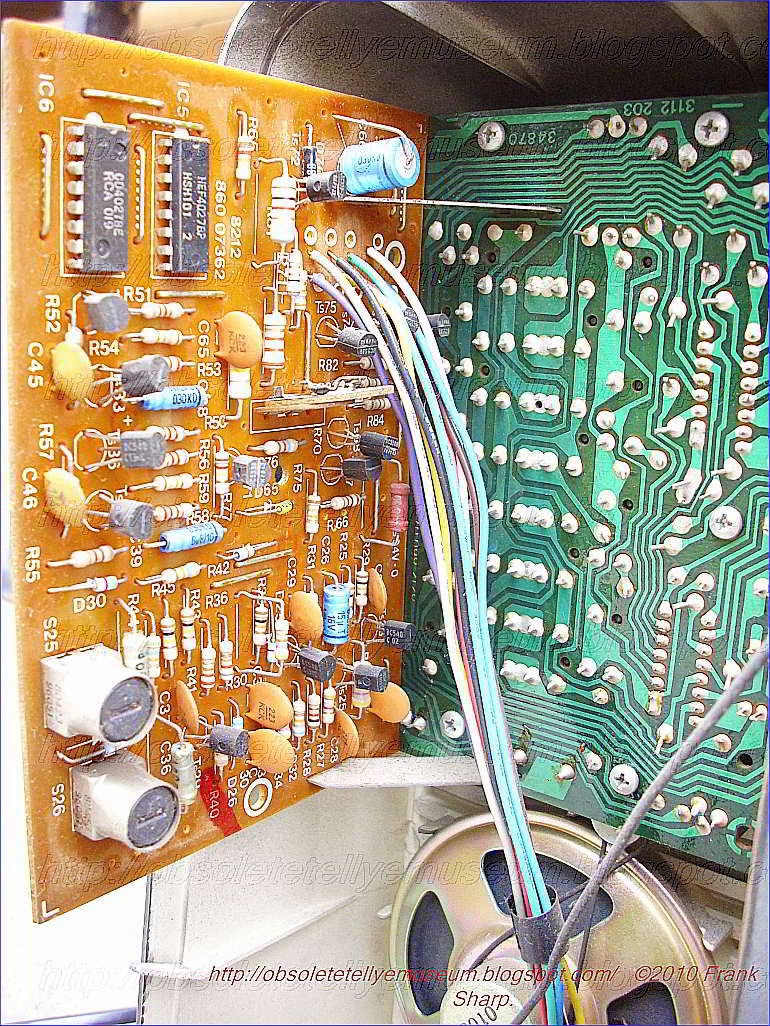

PHILIPS 12B912 /38C CHASSIS TX On a monocarrier are present all parts of the receiver inclusive the power supply with mains transformer.
On the left side up the tuning unit + remote control signal receiver based on cmos IC CD Series after models have implemented a Microcontroller TMS1100 type.
The Philips TX monochrome portable chassis has been in production for several years and large numbers have been sold in the Philips model ranges. several versions, with 12 and 14in. tubes, and with/without remote control. There have also been a number of modifications - most of these are of little significance from the servicing point of view, though it's worth noting that a simplified field generator stage is used in later production.
Power Supply Circuit:


Line Timebase:
The line generator circuit (Fig. 6) is rather unusual. The first transistor TS380 provides


No Sound or Raster:
If there's no sound or raster, check the voltage at the emitter of TS110. If there's no voltage here, check the fuses - VL100 (on the mains transformer), VL110 and VL111. If VL100 or VL110 is open -circuit, check the bridge rectifier diodes D110/111/113/114 and the protection capacitors C116-9 for shorts and if necessary the mains transformer T110 for shorted turns. If VL111 is open -circuit, the 1.t. reservoir capacitor C112 could be leaky. Alternatively there could be a short-circuit in the line or sound output stage. Check the output transistor TS450, then D450, C450 and the scan coupling capacitor C455 in the line output stage. Check the smoothing capacitor C314 (47μF) and the output coupling capacitor C311 (100μF) in the audio output stage. If the fuses are o.k., check the voltage at the collector of TS110. If this is low at 2-8V, check TS110, TS111 and TS112 as necessary. If the voltage at the collector of TS110 is more than 8V, check the boost voltage - at pin 6 of the line output transformer. If the voltage here is less than 15V, check the line output transistor, check whether C455 is leaky, then check the line output transformer by substitution. If the voltage at pin 6 is in excess of 15V, check whether R451 is open -circuit, thus removing the supply to the line oscillator. In the event of R451 being open -circuit, check for shorts in the field generator circuit. If R451 is o.k., check the voltage at the base of the line driver transistor TS410. The reading should be about -0.1V. If this is present, check TS410 and TS450. If the reading is absent, check whether R401 is open -circuit, thus removing the supply to the line oscillator stage. Finally check TS390, TS391 and TS410 by replacement.
Normal Sound, No Raster:
For the sound normal, no raster condition, first check whether the tube's heater is alight. If not, check the continuity of the heater winding. Next remove the aerial plug. If there's insufficient brightness, check the a.g.c. amplifier transistor TS351 (BC548) by replacement. If there's still no brightness, turn the contrast to minimum, the brightness to maximum, and make voltage checks at the c.r.t. base. The cathode voltage (pin 2) should be 67V. If this is incorrect, check the video output transistor TS560 (BF422) and if necessary the field flyback blanking transistor TS565 (BC548C). If the voltage at pin 2 is correct, check the grid voltage (pin 5) which should be about 57V. If this voltage is missing, check whether the grid decoupling capacitor C572 (0.1μF) is short-circuit, then check whether the 95V supply is being developed across C452. If not, check R450 and D453 for being open -circuit. Next check the first anode voltage (pin 6) which should be 160V. If not, check R570 (820kOhm), R452 and D455. Finally check the e.h.t. circuit if necessary - from pin 8 of the line output transformer through the rectifier to the final anode of the c.r.t. Normal Sound, Weak or No Picture In the event of normal sound with a weak picture or no picture, check the voltage at the emitter of the video output transistor TS560. This should be 3.3V. If incorrect, check TS560; if correct, check the video driver transistor TS350 (BC558).
Field Collapse:
In the event of field collapse, check whether the field output stage feed resistor R529 (33n) is open -circuit. If so replace it and check the output transistors TS521/2 (BC338/BC328). Next check the field output stage midpoint voltage - 10.1V at the emitter of TS521. If this is incorrect, check the output transistors, the field driver transistor TS523 (BC548) and the preamplifier transistor TS520 (BC559B). If necessary che

The later simplified circuit is shown in Fig. 2. This time C503 charges from the 95V line via R503 and R507. When the voltage at the junction of R503/7 exceeds the voltage at the base of TS509, both transistors switch on as before. In normal operation the positive -going field sync pulses fed to the emitter of TS509 drive this transistor on just ahead of the free -running switch -on -point.
Loss of Line Sync:
In the event of loss of line sync, first remove the aerial input and check that the 1.t. line is correctly set for 10.8V. If the correct voltage cannot be obtained by adjusting R113, check TS110, TS111, TS112 and make sure that R114 is 3.9Ohm (in some sets it's 4.7MOhm). If the supplies are correct, check the voltage at the positive side of the a.g.c. smoothing capacitor C351 (47μF). With the aerial discon- nected the reading should be 4.3V. With the aerial connected a reading of 6-8V should be obtained. If the voltage conditions are incorrect, suspect the a.g.c. amplifier transistor TS351 (BC548). If necessary, try adjusting the line hold control R394 with the emitter of the flywheel sync transistor TS380 shorted to chassis and the aerial connected. If line lock cannot be obtained, replace the line oscillator transistors TS390 and TS391. If line lock can be obtained but the sync floats on removing the shorting link, suspect TS380 and TS392.
Miscellaneous Faults and Modifications:
Sound buzz with unstable picture, possibly intermittent: Suspect the battery socket - the switch can become tarnished. Replacement cures. Uncontrollable sound: Suspect the d.c. volume control R302 (4.710 or the TBA120AS intercarrier sound chip (IC310). Intermittent line collapse, with vertical line: Change C393 to 0.0015μF. Philips advise that the value of C393 in all sets bearing factory code HU on the chassis or serial plate is checked and changed to 0.0015μF if necessary. Bright vertical line at left-hand side: If a replacement line output transformer does not cure this, change C412 to 0.006814F and TS410 to a BC637 (note that the base connections differ). Distortion at low volume: Change R300 to 18kOhm, R311 to 56f1, R312 to 3.3kOhm/ and R315 to 120kOhm. Brightness range: Where the tube is type 12VCUP4, R576 should be 470kOhm Where the tube is type 12BJP4 it should be 820kOhm.
Power supply is realized with mains transformer and Linear transistorized power supply stabilizer, A DC power supply apparatus includes a rectifier circuit which rectifies an input commercial AC voltage. The rectifier output voltage is smoothed in a smoothing capacitor. Voltage stabilization is provided in the stabilizing circuits by the use of Zener diode circuits to provide biasing to control the collector-emitter paths of respective transistors.A linear regulator circuit according to an embodiment of the present invention has an input node receiving an unregulated voltage and an output node providing a regulated voltage. The linear regulator circuit includes a voltage regulator, a bias circuit, and a current control device.
In one embodiment, the current control device is implemented as an NPN bipolar junction transistor (BJT) having a collector electrode forming the input node of the linear regulator circuit, an emitter electrode coupled to the input of the voltage regulator, and a base electrode coupled to the second terminal of the bias circuit. A first capacitor may be coupled between the input and reference terminals of the voltage regulator and a second capacitor may be coupled between the output and reference terminals of the voltage regulator. The voltage regulator may be implemented as known to those skilled in the art, such as an LDO or non-LDO 3-terminal regulator or the like.
The bias circuit may include a bias device and a current source. The bias device has a first terminal coupled to the output terminal of the voltage regulator and a second terminal coupled to the control electrode of the current control device. The current source has an input coupled to the first current electrode of the current control device and an output coupled to the second terminal of the bias device. A capacitor may be coupled between the first and second terminals of the bias device.
In the bias device and current source embodiment, the bias device may be implemented as a Zener diode, one or more diodes coupled in series, at least one light emitting diode, or any other bias device which develops sufficient voltage while receiving current from the current source. The current source may be implemented with a PNP BJT having its collector electrode coupled to the second terminal of the bias device, at least one first resistor having a first end coupled to the emitter electrode of the PNP BJT and a second end, a Zener diode and a second resistor. The Zener diode has an anode coupled to the base electrode of the PNP BJT and a cathode coupled to the second end of the first resistor. The second resistor has a first end coupled to the anode of the Zener diode and a second end coupled to the reference terminal of the voltage regulator. A second Zener diode may be included having an anode coupled to the cathode of the first Zener diode and a cathode coupled to the first current electrode of the current control device.


TDA2540 IF AMPLIFIER WITH DEMODULATOR AND AFC
DESCRIPTION
The TDA2540 and 2541 are IF amplifier and A.M.
demodulator circuits for colour and black and white
televisionreceiversusingPNPorNPNtuners. They
are intended for reception of negative or positive
modulation CCIR standard.
They incorporate the following functions : .Gain controlled amplifier .Synchronous demodulator .White spot inverter .Video preamplifier with noise protection .Switchable AFC .AGC with noise gating .Tuner AGC output (NPN tuner for 2540)-(PNP
tuner for 2541) .VCR switch for video output inhibition (VCR
play back)
.SUPPLYVOLTAGE : 12V TYP
.SUPPLYCURRENT : 50mATYP
.I.F. INPUT VOLTAGE SENSITIVITY ATF = 38.9MHz : 85mVRMS TYP
.VIDEO OUTPUT VOLTAGE (white at 10% oftop synchro) : 2.7VPP TYP
.I.F. VOLTAGE GAIN CONTROL RANGE :
64dB TYP .SIGNAL TO NOISE RATIO AT VI = 10mV :
58dB TYP .A.F.C. OUTPUT VOLTAGE SWING FOR
Df = 100kHz : 10V TYP
PHILIPS 12B912 /38C CHASSIS TX TELEVISION DIAGRAM AND DEFLECTION CIRCUIT:
A unidirectional conductive device is coupled from a base terminal to a collector terminal of a horizontal deflection output transistor in a television receiver and poled in a direction to prevent the transistor from saturating when it is driven into its conductive state during a portion of each deflection cycle. Biasing means is coupled to the diode to preselect the desired operating voltage of the transistor during its conduction period.
In present day transistor deflection circuits, for example, those used in the horizontal output stage of a television receiver; the output transistor is normally operated in a switching mode, that is, the transistor is driven into saturation during a trace interval of each deflection cycle and driven out of conduction during the retrace portion of each deflection c


In the solid state deflection art, however, it is desirable to reduce the turn-off time of the device not to increase the frequency of operation of the circuit, but rather to prevent second breakdown of the device as the relatively large inductive voltage pulse appears during the initial portion of the flyback interval, when current flowing through the deflection winding is interrupted to initiate the retrace portion of each deflection cycle.
The non-saturated operation of the deflection output transistor is achieved in circuits embodying the present invention by automatically holding the collector voltage above the saturation level by shunting excess base drive from the base to emitter junction into the collector circuit. Prior transistor deflection systems employ only the saturated operation of the deflection output device.
Circuits embodying the present invention include a deflection output transistor having a diode coupled between its base and collector terminals and poled to prevent the transistor from being driven into saturation during its conduction period of each deflection cycle.
The invention can be more fully understood by referring to the drawings together with the description below and the accompanying claims.
In the drawings:
FIG. 1 illustrates in block and schematic diagram form, a television receiver including a solid state deflection output stage embodying the present invention;
FIG. 2a is a waveform diagram of the voltage present at the collector terminal 55c of transistor 55 in FIG. 1;
FIG. 2b shows the drive current to terminal A in FIG. 1;
FIG. 2c is a waveform diagram of the current in diode 56 in FIG. 1;
FIG. 2d is a waveform diagram of the base current flowing in transistor 55 of FIG. 1;
FIG. 3 is a schematic diagram of an alternative embodiment of the present invention;
FIG. 4a is a waveform diagram of the voltage appearing at the terminal 366 in FIG. 3;
FIG. 4b is a waveform diagram of the drive current to terminal A in FIG. 3;
FIG. 4c is a waveform diagram of the current in diode 356 in FIG. 3; and
FIG. 4d is a waveform diagram of the base drive current to transistor 355 in FIG. 3.
Referring specifically to FIG. 1,

The automatic gain control stage 25 operates in a conventional manner to provide gain control signals which are applied to a radio frequency amplifier included in tuner 12 and to the I.F. amplifier 14. Sync separator 42 separates the synchronization information from the video information and also separates the horizontal synchronizing information for the vertical synchronizing information. The vertical synchronizing pulses derived from sync separator 42 are applied to the vertical deflection system 44 which provides the required deflection current to a vertical deflection winding 43 associated with kinescope 30 by means of the interconnection Y--Y. The horizontal synchronizing pulses from sync separator 42 are applied to an automatic frequency control detector 45 which serves to synchronize a horizontal oscillator 46 with the horizontal synchronizing pulses. The horizontal oscillator stage 46 is coupled to a horizontal driver stage 48 which develops the required drive signal and may be coupled by means of an output transformer in stage 48 (not shown) to a transistorized horizontal output stage 50. The transformer secondary, coupled to terminal A, provides a direct current path for the drive current.
The horizontal output stage 50 includes an output transistor 55 having a b

The output stage includes a unidirectional conductive device such as a diode 56 coupled between the base and collector terminals 55b and 55c of transistor 55. Stage 50 also includes a damper diode 57 coupled across transistor 55, a retrace capacitor 58 coupled across transistor 55 and the series combination of a horizontal deflection winding 59 and an S-shaping capacitor 60 also coupled across transistor 55. Output stage 50 also includes a flyback transformer 61 with a primary winding 61p coupled from a source of operating potential (B+) to the collector terminal 55c of transistor 55. A secondary winding 61s on transformer 61 develops high voltage pulses which are coupled to a high voltage rectifier 63 to provide the ultor voltage for application to a terminal 32 on kinescope 30. Flyback transformer 61 may also include additional windings (not shown) for providing, for example, keying pulses to the AGC stage 25.
The output stage 50 in FIG. 1 is a conventional shunt fed trace driven circuit with the exception of the diode 56 and the bias network including resistor 52 and capacitor 53. Beginning at the center of the trace interval of the deflection cycle, the yoke current is zero and capacitor 60 has a maximum charge. The drive signal applied to the base terminal 55b of transistor 55 turns this device on, thereby completing the conduction path for yoke current which includes capacitor 60, yoke 59 and the collector to emitter current path through transistor 55. During this portion of scan the yoke current is supplied by the charge on capacitor 60 and increases to a maximum value in one direction at which time scan retrace is initiated by driving transistor 55 out of conduction by applying an appropriate signal from the driver stage 48 to the base 55b of transistor 55. During the latter portion of the trace interval when the magnitude of the yoke current is increasing, the output transistor of prior circuits is normally driven into saturation and is in this conduction state at the instant retrace is initiated. During the first portion of retrace, the yoke current is at a maximum and resonates with the retrace capacitor 58 by charging capacitor 58 in a polarity to reverse bias the damper diode 57. As the yoke current decreases to zero, capacitor 58 has a maximum charge impressed upon it; and during the second portion of retrace, the capacitor (58) drives current through the yoke in a reverse direction until it is discharged and the voltage across it reverses sufficiently to forward bias damper diode 57. Diode 57 then conducts during this first portion of trace to complete the current path for yoke current which is, at this instant, at a maximum value in a direction in yoke 59 to charge capacitor 60 and is increasing toward zero. At the mid-point of trace the yoke current has reached zero and the cycle is completed by driving transistor 55 into conduction once again.
Turning now to the operation of the circuitry of FIG. 1 including the present invention, reference is made to the waveform diagrams of FIG. 2. The initial portion of trace is represented in FIG. 2 by the time period between t 0 and t 1 in the figure. It is recalled that during this period damper diode 57 is conducting. The voltage at collector terminal 55c of transistor 55 is represented by the voltage waveform (V c ) in FIG. 2a and is equal to the forward voltage drop across diode 57 which is of the order of -0.7 volts. At some non-critical time before t 1 , the horizontal driver 48 provides a drive current (I A ), as is shown in FIG. 2b. This current flows through diode 56 as is illustrated in FIG. 2c, since the diode is forward biased. [The cathode of diode 56 is at the same voltage as collector terminal 55c (-0.07 volts) and the drive current produces a positive voltage at point A which is at the anode of diode 56.] As time t 1 (the center of trace) is reached, damper diode 57 turns off allowing the collector voltage on transistor 55 to increase as shown in FIG. 2a. At the same time, a portion of the drive current flowing into terminal A is conducted by the now forward biased base to emitter junction of transistor 55 as is illustrated by the waveform of FIG. 2d. Transistor 55 is now conducting the increasing yoke current during the latter portion of scan represented by the period from t 1 to t 2 in FIG. 2. As the magnitude of the yoke current increases during the t 1 to t 2 interval, the base current in transistor 55 increases as shown in FIG. 2d. Diode 56 conducts as illustrated in FIG. 2c to shunt the remaining portion of the applied drive current at terminal A. It is noted that the sum of the currents shown in FIGS. 2c and 2d will equal the current shown in FIG. 2b. T

At time t 2 retrace is initiated by applying a relatively large negative drive signal as shown in FIG. 2b to the base terminal of transistor 55. During the retrace interval (t 2 to t 0 in FIG. 2), the collector voltage increases in a typical manner as illustrated in FIG. 2a. At time t 0 the cycle is again repeated.
The circuit modification illustrated in FIG. 3 is another embodiment of the invention which reduces the change in voltage applied to the yoke 59 of FIG. 1 at time t 1 . As shown in FIG. 2a, when diode 57 turns off and transistor 55 conducts, the voltage at the collector terminal 55c of transistor 55 changes by as much, for example, as 6 volts. This voltage change, which is coupled to the yoke 59, will vary the rate of change of yoke current during the center of trace and may, in certain circuits, cause an undesirable non-linearity in the scanning rate. As FIG. 4a illustrates, the circuit of FIG. 3 reduces this change in voltage at the mid-point of trace (t 1 ).
Referring to FIG. 3, the circuit elements which correspond to those of FIG. 1 are prefaced by the numeral 3. In explaining FIG. 3, it is helpful to refer to the waveform diagrams of FIG. 4. Transformer 364 in FIG. 3 is a tightly coupled auto-transformer wherein the tap point 365 may be, for example, at the 5 percent point on the transformer. That is, the segment between terminals 365 and 366 contain 5 percent of the total number of windings on transformer 364. Transformer 364 may also include a secondary winding such as the high voltage winding which is not shown in the figure. In operation, as drive current is applied at sometime prior to t 1 as is shown in FIG. 4b, damper diode 357 is conducting and the voltage at terminal 366 is therefore at approximately -0.7 volts. Drive current flowing into terminal A as represented in FIG. 4b will be conducted by diode 356 during this interval as indicated by the diode current waveform in FIG. 4c. At the middle portion of trace (t 1 ), the damper diode turns off and voltage at terminal 366 is thereby allowed to go slightly positive (less than 0.7 volts). The collector voltage of transistor 355 is held at a value of approximately 5 volts (assuming, for example, the B+ voltage is equal to 100 volts and the collector is coupled to the tap 365 on transformer 3

During the latter portion of trace, the transistor tends to saturate and the collector voltage at terminal 355c tends to decrease. As this occurs, more current will flow from the B+ terminal through the upper portion of transformer 364. Due to the relatively tight coupling of the segments of transformer 364, terminal 366 experiences a decrease in voltage which controls the forward bias applied to diode 356 to shunt sufficient drive current to hold the transistor 355 out of saturation. The collector voltage of transistor 355 is thus held at some preselected value depending on the location of tap point 365 on transformer 364. Since transformer 364 is utilized, terminal 366 wil

Although the specific embodiments of the invention are illustrated in the horizontal deflection output stage of a black and white television receiver, the invention has equal applicability to other deflection systems and may be utilized in a color television receiver.
No comments:
Post a Comment
The most important thing to remember about the Comment Rules is this:
The determination of whether any comment is in compliance is at the sole discretion of this blog’s owner.
Comments on this blog may be blocked or deleted at any time.
Fair people are getting fair reply. Spam and useless crap and filthy comments / scrapers / observations goes all directly to My Private HELL without even appearing in public !!!
The fact that a comment is permitted in no way constitutes an endorsement of any view expressed, fact alleged, or link provided in that comment by the administrator of this site.
This means that there may be a delay between the submission and the eventual appearance of your comment.
Requiring blog comments to obey well-defined rules does not infringe on the free speech of commenters.
Resisting the tide of post-modernity may be difficult, but I will attempt it anyway.
Your choice.........Live or DIE.
That indeed is where your liberty lies.
Note: Only a member of this blog may post a comment.