




This is one of the PANASONIC DIGITAL CHASSIS versions Implementing DIGITAL SIGNAL PROCESSING and basing it on the ITT DIGIVISION DIGIT3000 family chipset.
It's a successor of EURO 2 L and a full successor of the PANASONIC EURO 1 DIGITAL CHASSIS
CIRCUITS DESCRIPTIONS:


CCU 3000, CCU 3000-I
CCU 3001, CCU 3001-I
MICRONAS INTERMETALL 4
1. Introduction
The CCU 3000, CCU 3000-I, CCU 3001, CCU 3001-I
are integrated circuits designed in 1.2 mm CMOS
technology, with the exception of CCU 3000, TC18 and
TC19, which is designed in 1 mm CMOS technology. The
CPU contained on the chips is a functionally unchanged
65C02-core, which means that for program development,
systems can be used which are on the market; including
high level language c

The pin numbers mentioned in this data sheet refer to
the 68-pin PLCC package unless otherwise designated.
The CCU 3000-I is described separately in an addendum
on page 66.
1.1. Features of the CCU 3000, CCU 3000-I,
CCU 3001, CCU 3001-I
– CCU 3000 = ROM-less version of the CCU 3001
– 65C02 CPU with max. 8 MHz clock
– 32 kByte internal ROM (CCU 3001 only)
– 1344 internal Bytes RAM with stand-by option
– 51 I/O lines (CCU 3001)
– 26 I/O lines (CCU 3000)
– clock generator with programmable clock frequency
– 8 level interrupt controller
– CCU 3000, CCU 3001:
2 Multimaster IM bus interfaces
– CCU 3000-I, CCU 3001-I: 1I2C/IM bus and
1 Multimaster IM bus interface (see addendum)
– IR-input for software-decoded IR-systems
– on-chip power on, stand-by and clock supervision
logic
– on-chip watchdog
– 3 multifunctional timers
– supports memory banking (external 2MBytes)
– power down signal for external memory
– mask option: EMU mode
– programs can be written in Assembler or in “C”
– CCU 3000 TC 18/19: 1.0 mm CMOS technology, (see
addendum)
– application software available.
Functional Description
2.1. ROM
The chip is equipped with 32 kByte mask-programmable
ROM. The ROM uses up the address space from 8000H
to FFFFH. This ROM can be supplemented or replaced
externally. Only the CCU 3001 has an internal ROM.
2.2. RAM
The RAM

– page 0 (address 0 to FFH)
– page 1 (address 100H to 1FFH)
– page 3, 4, 5, 6 (address 300H to 63FH)
Page 0 offers a particularly fast access to the 65C02 and
is therefore very valuable for fast, compact programs.
Page 1 contains the stack and must therefore also have
RAM. The remaining RAM-memory follows in pages 3,
4, 5, 6, as page 2 is reserved as I/O address space. The
RAM can be kept in the stand-by mode via stand-by pin.
2.3. CPU
The CPU core is fully compatible with the 65C02 microprocessor.
However, not all the pins of the 65C02 processor
are accessible for the user outside the chip. One
switch in the control register allows the CPU to be
switched off, so that an external processor can take over
its tasks. This external processor can of course also be
an in-circuit emulator, which makes near-hardware
emulation possible, even though the status and control
lines of the internal CPU are not accessible. If an external
processor is used, all hardware blocks of the chip are
as accessible to it as if it were the internal CPU.
2.4. Clock Generator
An integrated two-pin oscillator generates the clock for
the microcontroller. The frequency created by the oscillator
can be programmed to be reduced with a divider
by the factor 1 ... 255. This enables the user to decrease
the current consumption by the controller by reducing
the working frequency as well as to increase the access
time for the (slower) external memory. This divider contains
the value 4 after a reset, so that the system can also
start with a slow external memory. If the mask-option
OSC is set (EMU version), a switch in the control register
makes it possible to recei

XTAL2. In this case the oscillator must be external and
the clock must be fed to the pin XTAL1. In this way, the
user gets a time reference for internal operations in the
microcomputer. This is especially important with the interrupt
controller. The production version of the CCU
does not have this function!
2.5. PORT 1 to PORT 3, PORT 6 to PORT 8
8 ports belong to the system, of which 5 are 8 bits wide,
one 6 bit, one 4 bit and one 1 bit wide. All port lines of
PORTS 1 to 3 and 6 to 8 can be used as inputs or outputs
independently from each other. One register per port
defines the direction. PORT1 to PORT3 have push-pull
outputs and PORT6 to PORT8 have open drain outputs.
Even a line defined as output can be read, the pin level
being important. This property makes it possible for the
software to find desired and undesired short circuits.
Each port reserves a byte for the direction register and
the data in the I/O page. If the corresponding bit in the
direction register is set to 0, the output mode is switched
on. After a reset, all bits of a direction register are set
to 1. The falling edge of bit 7 of PORT 8 generates interrupts
if the priority of the corresponding interrupt controller
source (7) is not set to 0.
2.6. PORT 4
PORT 4 consists of only one line (LSB, P40). After a reset,
PORT 4 operates as an input only. As soon as PORT
4 is written for the first time, it is switched to output mode
(push-pull). Later read accesses read the actual level at
port 4. If bit 3 in the control word is active, P4 is used as
an R/W-line. If the internal CPU is active, R/W is an output
line, otherwise it is an input. But P4 has another, very
important function during RESET. The level at P4 during
RESET decides whether the control word is read from
the internal ROM (FFF9H) or from the external memory.
It is therefore important that the desired level during RESET
is set at P4. An internal pull-down resistor of approx.
100 kW

that the control word is read by the internal ROM. The
external control word access is obtained via an external
pull-up resistor of approx. 5 kW. The CCU 3000 has an
internal pull-up resistor at P4 (external ROM access).
The further mode of operation of the CCU 3000, CCU
3001 depends only on the control word though.
Please note that this mode is always necessary for
the CCU 3000 since this device does not have internal
ROM!
2.7. I/O-Lines P50 to P55
The 6 additional I/O-lines have a two-fold function:
– input or output line (open drain output) or
– fully decoded I/O-select lines (push-pull outputs)
As a rule these lines can be used as input or output lines.
As soon as ports 1 to 4 are used as system bus, they are
lost as I/O-channels. However, a total of 48 port lines (24
inputs and outputs each) can be reconstructed without
difficulties (1 housing for 8 lines), if the additional 6 I/Olines
of the CCU 3000, CCU 3001 are switched into the
port select mode. They then represent the select lines of
the original ports 1 to 3. Each line can be defined as I/O
or port select line separately. In the I/O-page three bytes
are needed.
ITT VDP3108 Single-Chip Video Processor
Preamble:
The ITT VDP3108 Is the evolution of the DIGIT2000 chipset.

1. Introduction
The entire video processing and controlling for a color
TV has been developed on a single chip in 0.8m CMOS
technology. Modular design and submicron technology
allow the economic integration of features in all classes
of TV sets.
Open architecture is the key word to the new DSP generation.
Flexible standard building blocks have been defined
that offer continuity and transparency of the entire
system.
One IC contains the entire video and deflection processing
and builds the heart of a modern color TV. Its performance
and complexity allow the user to standardize
his product development. Hardware and software applications
can profit from the modularity as well as manufacturing,
system support or maintenance. The main
features are:
– low cost, high performance
– all digital video processing
– multi-standard color decoder PAL/NTSC/SECAM
– 3 composite, 1 S–VHS input
– integrated high-quality AD/DA converters
– sync and deflection processing
– luminance and chrominance features, e.g.
peaking, color transient improvement
– programmable RGB matrix
– various digital interfaces
– embedded RISC controller (80 MIPS)
– single power supply 5 V
– 0.8m CMOS Technology
– 68-pin PLCC or 64-pin Shrink DIL Package
1.1. System Architecture
Two main modules have been defined:
Video Processor and
Display Processor.
They are designed as silicon building blocks. Their partitioning
permits a variety of IC configurations with the aim
to satisfy the particular requirements of different applications.
Both, analog and digital interfaces, support
state of the art TV receivers as well as other environments.
Fig. 1–1 shows the block diagram of the singlechip
Video Processor which consists of both modules.

2. Functional Description
2.1. Analog Front End
This block provides the analog interfaces to all video inputs
and mainly carries out analog-to digital conversion
for the following digital video processing. A block diagram
is given in figure 2–1.
Most of the functional blocks in the front end are digitally
controlled (clamping, AGC and clock-DCO). The control
loops are closed by the Fast Processor (‘FP’) embedded
in the decoder.
2.1.1. Input Selector
Up to four analog inputs can be connected. Three inputs
are for input of composite video or S–VHS luma signal.
These inputs are clamped to the sync back porch and
are amplified by a variable gain amplifier. One input is
for connection of S–VHS carrier–chrominance signal.
This input is internally biased and has a fixed gain amplifier.
2.1.2. Clamping
The composite video input signals are AC coupled to the
IC. The clamping voltage is stored on the coupling capacitors
and is generated by digitally controlled current
sources. The clamping level is the back porch of the video
signal. S-VHS chroma is also AC coupled. The input
pin is internally bias
range.
2.1.3. Automatic Gain Control
A digitally working automatic gain control adjusts the
magnitude of the selected baseband by +6/–4.5 dB in 64
logarithmic steps to the optimal range of the ADC .
The gain of the video input stage including the ADC is
213 steps/V for all three standards (PAL/NTSC/SECAM/
Y/C), with the AGC set to 0 dB.
2.1.4. Analog-to-Digital Converters
Two ADCs are provided to digitize the input signals.
Each converter runs with 20.25 MHz and has 8 bit resolution.
An integrated bandgap circuit generates the required
reference voltages for the converters.
The two ADCs are of a 2-stage subranging type.
---------------------------------------------------------------------------
TOGHETHER WITH VIDEO PROCESSING THERE IS SOUND PROCESSING WITH MSP3400C

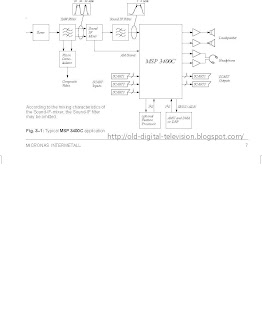
Multistandard Sound Processor
Release Notes: The hardware description in this
document is valid for the MSP 3400C – C8 and newer
codes. Revision bars indicate significant changes
to the previous version.
1. Introduction
The MSP 3400C is designed as single-chip Multistandard
Sound Processor for applications in analog and
digital TV sets, satellite receivers and video recorders.
The MSP-family, which is based on the MSP 2400, demonstrates
the progressive development towards highly
integrated multi-functional ICs.
The MSP 3400C, again, improves function integration:
The full TV sound processing, starting with analog
sound IF signal-in, down to processed analog AF-out, is
performed in a single chip. The IC is produced in 0.8 mm
CMOS technology, combined with high performance
digital signal processing.
The MSP 3400C 0.8 m CMOS version is fully pin and
3410. The main difference between the MSP 3400C and
the MSP 3410, consists of the MSP 3410 being able to
decode NICAM signals.
2. Features of the MSP 3400C:
2.1. Features of the Demodulator and Decoder
Sections
The MSP 3400C is designed to perform demodulation
of FM-mono TV sound and two carrier FM systems according
to the German or Korean terrestrial specs. With
certain constraints, it is also possible to do AM-demodulation
according to the SECAM system. Alternatively, the
satellite specs can be processed with the MSP 3400C.
For FM carrier detection in satellite operation, the AMdemodulation
offers a powerful feature to calculate the
carrier field strength, which can be used for automatic
search algorithms. So, the IC facilitates a first step towards
multistandard capability with its very flexible
application and may be used in TV-sets, satellite tuners,
and video recorders.
The MSP 3400C facilitates profitable multistandard capability,
offering the following advantages:
– two selectable analog inputs (TV and SAT-IF sources)
– Automatic Gain Control (AGC) for analog input: input
range: 0.14 – 3 Vpp
– integrated A/D converter for sound-IF inputs
– all demodulation and filtering is performed on chip and
is individually programmable
– no external filter hardware is required
– only one crystal clock (18.432 MHz) is necessary
– FM carrier level calculation for automatic search algorithms
and carrier mute function
– high deviation FM-mono mode (max. deviation:
approx. 360 kHz)
2.2. Features of the DSP-Section
– flexible selection of audio sources to be processed
– digital input and output interfaces via I2S-Bus for external
DSP-processors, surround sound, ADR etc.
– digital interface to process ADR (Astra Digital Radio)
together with DRP 3510 A
– performance of all deemphasis systems including
adaptive Wegener Panda 1 without external components
or controlling
– digitally performed FM-identification decoding and dematrixing
– digital baseband processing: volume, bass, treble,
5-band equalizer, loudness, pseudostereo, and basewidth
enlargement
– simple controlling of volume, bass, treble, equalizer
etc.
– increased audio bandwidth for FM-Audio-signals
(20 Hz – 15 kHz, 1 dB)
2.3. Features of the Analog Section
– three selectable analog pairs of audio baseband inputs
(= three SCART inputs)
input level: 32 V RMS,
input impedance: .25 kW
– one selectable analog mono input (i.e. AM sound),
input level: 32 V RMS,
input impedance: .10 kW
– two high quality A/D converters, S/N-Ratio: .85 dB
– 20 Hz to 20 kHz Bandwidth for SCART-to-SCARTCopy
facilities
– MAIN (loudspeaker) and AUX (headphones): two
pairs of 4-fold oversampled D/A-converters
output level per channel: max. 1.4 V RMS
output resistance: max. 5 kW
S/N-Ratio: .85 dB at maximum volume
max. noise voltage in mute mode: 310 mV (BW: 20 Hz
...16 kHz)
– one pair of four-fold oversampled D/A-converters supplying
two selectable pairs of SCART-Outputs. Output
level per channel: max. 2 V RMS, output resistance:
max. 0.5 kW, S/N-Ratio: .85 dB
(20 Hz...16 kHz).

TOGHETHER WITH VIDEO PROCESSING THERE IS SOUND PROCESSING WITH MSP3400C
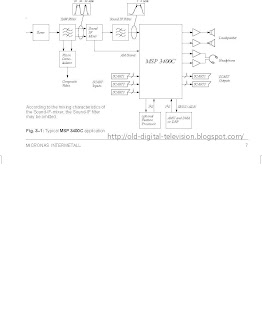
Multistandard Sound Processor
Release Notes: The hardware description in this
document is valid for the MSP 3400C – C8 and newer
codes. Revision bars indicate significant changes
to the previous version.
1. Introduction
The MSP 3400C is designed as single-chip Multistandard
Sound Processor for applications in analog and
digital TV sets, satellite receivers and video recorders.
The MSP-family, which is based on the MSP 2400, demonstrates
the progressive development towards highly
integrated multi-functional ICs.
The MSP 3400C, again, improves function integration:
The full TV sound processing, starting with analog
sound IF signal-in, down to processed analog AF-out, is
performed in a single chip. The IC is produced in 0.8 mm
CMOS technology, combined with high performance
digital signal processing.
The MSP 3400C 0.8 m CMOS version is fully pin and
software compatible to the 1.0 m MSP 3400 and MSP
3410. The main difference between the MSP 3400C and
the MSP 3410, consists of the MSP 3410 being able to
decode NICAM signals.
2. Features of the MSP 3400C:
2.1. Features of the Demodulator and Decoder
Sections
The MSP 3400C is designed to perform demodulation
of FM-mono TV sound and two carrier FM systems according
certain constraints, it is also possible to do AM-demodulation
according to the SECAM system. Alternatively, the
satellite specs can be processed with the MSP 3400C.
For FM carrier detection in satellite operation, the AMdemodulation
offers a powerful feature to calculate the
carrier field strength, which can be used for automatic
search algorithms. So, the IC facilitates a first step towards
multistandard capability with its very flexible
application and may be used in TV-sets, satellite tuners,
and video recorders.
The MSP 3400C facilitates profitable multistandard capability,
offering the following advantages:
– two selectable analog inputs (TV and SAT-IF sources)
– Automatic Gain Control (AGC) for analog input: input
range: 0.14 – 3 Vpp
– integrated A/D converter for sound-IF inputs
– all demodulation and filtering is performed on chip and
is individually programmable
– no external filter hardware is required
– only one crystal clock (18.432 MHz) is necessary
– FM carrier level calculation for automatic search algorithms
and carrier mute function
– high deviation FM-mono mode (max. deviation:
approx. 360 kHz)
2.2. Features of the DSP-Section
– flexible selection of audio sources to be processed
– digital input and output interfaces via I2S-Bus for external
DSP-processors, surround sound, ADR etc.
– digital interface to process ADR (Astra Digital Radio)
together with DRP 3510 A
– performance of all deemphasis systems including
adaptive Wegener Panda 1 without external components
or controlling
– digitally performed FM-identification decoding and dematrixing
– digital baseband processing: volume, bass, treble,
5-band equalizer, loudness, pseudostereo, and basewidth
enlargement
– simple controlling of volume, bass, treble, equalizer
etc.
– increased audio bandwidth for FM-Audio-signals
(20 Hz – 15 kHz, 1 dB)
2.3. Features of the Analog Section
– three selectable analog pairs of audio baseband inputs
(= three SCART inputs)
input level: 32 V RMS,
input impedance: .25 kW
– one selectable analog mono input (i.e. AM sound),
input level: 32 V RMS,
input impedance: .10 kW
– two high quality A/D converters, S/N-Ratio: .85 dB
– 20 Hz to 20 kHz Bandwidth for SCART-to-SCARTCopy
facilities
– MAIN (loudspeaker) and AUX (headphones): two
pairs of 4-fold oversampled D/A-converters
output level per channel: max. 1.4 V RMS
output resistance: max. 5 kW
S/N-Ratio: .85 dB at maximum volume
max. noise voltage in mute mode: 310 mV (BW: 20 Hz
...16 kHz)
– one pair of four-fold oversampled D/A-converters supplying
two selectable pairs of SCART-Outputs. Output
level per channel: max. 2 V RMS, output resistance:
max. 0.5 kW, S/N-Ratio: .85 dB
(20 Hz...16 kHz).
PANASONIC TX-28XD3C QUINTRIX CHASSIS EURO-2M CHASSIS SMPS POWER Supply is based on TDA4600 (SIEMENS).
PANASONIC TX-28XD3C QUINTRIX CHASSIS EURO-2M Power supply Description based on TDA4601d (SIEMENS)

TDA4601 Operation. * The TDA4601 device is a single in line, 9 pin chip. Its predecessor was the TDA4600 device, the TDA4601 however has improved switching, better protection and cooler running. The (SIEMENS) TDA4601 power supply is a fairly standard parallel chopper switch mode type, which operates on the same basic principle as a line output stage. It is turned on and off by a square wave drive pulse, when switched on energy is stored in the chopper transformer primary winding in the form of a magnetic flux; when the chopper is turned off the magnetic flux collapses, causing a large back emf to be produced. At the secondary side of the chopper transformer this is rectified and smoothed for H.T. supply purposes. The advantage of this type of supply is that the high chopping frequency (20 to 70 KHz according to load) allows the use of relatively small H.T. smoothing capacitors making smoothing easier. Also should the chopper device go short circuit there is no H.T. output. In order to start up the TDA4601 I.C. an initial supply of 9v is required at pin 9, this voltage is sourced via R818 and D805 from the AC side of the bridge rectifier D801, also pin 5 requires a +Ve bias for the internal logic block. (On some sets pin 5 is used for standby switching). Once the power supply is up and running, the voltage on pin 9 is increased to 16v and maintained at this level by D807 and C820 acting as a half wave rectifier and smoothing circuit. PIN DESCRIPTIONS Pin 1 This is a 4v reference produced within the I.C. Pin 2 This pin detects the exact point at which energy stored in the chopper transformer collapses to zero via R824 and R825, and allows Q1 to deliver drive volts to the chopper transistor. It also opens the switch at pin 4 allowing the external capacitor C813 to charge from its external feed resistor R810. Pin 3 H.T. control/feedback via photo coupler D830. The voltage at this pin controls the on time of the chopper transistor and hence the output voltage. Normally it runs at Approximately 2v and regulates H.T. by sensing a proportion of the +4v reference at pin 1, offset by conduction of the photo coupler D830 which acts like a variable resistor. An increase in the conduction of transistor D830 and therefor a reduction of its resistance will cause a corresponding reduction of the positive voltage at Pin 3. A decrease in this voltage will result in a shorter on time for the chopper transistor and therefor a lowering of the output voltage and vice versa, oscillation frequency also varies according to load, the

Description:
In the blocking converter described in the aforementioned reference in the literature, "Funkschau" (1975), No. 5, Pages 40 to 44, the power switching transistor is connected in the manner defined in the introduction to this application. In addition, a so-called starting circuit is provided. Because several diodes are generally provided in the overall circuit of a blocking oscillator according to the definition provided in the introduction hereto, it is necessary, in order not to damage these diodes, that due to the collector peak current in the case of a short circuit, no excessive stress of these diodes and possibly existing further sensitive circuit parts can occur.
It is accordingly an object of the invention to provide another starting circuit. It is a further object of the invention to provide a possible circuit for the control circuit which is particularly well suited for this purpose. It is yet another object of the invention to provide such a power supply which is assured of operation over the entire range of line voltages from 90 to 270 V a-c, while the secondary voltages and secondary load variations between no-load and short circuit are largely constant.

In accordance with a further feature of the invention, the base of the second bipolar transistor is connected to a resistor and via the latter to one pole of a first capacitor, the anode of the first diode being connected to the other pole of the first capacitor.
In accordance with an added feature of the invention, the input serving to supply power to the control circuit is connected via a second capacitor to an output of a line rectifier, the output of the line rectifier being directly connected to the emitter of the first bipolar transistor.
In accordance with an additional feature of the invention, the other secondary winding is connected at one end to the emitter of the first bipolar transistor and to a pole of a third capacitor, the third capacitor having another pole connected, on the one hand, via a resistor, to the other end of the other secondary winding and, on the other hand, to a cathode of a third diode, the third diode having an anode connected via a potentiometer to an actual value input of the control circuit and, via a fourth capacitor, to the emitter of the first bipolar transistor.
In accordance with yet another feature of the invention, the control circuit has a control output connected via a fifth capacitor to the base of the first bipolar transistor for conducting to the latter control pulses generated in the control circuit.
In accordance with a concomitant feature of the invention, there is provided a sixth capacitor shunting the emitter-collector path of the first transistor.
Other features which are considered as characteristic for the invention are set forth in the appended claim.
The construction and method of operation of the invention, however, together with additional objects and advantages thereof will be best understood from the following description of specific embodiments when read in connection with the accompanying drawings, in which:
FIGS. 1 and 2 are circuit diagrams of the blocking oscillator type switching power supply according to the invention; and
FIG. 3 is a circuit diagram of the control unit RS of FIGS. 1 and 2.
Referring now to the drawing and, first, particularly to FIG. 1 thereof, there is shown a rectifier circuit G in the form of a bridge current, which is acted upon by a line input represented by two supply terminals 1' and 2'. Rectifier outputs 3' and 4' are shunted by an emitter-collector path of an NPN power transistor T1 i.e. t

The cathode of the diode D1 and, therewith, the power supply terminal 9 of the control circuits RS are furthermore connected to one pole of a capacitor C3, the other pole of which is connected to the output 3' of the rectifier G. The capacitance of this capacitor C3 thereby smoothes the positive half-wave pulses and serves simultaneously as an energy storage device during the starting period. Another secondary windi

The nine terminals of the control circuit RS have the following purposes or functions:
Terminal 1 supplies the internally generated reference voltage to ground i.e. the nominal or reference value required for the control or regulating process;
Terminal 2 serves as input for the oscillations provided by the secondary winding III, at the zero point of which, the pulse start of the driving pulse takes place;
Terminal 3 is the control input, at which the existing actual value is communicated to the control circuit RS, that actual value being generated by the rectified oscillations at the secondary winding III;
Terminal 4 is responsive to the occurrence of a maximum excursion i.e. when the largest current flows through the first transistor T1 ;
Terminal 5 is a protective input which responds if the rectified line voltage drops too sharply; Terminal 6 serves for the power supply of the control process and, indeed, as ground terminal;
Terminal 7 supplies the d-c component required for charging the coupling capacitor C2 leading to the base of the first transistor T1 ;
Terminal 8 supplies the control pulse required for the base of the first transistor T1 ; and
Terminal 9 serves as the first terminal of the power supply of the control circuit RS.
Further details of the control circuit RS are described hereinbelow.
The capacity C3 smoothes the positive half-wave pulses which are provided by the secondary winding II, and simultaneously serves as an energy storage device during the starting time. The secondary winding III generates the control voltage and is simultaneously used

The diode D4, together with the resistor R9 in cooperation with the diode D1 and the secondary winding II, forms the starting circuit provided, in accordance with the invention. The operation thereof is as follows:
After the switching power supply is switched on, d-c voltages build up at the collector of the switching transistor T1 and at the input 4 of the control circuit RS, as a function in time of the predetermined time constants. The positive sinusoidal half-waves charge the capacitor C3 via the starting diode D4 and the starting resistor R9 in dependence upon the time constant R9.C3. Via the protective input terminal 5 and the resisto

In FIG. 2, there is shown a further embodiment of the circuit for a blocking oscillator type switching power supply, according to the invention, as shown in FIG. 1. Essential for this circuit of FIG. 2 is the presence of a second bipolar transistor T2 of the type of the first bipolar transistor T1 (i.e. in the embodiments of the invention, an npn-transistor), which forms a further component of the starting circuit and is connected with the collector-emitter path thereof between the resistor R9 of the starting circuit and the current supply input 9 of the control circuit RS. The base of this second transistor T2 is connected to a node which leads, on the one hand, via a resistor R10 to one electrode of a capacitor C7, the other electrode of which is connected to the anode of the diode D4 of the starting circuit and, accordingl
Regarding the operation of the starting circuit according to FIG. 2,

Because of the time constant R9.C3, several positive half-waves are necessary in order to increase the voltage U9 at the supply terminal 9 of the control circuit RS to such an extent that the control circuit RS is energized. During the negative sine half-wave, a partial energy chargeback takes place from the capacitor C3 via the emitter-base path of the transistor T2 of the starting circuit and via the resistor R10 and the capacitor C7, respectively, into the supply network. At approximately 2/3 of the voltage U9, which is limited by the diode D3, the control circuit RS is switched on. At the terminal 1 thereof, the reference voltage Uref then appears. In addition, the voltage divider R5 /R4 becomes effective. At the terminal 3, the control amplifier receives the voltage forming the actual value, while the first bipolar transistor T1 of the blocking-oscillator type switching power supply is addressed pulsewise via the terminal 8.
Because the capacitor C6 is charged via the resistor R6, a higher voltage than Uref is present at the terminal 4 if the control circuit RS is activated. The control voltage then discharges the capacitor C6 via the terminal 4 to half the value of the reference voltage Uref, and immediately cuts off the addressing input 8 of the control circuit RS. The first driving pulse of the switching transistor T1 is thereby limited to a minimum of time. The power for switching-on the control circuit RS and for driving the transistor T1 is supplied by the capacitor C3. The voltage U9 at the capacitor C3 then drops. If the voltage U9 drops below the switching-off voltage value of the control circuit RS, the latter is then inactivated. The next positive sine half-wave would initiate the starting process again.
By switching the transistor T1, a voltage is transformed in the secondary winding II of the transformer Tr. The positive component is rectified by the diode D1, recharing of the capacitor C3 being thereby provided. The voltage U9 at the output 9 does not, therefore, drop below the minimum value required for the operation of the control circuit RS, so that the control circuit RS remains activated. The power supply continues to operate in the rhythm of the existing conditions. In operation, the voltage U9 at the supply terminal 9 of the control circuit RS has a value which meets the condition U9 >[UDs -UBE (T2)], so that the transistor T2 of the starting circuit remains cut off.
For the internal layout of the control circuit RS, the construction shown, in particular, from FIG. 3 is advisable. This construction is realized, for example, in the commercially available type TDA 4600 (Siemens AG).
The block diagram of the control circuit according to FIG. 3

The outer voltage divider of the terminal 1 via the r

Within a provided trigger circuit, the driving pulse length is determined as a function of the sawtooth rise at the terminal 4, and is transmitted to the control logic. In the control logic, the commands of the trigger circuit are processed. Through the zero-crossing identification at input 2 in the control circuit RS, the control logic is enabled to start the control input only at the zero point of the frequency oscillation. If the voltages at the terminal 5 and at the terminal 9 are too low, the control logic blocks the output amplifier at the terminal 8. The output amplifier at the terminal 7 which is responsible for the base charge in the capacitor C2, is not touched thereby.
The base current gain for the transistor T1 i.e. for the first transistor in accordance with the definition of the invention, is formed by two amplifiers which mutually operate on the capacitor C2. The roof inclination of the base driving current for the transistor T1 is impressed by the collector current simulation at the terminal 4 to the amplifier at the terminal 8. The control pulse for the transistor T1 at the terminal 8 is always built up to the potential present at the terminal 7. The amplifier working into the terminal 7 ensures that each new switching pulse at the terminal 8 finds the required base level at terminal 7.
Supplementing the comments regarding FIG. 1, it should also be mentioned that the cathode of the diode D1 connected by the anode thereof to the one end of the secondary winding II of the transformer Tr is connected via a resistor R11 to the protective input 5 of the control circuit RS whereas, in the circuit according to FIG. 2, the protective input 5 of the control circuit RS is supplied via a voltage divider R8, R7 directly from the output 3', 4' of the rectifier G delivering the rectified line a-c voltage, and which obtains the voltage required for executing its function. It is evident that the first possible manner of driving the protective input 5 can be used also in the circuit according to FIG. 2, and the second possibility also in a circuit in accordance with FIG. 1.
The control circuit RS which is shown in FIG. 3 and is realized in detail by the building block TDA 4600 and which is particularly well suited in conjunction with the blocking oscillator type switching power supply according to the invention has 9 terminals 1-9, which have the following characteristics, as has been explained in essence hereinabove:
Terminal 1 delivers a reference voltage Uref which serves as the constant-current source of a voltage divider R5.R4 which supplies the required d-c voltages for the differential amplifiers provided for the functions control, overload detection, short-circuit detection and "standby"-no load detection. The dividing point of the voltage divider R5 -R4 is connected to the terminal 3 of the control circuit RS. The terminal 3 provided as the control input of RS is controlled in the manner described hereinabove as input for the actual value of the voltage to be controlled or regulated by the secondary winding III of the transformer Tr. With this input, the lengths of the control pulses for the switching transistor T1 are determined.
Via the input provided by the terminal 2 of the control circuit RS, the zero-point identification in the control circuit is addressed for detecting the zero-point o

A sawtooth-shaped voltage, the rise of which corresponds to the collector current of the switching transistor T1, is present at the terminal 4 and is minimally and maximally limited by two reference voltages. The sawtooth voltage serves, on the one hand as a comparator for the pulse length while, on the other hand, the slope or rise thereof is used to obtain in the base current amplification for the switching transistor T1, via the terminal 8, a base drive of this switching transistor T1 which is proportional to the collector current.
The terminal 7 of the control circuit RS as explained hereinbefore, determines the voltage potential for the addressing pulses of the transistor T2. The base of the switching transistor T1 is pulse-controlled via the terminal 8, as described hereinbefore. Terminal 9 is connected as the power supply input of the control circuit RS. If a voltage level falls below a given value, the terminal 8 is blocked. If a given positive value of the voltage level is exceeded, the control circuit is activated. The terminal 5 releases the terminal 8 only if a given voltage potential is present.
Forei

DE2417628A1 1975-10-23 363/37
DE2638225A1 1978-03-02 363/49
Other References:
Grundig Tech. Info. (Germany), vol. 28, No. 4, (1981).
IBM Technical Disclosure Bulletin, vol. 19, No. 3, pp. 978, 979, Aug. 1976.
German Periodical, "Funkschau", (1975), No. 5, pp. 40 to 44.
It has even Digital controlled beam scan velocity modulation (SVM) with a unit fitted on the tube neck.
PANASONIC TX-28XD3C QUINTRIX CHASSIS EURO-2M beam scan velocity modulation (SVM) system for a television receiver,

a video signal is applied to a differentiator followed by a limiting differential amplifier. A driver amplifier coupled to the limiting amplifier drives an output stage that supplies current to an SVM coil. Certain video signals with large high frequency content may tend to produce excessive dissipation in the devices of the output stage. To prevent this, a current source for the differential amplifier is controlled by a voltage which is a measure of the average current through the output stage. The magnitude of the current source is varied to thereby vary the peak-to-peak signal output from the limiting amplifier to prevent overdissipation of the output devices. The presence of random noise in the video signal can produce unwanted SVM operation which can impair the viewed image. The unwanted noise component in the video signal can be reduced in amplitude by coring. The coring is unaffected by the variable limiting.
Beam scan velocity modulation (SVM) apparatus with a svm disabling circuit employed for picture sharpness enhancement is disclosed. The beam SVM includes a picture display device, a source of a first video signal having a picture information displayed on the device when the source is selected, an OSD/TELETEXT display generator having on-screen display information or teletext display information displayed on the device when the generator is selected, a scan velocity modulating circuit coupled to the source for modulating information displayed on the device in accordance with the video content of the first video signal, and a svm disabling circuit responsive to the pulses and the dc voltage and coupled to the scan velocity modulating circuit for modifying operation of the scan velocity modulating circuit when the OSD/TELETEXT display generator is selected. The generator produces pulses, on a line by line basis, and a certain level of dc voltage, indicative of insertion of the picture information and of a full-screen teletext display information. With the beam scan velocity modulation apparatus with svm disabling circuit, an OSD display over a certain display size or a full-screen teletext display is obtained on the screen without any ghost image caused by luminance signal.
1. Field of the Invention
This invention relates generally to beam scan velocity modulation (SVM) systems employed for picture sharpness enhancement and more particularly to an output current limiting, apparatus employed in an SVM system.
2. Description of the Related Art
It is well known that an improvement in apparent picture resolution can be achieved by modulating the beam scan velocity in accordance with the derivative of the video signal which controls the beam intensity. This video signal is referred to as the luminance signal and the derivative of the luminance signal is employed for such control. An advantage of this method over a peaking approach to picture sharpness enhancement is the avoidance of blooming of peaked white picture elements.
It may be desirable, however, to use a single differential amplifier stage, followed by another stage which will provide the coring function. In such an arrangement, it may be easier to design cost effective circuitry that still meets the requirements of a flat group delay response.
As indicated above, in order to provide beam scan velocity modulation, one differentiates the video signal. A differentiator has an increasing output with increasing frequency. Thus, if the input video signal has higher than normal high frequency components, then a linear system would deliver higher than normal output current and dissipate higher than normal power in the output stage. In such a prior art system, it is possible to overdissipate the output stages of the beam scan velocity modulation system by responding to a particular video signals with much high frequency content.
Still other circuits are known which operate in a different manner to limit power dissipated in the SVM output stages. In these circuits parallel resistor capacitor combinations with long time constants are provided. These RC combinations are in series with emitter electrodes of transistors which are employed in the output power amplifiers of the SVM system. The transistors operate in a Class B mode with the top transistor conducting on one half cycle of its input waveform and with the bottom device conducting on the other half cycle.
Using this scheme, the bias of the base emitter junction becomes a function of the average amount of high frequency detail in the television image and thereby undesirably introduces more or less output stage coring of the signal depending upon the scene information. Furthermore, this approach requires relatively large magnitude, high voltage capacitors which are expensive and bulky.
As an example, the capacitors used may be 47 μf in value and the resistors 20 ohms in value. The voltage requirements on the capacitors may be in excess of 150 volts. Hence, these capacitors are quite large, bulky and expensive.
SUMMARY OF THE INVENTION
In accordance with an inventive arrangement, a first amplifier is responsive to an input video signal and provides peak-to-peak limiting. A driver amplifier receives the limited signal via a buffer amplifier and provides noise coring subsequent to limiting. An output amplifier coupled to the driver amplifier energizes a scan velocity modulation circuit in accordance with the limited and noise cored video signal.
In accordance with another inventive arrangement, a scan velocity modulation circuit includes means for monitoring the current in the output stage of the SVM circuit and controlling the operation of a preceding stage differential amplifier in accordance with the monitored current. Advantageously, this can prevent overdissipation in the output stage.
1. Field of the Invention
2. Description of the Prior Art
It is well known that an improvement in apparent picture resolution can be achieved by the use of modulation of the beam scan velocity in accordance with the derivative of a video signal which controls the beam intensity. This video signal is known as the luminance signal and the derivative of the luminance signal is employed for the beam SVM. The beam SVM will improve the picture sharpness in a color television system employing a color kinescope.
Many modern color television receivers also employ alternate video sources. An example of such an alternate video source is commonly referred to as an on screen display (OSD) generator. The function of the OSD generator is to provide additional display informations to a viewer while viewing a typical television program. Thus, OSD generator provides for the display on the television screen of time, day, channel number and other various control informations.
In implementing OSD display, the OSD informations are presented as graphical data together with the normal pictures.
A scan modulation circuit modulates the picture displayed on a display device in accordance with the video content of a first video signal. An alternate video signal possesses its picture informations displayed on the display device when the alternate signal is selected. The operation of the scan modulation circuit is varied in accordance with this selection. A problem may occur in regard to scan velocity modulation in television receivers which also include an alternate video signal source such as on screen display generator. As is known, the SVM apparatus operates to modulate the horizontal beam scan velocity in response to differentiated luminance information from the main video source. This modulation may occur prior to OSD deletion of the main luminance signal and insertion of the character signal.
U.S. Pat. No. 5,072,300 (issued to Mark R. Anderson) discloses a beam scan velocity modultion apparatus, which controls the current in a scan velocity modulation (SVM) coil by a blanking pulse in order to eliminate the effect of SVM artefact generation during the operation of an OSD generator in a television receiver. In this arrangement, a ghost image representative of the deleted portions of the main luminance signal may appear on the television screen near or behind the inserted OSD character information since the current flowing in the SVM coil is not completely controlled. The ghost image behind the characters generated by the OSD display appears as an outline of the picture contained in the deleted portions of the main luminance signal.
SUMMARY OF THE INVENTION
The object of the present invention is to provide a beam scan velocity modulation (SVM) apparatus with an SVM disabling circuit capable of eliminating the above-mentioned picture interference when OSD display information and TELETEXT information are displayed over a certain display size on the screen.
In order to achieve the above object, the beam scan velocity modulation (SVM) apparatus with an SVM disabling circuit according to the present invention comprises:
a picture display device;
a source of a first video signal having a picture information displayed on the picture display device when the source is selected;
an OSD/TELETEXT display generator having on-screen display information or teletext display information displayed on the picture display device when the OSD/TELETEXT display generator is selected, the OSD/TELETEXT display generator producing pulses on a line-by-line basis and a certain level of a dc voltage indicative of insertion of the picture information and of a full-screen teletext display information;
a scan velocity modulating circuit coupled to the source for modulating information displayed on the device in accordance with the video content of the first video signal; and
an SVM disabling circuit responsive to the pulses and the dc voltage and coupled to the scan velocity modulating circuit for modifying operation of the scan velocity modulating circuit when the OSD/TELETEXT display generator is selected.
With the beam scan velocity modulation apparatus with SVM disabling circuit, an OSD display over a certain display size or a full-screen teletext display is obtained on the screen without any ghost image caused by a luminance signal.
-----------------------------------------------------------
PHILIPS TDA6103Q Triple video output amplifier:
• High bandwidth: 7.5 MHz typical; 60 V (peak-to-peak
value)
• High slew rate: 1600 V/µs
• Simple application with a variety of colour decoders
• Only one supply voltage needed
• Internal protection against positive appearing
Cathode-Ray Tube (CRT) flashover discharges
• One non-inverting input with a low minimum input
voltage of 1 V
• Thermal protection
• Controllable switch-off behaviour.
GENERAL DESCRIPTION
The TDA6103Q includes three video output amplifiers in
one single in-line 9-pin medium power (SIL9MP) package
SOT111BE, using high-voltage DMOS technology,
intended to drive the three cathodes of a colour CRT.
PINNING
SYMBOL
PIN
DESCRIPTION
Vi1
1
inverting input 1
Vi2
2
inverting input 2
Vi3
3
inverting input 3
GND
4
ground, fin
Vip
5
non-inverting input
VDD
6
supply voltage
Voc3
7
cathode output 3
Voc2
8
cathode output 2
Voc1
9
cathode output 1
The internal thermal protection circuit gives a decrease of
the slew rate at high temperatures: 10% decrease at
130 °C and 30% decrease at 145 °C (typical values on the
spot of the thermal protection circuit).
Cathode output
The cathode output is protected against peak currents
(caused by positive voltage peaks during high-resistance
flash) of 5 A maximum with a charge content of 50 µC.
The cathode is also protected against peak currents
(caused by positive voltage peaks during low-resistance
flash) of 10 A maximum with a charge content of 100 nC.
The DC voltage of VDD (pin 6) must be within the operating
range of 180 to 210 V during the peak currents.
Flashover protection
The TDA6103Q incorporates protection diodes against
CRT flashover discharges that clamp the cathode output
voltage up to a maximum of VDD + Vdiode. To limit the diode
current, an external 1.5 kΩ carbon high-voltage resistor in
series with the cathode output and a 2 kV spark gap are
needed (for this resistor-value, the CRT has to be
connected to the main PCB). This addition produces an
increase in the rise- and fall times of approximately 5 ns
and a decrease in the overshoot of approximately 3%.
VDD to GND must be decoupled:
1.
With a capacitor >20 nF with good HF behaviour (e.g.
foil). This capacitance must be placed as close as
possible to pins 6 and 4, but definitely within 5 mm.
2.
With a capacitor >10 µF on the picture tube base print.
Switch-off behaviour
The switch-off behaviour of the TDA6103Q is controllable.
This is due to the fact that the output pins of the
TDA6103Q are still under control of the input pins for
relative low-power supply voltages (approximately 30 V
and higher).
No comments:
Post a Comment
The most important thing to remember about the Comment Rules is this:
The determination of whether any comment is in compliance is at the sole discretion of this blog’s owner.
Comments on this blog may be blocked or deleted at any time.
Fair people are getting fair reply. Spam and useless crap and filthy comments / scrapers / observations goes all directly to My Private HELL without even appearing in public !!!
The fact that a comment is permitted in no way constitutes an endorsement of any view expressed, fact alleged, or link provided in that comment by the administrator of this site.
This means that there may be a delay between the submission and the eventual appearance of your comment.
Requiring blog comments to obey well-defined rules does not infringe on the free speech of commenters.
Resisting the tide of post-modernity may be difficult, but I will attempt it anyway.
Your choice.........Live or DIE.
That indeed is where your liberty lies.
Note: Only a member of this blog may post a comment.