surface of the panel has a great impact on the sense of flatness of the screen, the uniformity of brightness, contrast, and strength of the shadow mask. With the diagonal curvature radius limited to 1.5R–4R, it is possible to prevent the diagonal portion of the screen from being too thick without losing the above features, i.e. maintaining the sense of flatness of the screen, the uniformity of brightness and contrast, and securing the mechanical strength of the shadow mask.
Considering that the shadow mask is usually formed to completely cover the inside surface curvature radius of the panel, a diagonal curvature radius of an inside surface of the shadow mask is preferably in the range of 1.5R–4R also. Here, 1R=1.767×a diagonal length of an effective surface. That is, 1R equals to 1.767 times a diagonal length of an effective surface of the screen.
FIG. 8 is a schematic view illustrating lengths of the long side and the short side of the shadow mask for a cathode ray tube according to the present invention. FIG. 9 is a schematic view illustrating the length of the skirt of the shadow mask for the cathode ray tube according to the present invention. Referring to FIGS. 8 and 9, the shadow mask having a large number of electron beam passing holes is in a recta

The shadow mask 3 fits into the cathode ray tube by welding a welding portion 19 of the skirt 15 onto the inside surface of the mask frame 14 . In some cases, the welding portion 19 of the skirt 15 is welded onto an outside surface of the mask frame 14 . The former method, i.e. welding the inside surface of the mask frame 14 onto the welding portion 19 of the skirt 15 , is better in terms of preventing a doming phenomenon and securing thermal stability of the shadow mask.
The present inv

FIG. 10 is a schematic view comparing the shadow mask of the related art to the shadow mask of the present invention where the position of the shadow mask of the present invention is changed because of a deformed mask frame that is welded into the welding portion of the skirt. FIG. 11 is a schematic view illustrating the shadow mask for the cathode ray tube according to the present invention and showing the length of the skirt and the displacement of the shadow mask being inversely proportional to each other, that is, as the length of the skirt increases, the shadow mask moves little.
As shown in FIG. 10 and FIG. 11, the skirt 15 of the shadow mask 3 for the cathode ray tube according to the present invention is longer than the skirt 15 of the conventional shadow mask 3 , and the welding portion 19 of the skirt 15 is also disposed relatively lower. Ther

Referring back to FIG. 8, S denotes the length of the skirt 15 of the shadow mask 3 and X denotes the length of the long side of the shadow mask 3 . Then the ratio (%) of the length of the skirt (S) to the length of the long side (X) beneficially satisfies a condition of 4.1%≦S/X≦5.2%.
To obviate any inconvenience of welding and possible degradation of welding, the skirt portion 19 may be at least 2 mm distant from the end of the skirt 15 . In considerations of the height of the welding portion 19 , an interference with the mask frame 14 , and tolerance of welding, the ratio (%) of the length of the skirt (S) to the length of the long side (X) should be not larger than 5.2% and not smaller than 4.1%.
Similarly, in consideration of the height of the welding portion 19 , an interference with the mask frame 14 , and tolerance of welding, the ratio (%) of the length of the skirt (S) to the length of the short side (Y) should be not larger than 6.8% and not smaller than 5.4%. That is, the ratio (%) of the length of the skirt (S) to the length of the short side (Y) beneficially satisfies a condition of 5.4%≦S/Y≦6.8%.
Suppose that the skirt length on the long side of the shadow mask is XS, and the skirt length on the short side of the shadow mask is YS. Then, the skirt length on the long side and the skirt length on the short side beneficially satisfy a relation of (XS)≦(YS). Usually, the short side of the shadow mask is more susceptible to the doming phenomenon. Hence, the skirt length on the short side (YS) is made to be relatively longer than the skirt length on the long side (XS) to reduce the doming phenomenon. Accordingly, the two skirt lengths satisfy the condition of (XS)≦(YS).
Table 1 below explains changes in a doming degree of the shadow mask for the cathode ray tube according to the present invention.
TABLE 1 | ||||||
Peak value- | ||||||
Peak | Base | |||||
X | Y | S | value | Best value | value | |
Related art | 362 mm | 277 mm | 14 mm | 5 μm | −13 μm | 18 μm |
Present | 364 mm | 278 mm | 17 mm | 5 μm | −8 μm | 13 μm |
Invention | ||||||
FIG. 12 is a diagram comparing the mis-landing degree of the electron beams on the shadow masks

The shadow mask which prevents the doming phenomenon and deterioration of overall color purity according to the present invention can be adopted to TV cathode ray tubes as well as monitor cathode ray tubes.
By making the skirt length of the shadow mask longer than the related art and applying the shadow mask to the cathode ray tube according to the present invention, it is now possible to obviate problems with the doming phenomenon and deterioration of color purity.
It will be apparent to those skilled in the art that various modifications and variation can be made in the present invention without departing from the spirit or scope of the invention. Thus, it is intended that the present invention cover the modifications and variations of this invention provided they come within the scope of the appended claims and their equivalents.
No comments:
Post a Comment
The most important thing to remember about the Comment Rules is this:
The determination of whether any comment is in compliance is at the sole discretion of this blog’s owner.
Comments on this blog may be blocked or deleted at any time.
Fair people are getting fair reply. Spam and useless crap and filthy comments / scrapers / observations goes all directly to My Private HELL without even appearing in public !!!
The fact that a comment is permitted in no way constitutes an endorsement of any view expressed, fact alleged, or link provided in that comment by the administrator of this site.
This means that there may be a delay between the submission and the eventual appearance of your comment.
Requiring blog comments to obey well-defined rules does not infringe on the free speech of commenters.
Resisting the tide of post-modernity may be difficult, but I will attempt it anyway.
Your choice.........Live or DIE.
That indeed is where your liberty lies.
Note: Only a member of this blog may post a comment.