GRUNDIG SUPER COLOR 8285 (GSC700) CHASSIS GSC700
The CHASSIS GRUNDIG GSC700 is a unique concept of television Chassis modular circuitry.
NO ONE worldwide have had s similar idea like the German firm GRUNDIG.
The FULLY ULTRA MODULAR CHASSIS GSC700 have a brother called GSC600 that you can see here.
This is a Very Complex Chassis even if it is appearing simple.
The serviceability is pretty unique with diagnose Lamps (LED) fitted
almost on every Unit with the function of signaling a path to the
service to reach the defective Unit via a structured and trained search.
The GRUNDIG GSC700 was Produced for a time inferior to a Year, Between
1979 1980. Production ended quickly due to very hight COSTS !!!!
Grundig in the West Germany, was the firm able to contrast the japanese electronics invasion of Europe in that era of time.
It has launched a new range of television equipment which should be considered a service
engineer's
dream. The equipment, which includes both conventional colour TV
receivers and a domestic TV projector , automatically Identifies faults
and indi-cates the part: to be replaced.
In
response to the criticism that such a system will make skilled
engineers redundant, Grundig argues that the new design is not intended
to encourage do-it-yourself repairs, But it should free TV retailers and
rental companies from the obligation to send their best engineers to
amend faulty sets in peoples homes.
According
to Grundig, from now on the companies most proficient engineers can
remain in the vrorkshop, where their time and abilities an most
profitably deployed, leaving lees-skilled people to carry out the
unproductive task of making the house calls.
All Grundig Super Color (Super color 80 range of TV receivers, and the Cinema 9000
TV
projector) , are designed around a similar chassis. This contains a
large circuit board to which just three components are solidly secured.
All the remaining electronic parts are contained
in
12 modules plug-fitted into sockets on the circuit board. Each plug-in
module, clad in metal to screen the components from outside electrical
interference, carries a tiny light emitting diode (LED) If any component
fails, the LED on the module containing the component cease to glow
indicating task for eventually schematic search to identify and replace
the faulty module,
which is returned either toGrundig or the service trained workshop for repair.
(Where money have had NO RULE The ENGINEERS WERE STARTING TO "DANCE",)
GRUNDIG SUPER COLOR 8285 CHASSIS GSC700 Remote control television with external data bus connection,
Remote Control With MOS IC's For TV Sets: THE GRUNDIG AV FEATURE CONNECTOR TECHNOLOGY:A
television receiver is provided for use as a picture display terminal
for electronic peripheral equipment, where a control system with a
data-bus is built into the television receiver for multitude of commands
and in which the television receiver is intended to be used in addition
to the normal direct reception of televised pictures for other possible
applications. The television receiver can serve as a monitor for a
picture tape recorder, which is equipped for recording independently of
the television receiver. A complete television receiving set is provided
with automatic transmitter seeking mechanism and electronic channel
storage.
2. A television receiver as a picture terminal according to claim 1, in which said external coupling includes a connecting cable between the external connections of the television set and the peripheral device forming a unitary unit together with a decoder which transforms the data from the data collector into a code which directly controls the functions of the peripheral device.
3. A television receiver as a picture terminal according to claim 1 or 2, in which the peripheral device is a picture taping device which operates for recording independently from the television set which acts as a monitor.
4. A television receiver as a picture terminal according to claim 1, in which the functions controlled by said first commands include the on-off switching, picture, sound and channel selection of the television receiver and the functions controlled by said second commands include electronic program storage and changeover functions.
Integrat

Television receivers available today in many designs provide for up to 30 remotely controlled channels or channels controlled by the received signal (tele-signal) to properly operate. Additionally, infrared control is also becoming popular. These controls provide commands by means of a databus so that the operation of the various functions is possible with the provision of additional commands.
It is further known to equip peripheral equipment such as video tape recorders with a so-called electronic-tap-key rather than keys with a long throw so that all parts which are susceptable to mechanical wear are eliminated and replaced by digital controls.
It has become of interest to connect the peripheral equipment such as the video tape recorder to the television receiver so that both can be conveniently operated. With the development of new concepts simplification of design becomes critical for ease of operation and reduction of expense.
A

The FIGURE is a diagrammatic showing of a television receiver and electronic periphery device incorporating the invention.
A television receiver and electronic peripheral device incorporating the invention are shown in the FIGURE. The television receiver 10 can be used as a picture display terminal for peripheral device 12. This provides the advantage, that by means of a single tele-control signal, the control of functions of the receiving and displaying sections of the television receiver can be accomplished as wel

The primary expenses result from the necessary cable connections between the external terminals of the television receiver and the peripheral equipment, as well as the auxiliary apparatus, such as decoder 18, which decodes the data from the databus 14 and prepares it for the peripheral equipment. These expenses are reduced by simplified design, in which the connecting cables 20 and 22 together with the auxiliary apparatus or decoder 18 are combined in one component or building block. This building block can be offered as an accessory to the user of television receivers with peripheral equipment.
The invention can be used with especial advantage in connecting a television receiver with a picture tape recorder as a peripheral equipment. The picture tape recorder is equipped preferably for recording independently from the television receiver, so that the latter serves as a monitor only. With such a switching combination it is possible, for example, to accomplish this with a single control system, and by the help of a tele-control system, which is built into the television receiver, to operate the channel selection and drive mechanism control, the control for an electronic switch clock and programming of the switch commands of the picture tape recorder as well as the control of the function of the receiving and displaying unit of the receiver. In this way it is possible to use the tele-control of a television receiver additionally for the tele-control of the picture tape recorder without substantial higher expenses.
GRUNDIG CHASSIS GSC700 Chassis for a television set.(IN GERMAN)

2. Fernsehger·at nach Anspr

3. Fernsehger·atechassis nach Anspruch 2, d a d u r c h g e k e n n z e i c h n e t , dass das Geh·ause (5)aus einem rechteckigen Rahmen (6) und zwei diesem angepassten, abnehmbaren, an den L·angsseiten rechtwinklig abgebogenen Deckeln (7, 8) besteht, die einseitig am Rahmen gelenkartig eingeh·angt und mindestens am anderen Ende durch eine l·osbare snapin-Verbindung (9, 10) und zus·atzlich durch ein Verschlusselement (11, 13, 14, 15, 16) am Rahmen festgelegt sind.
4. Fernsehger·atechassis nach Anspruch 3, d a d u r c h g e k e n n z e i c h n e t , dass die abnehmbaren Deckel (7, 8) je eine Lasche (12) aufweisen, die rechtwinklig zum Rahmen (6) umgebogen und mit diesem durch ein beide Verbindungsteile durchdringendes Verschlusselement (11, 13, 14, 15, 16) verbunden ist.
5. Fernsehger·atechassis nach Anspruch 1, d a d u r c h g e k e n n z e i c h n e t , dass das Geh·ause (5) im wesentlichen aus einem einzigen, an einer Seite offenen Teil (26) besteht, der auf seiner Innenseite Fuhrungs und Halteteile (28), insbesondere in Form von geschlitzten Pr·agungen, zum Sichern der Lage einer die Bauelemente und Bauteile tragenden elektrischen Leiterplatte (27) aufweist, die zus·atzlich durch mindestens ein Verschlusselement (29, 30, 31, 34) festgelegt ist und nach dem L·osen des Verschlusselements aus dem Geh·ause herausgezogen werden kann.
6. Fernsehger·atechassis nach einem oder mehreren der Anspr·uche 1 bis 5, d a d u r c h g e k e n n z e i c h n e t, dass das Verschlusselement (11, 13; 29) aus einem Kunststoffteil besteht, das einen mit einem Schlitz versehenen Flachkopf (15; 30) und einen daran anschliessenden federnden Teil (16; 31, 34) aufwei

7. Fernsehger·atechassis nach Anspruch 6, d a.d u r c h g e k e n n z e i c h n e t , dass die Funktionsgruppe vor unbefugtem Eingriff zus·atzlich durch ein den Flachkopf (15; 30) des Verschlusselements (11, 13; 29) und einen benachbarten Bereich Uberdeckende Versiegelung (19), insbesondere in Form eines spezifisch gekennzeichneten Filmes, gesichert ist.
8. Fernsehger·atechassis nach einem oder mehreren der Anspruche 1 bis 7, d a d u r c h g e k e n n z e i c h n e t, dass das Geh·ause (5) im wesentlichen aus d·unnem Abschirmblech mit EntlUftungsschlitzen (20, 21; 35) oder -l·ochern zur Abf·uhrung der Verlustw·arme besteht.
9. Fernsehger·atechassis nach Anspruch 8, d a d u r c h g e k e n n z e i c h n e t , dass das Geh·ause (5) in mehrere HF-dichte Kammern aufgeteilt ist.
10. Fernsehger·atechassis nach Anspruch 8 oder 9, d a d u r c h g e k e n n z e i c h n e t , dass das Abschirmblech mit den K·uhlblechen (22) f·ur w·armeempfindliche Bauelemente w·armeleitend verbunden ist.
11. Fernsehger·atechassis nach einem oder mehreren der Anspr·uche 1 bis 10, d a d u r c h g e k e n n z e i c h n e t , dass das G

12. Fernsehger·atechassis nach einem oder mehreren der Anspr·uche 1 bis 11, d a d u r c h g e k e n n z e i c h n e t , dass das Geh·ause (5) an seiner der Ger·ater·uckwand zugewandten Seite eine Einrichtung (38) zum Anzeigen einer fehlerhaften Funktion der Funktionsgruppe (2) aufweist.
13. Fernsehger·atechassis nach einem oder mehreren der Anspr·uche 1 bis 12, d a d u r c h g e k e n n z e i c h n e t , dass das Geh·ause (5) an seiner der Ger·ater·uckwand zugewandten Seite eine oder mehrere Anschlussbuchsen (23; 36) und/oder Messanschlussstellen (24; 37) zum Pr·ufen der Funktionsf·ahigkeit der Funktionsgruppe (2) aufweist. Beschreibung:

Solche Fernsehempf·anger brauchen daher nicht mehr in die Werkstatt zur Reparatur transportiert zu werden; die Reparaturkosten k·onnen deshalb niedriger festgelegt werden, und ausserdem braucht die ganze Reparatur nur wenige Minuten zu dauern.

Eine derartige Technik bietet auch besondere M·oglichkeiten der Automatisierung und Rationalisierung in der Fertigung, sie bringt aber insbesondere dem Handel und besonders dem Service Tec

Aufgabe Der im Anspruch 1 angegebenen Erfindung liegt die Aufgabe zugrunde, bei einem in einzelne steckbare Funktionsgruppen aufgeteilten Fernsehger·atechassis erkennbar zu machen, wenn ungeschulte Kr·afte an den Funktionsgruppen gearbeitet haben, um elektrische oder mechanische Defekte zu beheben.
Vorteile Mit dem Fernsehger·atechassis nach der Erfindung wird erreicht, dass die Funktionsgruppen besser vor Eingriffen durch ungeschulte Kr·afte gesch·utzt sind. Zumindest bietet die Erfindung den Vorteil, dass ein unbefugter Eingriff in die Funktionsgruppe sofort angezeigt und somit vom Handel oder Hersteller erkannt wird. Auf diese Weise f·uhrt die Erfindung f·ur den Handel oder den Hersteller zu einer gewissen Kostenersparnis, da der Unbefugte sich nicht mehr auf seine Gew·ohrleistungsan spr·uche berufen kann.

Darstellung der Erfindung Die Erfindung wird im folgenden anhand schematischer Zeichnungen n·aher erl·autert.

Das in Fig. 1 dargestellte Fernsehger·atechassis besteht im wesentlichen aus dem Chassisrahmen 1, den Funktionsgruppen 2 und einer allen Funktionsgruppen gemeinsamen elektrischen Leiterplatte 3. Der die Leiterplatte 3 aufnehmende Chassisrahmen 1 ist bei abgenommener Ger·ater·uckwand ausziehbar und um eine horizontale, zur Achse der Bildr·ohre 4 senkrechte Achse schwenbar, damit die Leiterplatte auch auf der den Funktionsgruppen 2 abgewandten Seite leicht zug-·anglich ist. Die einzelnen Funktionsgruppen 2 sind mit ihrem Steckverbinder in einen zugeordneten Stechverbindungsteil der Leiterplatte 3 eingesteckt und zus·atzlich durch Halterungsmittel gegen ein ungewolltes L·osen von der Leiterplatte gesichert.
Die Grundleiterplatte

Die einzelnen Funktionsgruppen 2 sind je nach der in ihr enthaltenen Empf·angerschaltung unterschiedlich ausgebildet. Insbesondere ist es erforderlich, bestimmte Funktionsgruppen, wie z. B. Tuner, Abstimmbaustein und ZF-Baustein, gegen passive als auch aktive St·orstrahlung abzuschirmen. Diese und ·ahnliche Forderungen finden bei der Ausgestaltung der Funktionsgruppen des Fernsehger·atechassis gem·ass der Erfindung Ber·ucksichtigung.
Eine einzelne Funktionsgruppe der in Fig. 2 dargestellten Art besteht aus einem im wesentlichen allseitig geschlossenen Abschirmgeh·ause 5 aus d·unnem Blech und einer darin befindlichen elektrischen Leiterplatte, die die Verdrahtung und die Bauelemente tr·agt und im Geh·ause durch F·uhrungsprugungen und ggf. durch L·otung festgelegt ist. Das metallische Abschirmgeh·ause 5, das zugleich auch f·ur die Abf·uhrung der Verlustw·arme dient, besteht aus mehreren l·osbar miteinander verbundenen Teilen, und zwar aus einem rechteckigen Rahmen 6 und zwei diesem angepassten Ded < eln 7, 8.
Die Verbindung zwischen Rahmen 6 und Deckel 7, 8 erfolgt dadurch, dass diese einseitig am Rahmen gelenkarti
Es ist somit ersichtlich, dass das geschlossene Abschirmgeh·ause 5 die Bauelemente und Bauteile der Funktionsgruppe vor ·ausserem Zugriff sch·utzt. Da jedoch das Abschirmgeh·ause 5 aus mehreren l·osbar miteinander verbundenen Teilen 6, 7, 8 besteht, die mindestens so weit ge·offnet werden k·onnen, dass die Bauelemente und Bauteile der Funktionsgruppe frei zug·anglich sind, k·onnte der Fall eintreten, dass ungeschulte Kr·afte an einer solchen Funktionsgruppe arbeiten. Um das zu verhindern oder zumindest erkennbar zu machen, sind die l·osbar miteinander verbundenen Teile 6, 7, 8 zus·atzlich durch mindestens ein Verschlusselement 11 festgelegt, hierzu weisen die abnehmbaren Deckel 7, 8 je eine Lasche 12 auf, die rechtwinklig zum Geh·auserahmen 6 umgebogen und mit diesem durch ein beide Verbindungsteile durch dringendes Verschlusselement 11 verbunden ist.

Bei dem in Fig. 4 dargestellten Ausf·uhrungsbeispiel eines Verschlusselementes 13 besteht dieses aus einem Kunststoffteil, das einen mit einem Schlitz 14 versehenen Flachkopf 15 und einen daran anschliessenden federnden Teil 16 aufweist. Ein solches Verschlusselement wird in Ausnehmungen 17, 18 der Geh·auseteile 12 bzw. 6 eingesetzt. Durch entsprechende Gestaltung der Ausnehmungen 17, 18 ist es m·oglich, dass beim Drehen des Verschlusselementes 13, z. B. mittels eines Schraubenziehers, eine Schneid- oder Scherwirkung erzeugt wird, durch die der Flachkopf 15 des Verschlusselementes abgetrennt wird. Zu diesem Zweck wird die dem Flachkopf abgewandte Ausnehmung 18 im Geh·auserahmen 6 in Form eines scharfkantigen Kreuzschlitzes ausgebildet, w·ahrend die andere Ausnehmung 17 im Geh·auseteil 12 eine kreisf·ormige Bohrung ist.
Zur weiteren Sicherung der Funktionsgruppe gegen unbefugten Eingriff kann eine Versiegelung des Verschlusselements 11, 13 angewendet werden. Bei dem aus Fig. 4 ersichtlichen Verschlusselement 13 ist es zweckm·assig, hierzu einen spezifisch gekennzeichneten Film 19 zu verwenden, der den Flachkopf 15 des Verschlusselements und einen benachbarten Bereich ·uberdeckt. Bei dem Versuch, das Verschlusselement 11, 13 zu l·osen, wird dann in jedem Fall die Versiegelung deutlich sichtbar ver·andert oder zerst·ort.
Die Ausf·uhrungsform einer Funktionsgruppe nach Fig. 2 eignet sich insbesondere f·ur den Tuner-, Abstimm- und ZF-Baustein. Bei diesen Bausteinen is

Eine weitere Verbesserung bei diesem Aufbau ist m·oglich, wenn die Abf·uhrung der sch·adlichen W·arme durch zus·atzlich im Geh·ause untergebrachte K·uhlbleche 22 unterst·utzt werden kann, die mit dem Abschirmgeh·ause 5 w·armeleitend verbunden sind.
Auch die Aufteilung des Abschirmgeh·auses 5 in mehrere HF-dichte Kammern kann Vorteile bringen. Zu diesem Zweck wird das metallische Abschirmgeh·ause 5 im Innern mit Trennw·anden zum Abteilen der einzelnen Schaltungsbaugruppen untereinander versehen.
Ferner k·onnen am Abschirmgeh·ause 5 an der der Ger·ater·uckwand zugewandten Seite eine Antennenanschlussbuchse 23 oder eine andere Buchse, wie z. B. die Videobuchse, f·ur den Anschluss eines Zusatzger·ates mechanisch befestigt werden. Weiter ist es m·oglich, das Abschirmgeh·ause 5 mit Durchbr·uchen 24 zu versehen, durch die hindurch Abgleichvorg·ange, z. B. nach einer Reparatur, vorgenommen werden k·onnen, oder durch die Messpunkte zum Anschliessen von Pr·ufger·aten gef·uhrt sind bzw. zug·anglich werden. Auch diese Mess- und Abgleichanschlussstellen werden zweckm·assigerweise an der der Ger·ater·uckwand zugewandten Seite des Abschirmgeh·auses 5 angebracht.
Auf der der Ger·ater·uckwand abgewandten Seite ist das Abschirmgeh·ause 5 mit einem Steckverbindungsteil 25 zum Einstecken in eine den Funktionsgruppen 2 gemeinsame elektrische Leiterplatte 3 versehen. Wie bereits erw·ahnt, ist diese Leiterplatte in einem um eine Achse schwenkbaren Chassisrahmen 1 angeordnet, die senkrecht zur Bildr·ohrenachse und in horizontaler Richtung verl·auft.
Bei der in Fig. 3 dargestellten Funktionsgruppe beste
Um zu verhindern, dass eine ungeschulte Kraft an den Bauelementen und Bauteilen einer solchen Funktionsgruppe arbeitet, ist die Leiterplatte 27 auf zwei Seiten durch je ein Verschlusselement 29 im Abschirmgeh·ause 26 festgelegt, so dass erst nach dem L·osen des Verschlusselements die Leiterplatte herausgenommen werden kann, Dabei erf·ahrt das Verschlusselement wiederum eine nichtreversible Ver·anderung, wie bereits im Vors

Ein hierf·ur geeignetes Verschlusselement 29 ist in Fig. 5 dargestellt. Auch dieses Verschlusselement besteht aus einem Kunststoffteil, das einen mit einem Schlitz versehenen Flachkopf 30 und einen daran anschliessenden federnden Teil 31 aufweist. Das Verschlusselement 29 durchdringt mit dem federnden Teil 31 einen angepassten Durchbruch 32 im Abschirmgeh·ause 26 und greift zugleich in eine angepasste Ausnehmung 33 am Rand der Leiterplatte 27 ein. Da die Federarme 34 des Teils 31 nach dem Einstecken des Verschlusselements 29 hinter dem Rand des Durchbruchs 32 verrasten, wird eine fest mechanische Verbindung zwischen dem Abschirmgeh·ause 26 und der Leiterplatte 27 hergestellt. Beim Drehen des Verschlusselements 29 mit Hilfe eines Schraubenziehers oder ·ahnlichen Werkzeuges wird diese mechanische Verbindung gel·ost, indem der Flcchkopf 30 durch Schneid- oder Scherwirkung abgetrennt wird.

Ausserdem kann das Abschirmgeh·ause 26 an seiner der Ger·ater·uckwand zugewandten Seite eine Einrichtung 38 zum Anzeigen einer fehlerhaften Funktion der Funktionsgruppe tragen. Eine solche Einrichtung kann darin bestehen, dass eine Leuchtdiode anzeigt, wenn die Funktionsgruppe nicht mehr einwandfrei arbeitet.
GRUNDIG SUPER COLOR 8285 CHASSIS GSC700
GRUNDIG GSC600 GSC700 CHASSIS DEVICE STRUCTURE TECHNOLOGY.
A chassis of a device, for example an electronic device, comprises a support unit made of plastic material which carries the components of the device, such as printed circuit boards, a data storage disk, a ventilator, and a loudspeaker. The components are held in place in corresponding recesses of the chassis by a form-locking connection with the plastic material. The components are carried by the chassis without requiring any fastening elements. For assembling the device, the components are inserted into the lower part of the chassis. Thereafter, the upper part is positioned on top of the lower part. The chassis can be enclosed in a metal enclosure. The chassis is preferably manufactured by a plastic molding process. Ventilation ducts can be provided in the plastic material to ensure cooling of the components.

1. A chassis of a device, the device comprising a plurality of functionally interconnected components disposed in the chassis, the chassis comprising a support unit made of resilient material, the support unit having inner contacting surfaces forming recesses which fit the outer shapes of the components such that the components are held in the support unit by elastic and frictional forces created by the deformation of the inner contacting surfaces by an exterior surface of the components disposed in corresponding recesses.
2. A chassis of a device, the device comprising a plurality of functionally interconnected components disposed in the chassis, the chassis comprising a support unit made of deformable material, the support unit having inner contacting surfaces forming recesses, the recesses fitting the outer shape of the corresponding components such that the components are held in the support unit by elastic and frictional forces created by the substantially continuous deformation of an inner contacting surface by an exterior surface of the component disposed in a corresponding recess.
The invention relates to a chassis of a device, such as a computer or electronic instrument, for receiving the components of the device. The components which are typically mounted to such a chassis, in particular with electronic devices, are printed circuit boards, storage disks, ventilators, loudspeakers etc. The chassis has the purpose to hold, mechanically stable, the individual components at a fixed location inside the device.
BACKGROUND OF THE INVENTION
A chassis according to the prior art typically comprises a framework having several partitions to which the components are mounted. The framework itself is also fastened to the outer housing of the device. The manufacture of a prior art chassis and housing is a comparatively complicated and time-consuming process. For the manufacture of a metal chassis, metal sheets have to be stamped and bent. Thereafter, the surfaces of the sheets are treated, for example by galvanizing, then the sheets are connected to each other by a suitable connection technique, such as riveting, screwing, welding, or gluing. Finally, the components are connected to the chassis by fastening elements like screws or rivets or other connection techniques. It is also known to use parts of hard plastic for a chassis, but also in this case, the assembly is complicated and time-consuming since fastening elements have to be mounted to the chassis, for example by ultrasound welding, gluing, or pressing. Furthermore, electromagnetic shielding arrangements have to be provided by covering plastic parts with the conductive material and/or by fastening metal plates or foils to the chassis. Often, additional holding components, for instance angle plates, are required to hold a component at the desired position in the device. In summary, prior art chassis have a mechanically complicated structure and involve a time-consuming procedure for the manufacture of the chassis and for the assembly of the components on the chassis. In particular, known chassis require the use of mounting tools, such as screw drivers, bending tools, riveting tools, or welding tools which make the assembly costly.

According to the invention, the chassis comprises a support unit of plastic material having recesses which fit the outer shapes of the components, respectively, with the components being held in said support unit in a substantially form-locking manner without requiring fastening elements, and with the components being enclosed by said support unit when inserted therein.
According to an underlying principle of the invention, the chassis which holds the components of the device is completely made of plastic material and furnished with recesses into which the components fit in a form-locking manner. The components are thus held in place by the form-fitting connection to the plastic material without requiring any fastening elements like screws or rivets or clamps or snap-fits or any connection technique like welding, soldering, gluing or other permanent connection technique. The assembly of the device is simply performed by inserting the individual components into the corresponding recesses. Consequently, the assembly process is substantially simplified as compared with prior art devices where the components have to be fastened to the chassis with fastening elements. In particular, the assembly process does not require special tools; the assembly can be performed manually just by putting the individual components into the corresponding recesses. Furthermore, the assembly time is substantially reduced relative to the prior art.
The present invention has, among others, the following additional advantages:

The requirements regarding manufacturing tolerances are smaller than in a prior art chassis wherein the parts which are to be assembled have to be manufactured with great precision to ensure accurate joining of the various parts. In the invention, however, since there is only one (or two) part(s), manufacturing tolerances are not of such an importance.
The components can easily be inserted into the chassis from one direction, preferably from above (in the direction of gravity), no complicated three-dimensional movements for positioning the components at their places in the chassis are required. Thus, the assembly process can be fully automated, using, for example, an assembly robot.
For assembling the chassis, no assembly instructions are required since the assembly process is self-explaining as the shapes of the recesses in the chassis correspond to the contours of the components to be inserted.
The weight of the chassis is substantially reduced relative to conventional chassis. According to a practical example, the weight can be reduced by a factor of 15-20.
The chassis provides for good acoustical insulation, since it surrounds any noise generating components.
Air ducts can be formed in the chassis such that a concentrated air stream can be directed to any heat generating components and thus provide for efficient cooling.
The components in the device are protected from mechanical shocks or vibrations since the chassis material has a damping function.
Due to the shock-absorbing function of the chassis, the requirements regarding shock-proof packing of the device during transportation are reduced. Consequently, a great amount of packing material during transportation can be saved, resulting in a smaller transport volume and reduction of potentially ecologically damaging materials.
The disassembly is as simple and easy as the assembly, which is advantageous for a quick and simple exchange of defective components.
The chassis does not have sharp edges or corners, thus reducing the risk of injuries.
Even though it is known in connection with an electronic device (Hewlett-Packard Model No. HP 8118A "Pulse Pattern Generator") to surround the ventilator for cooling certain electronic components with an enclosure made of polyurethane foam, this prior art is based on a different concept than the present invention: The purpose of the polyurethane casing is to absorb the sound generated by the ventilator. The remaining components of this known device are fastened to the metal chassis in the conventional manner using fastening elements. This prior art has therefore no relationship to the concept of the present invention to use the plastic material as a load-bearing structure for all components of the device.

If the chassis carries electronic components, it is preferred to provide the chassis with electrically conductive material to avoid electrostatic charging.
In a preferred embodiment of the invention, the chassis is manufactured in a fast and cost-effective way by molding from a plastic material which can be foamed. In that way, all recesses for receiving the components can be manufactured by a single forming step. At the same time, it is possible to form ventilation ducts. An alternative for cooling could be to provide a tube system in the chassis for circulation of a cooling agent and a heat exchanger for dissipating heat from the cooling agent. The tube system could simply be embodied as channels molded in the plastic material of the chassis.
The recesses for receiving the components can be provided in different planes, one above the other, so that the components can be arranged not only one beside the other, but also one above the other. This permits a space-saving arrangement of the components.
An advantageous plastic material is expanded polypropylene. It is a lightweight material, can be readily molded into various shapes, is shock-absorbing and yet has dimensional stability. Furthermore, polypropylene is temperature-stable and chemically resistant. Also, it can be completely recycled and is thus economically beneficial. A further contribution to environmental pr













The aim of this article has been to provide a general guide to servicing rather than to list faults common to particular models. Much useful information on individual
chassis with thyristor line output stages has appeared in previous issues of Obsolete Technology Tellye !- refer to the following as required: Search with the tag Thyristors at the bottom of the post to select all posts with this argument on various fabricants.
GRUNDIG SUPER COLOR W8285 CHASSIS GSC700 THYRISTOR (LINE / HORIZONTAL) DEFLECTION OVERVIEW.
Horizontal deflection circuit




Description:
1. A horizontal deflection circuit for generating the deflection current in the deflection coil of a television picture tube wherein a first switch controls the horizontal sweep, and wherein a second switch in a so-called commutation circuit with a commutating inductor and a commutating capacitor opens the first switch and, in addition, controls the energy transfer from a dc voltage source to an input inductor, characterized in that the input inductor (Le) and the commutating inductor (Lk) are combined in a unit designed as a transformer (U) which is proportioned so that the open-circuit inductance of the transformer is essentially equal to the value of the input inductor (Le), while the short-circuit inductance of the transformer (U) is essentially equal to the value of the commutating inductor (Lk), and that the second switch (S2) is connected in series with the dc voltage source (UB) and a first winding (U1) of the transformer (U). 2. A horizontal deflection circuit according to claim 1, characterized in that the transformer (U) operates as an isolation transformer between the supply (UB) and the subcircuits connected to a second
winding. 3. A horizontal deflection circuit according to claim 1, characterized in that the second switch (S2) is connected between ground and that terminal of the first winding (U1) of the transformer (U) not connected to the supply potential (+UB). 4. A horizontal deflection circuit according to claim 1, characterized in that a capacitor (CE) is connected across the series combination of the first winding (U1) of the transformer and the second switch (S2). 5. A horizontal deflection circuit according to claim 1, characterized in that the second winding (U2) of the transformer (U) is connected in series with a first switch (S1), the commutating capacitor (Ck), and a third, bipolar switch (S3) controllable as a function of the value of a controlled variable developed in the deflection circuit. 6. A horizontal deflection circuit according to claim 5, characterized in that the third switch (S3) is connected between ground and the second winding (U2) of the transformer. 7. A horizontal deflection circuit according to claim 2, characterized in that the isolation transformer carries a third winding via which power is supplied to the audio output stage of the television set. 8. A horizontal deflection circuit according to claims 2, characterized in that the voltage serving to control the first switch (S1) is derived from a third winding of the transformer.
German Auslegeschrift (DT-AS) No. 1,537,308 discloses a horizontal deflection circuit in which, for generating a periodic sawtooth current within the respective deflection coil of the picture tube, in a first branch circuit, the deflection coil is connected to a sufficiently large capacitor serving as a current source via a first controlled, bilaterally conductive switch which is formed by a controlled rectifier and a diode connected in inverse parallel. The control electrode of the rectifier is connected to a drive pulse source which renders the switch conductive during part of the sawtooth trace period. In that arrangement, the sawtooth retrace, i.e. the current reversal, also referred to as "commutation", is initiated by a second controlled switch.
The first controlled switch also forms part of a second branch circuit where it is connected in series with a second current source and a reactance capable of oscillating. When the first switch is closed, the reactance, consisting essentially of a coil and a capacitor, receives energy from the second current source during a fixed time interval. This energy which is taken from the second current source corresponds to the circuit losses caused during the previous deflection cycle.
As can be seen, such a circuit needs two different, separate inductive elements, it being known that inductive elements are expensive to manufacture and always have a certain volume determined by the electrical properties required.
The object of the invention is to reduce the amount of inductive elements required.
The invention is characterized in that the input inductor and the commutating inductor are combined in a unit designed as a transformer which is proportioned so that the open-circuit inductance of the transformer is essentially equal to the value of the input inductor, while the short-circuit inductance of the transformer is essentially equal to the value of the commutating inductor, and that the second switch is connected in series with the dc voltage source and a first winding of the transformer.
This solution has an added advantage in that, in mass production, both the open-circuit and the short-circuit inductance are reproducible with reliability.
According to another feature of the invention, the electrical isolation between the windings of the transformer is such that the transformer operates as an isolation transformer between the supply and the subcircuits connected to a second winding or to additional windings of the transformer. In this manner, the transformer additionally provides reliable mains isolation.
According to a further feature of the invention, the second switch is connected between ground and that terminal of the first winding of the transformer not connected to the supply potential. This simplifies the control of the switch.
According to a further feature of the invention, to regulate the energy supply, the second winding of the transformer is connected in series with the first switch, the commutating capacitor, and a third, bipolar switch controllable as a function of the value of a controlled variable developed in
the deflection circuit.
The advantage gained by this measure lies in the fact that the control takes place on the side separated from the mains, so no separate isolation device is required for the gating of the third switch. Further details and advantages will be apparent from the following description of the accompanying drawings and from the claims. In the drawings,
FIG. 1 is a basic circuit diagram of the arrangement disclosed in German Auslegeschrift (DT-AS) No. 1,537,308;
FIG. 2 shows a first embodiment of the horizontal deflection circuit according to the invention, and
FIG. 3 shows a development of the horizontal deflection circuit according to the invention.
FIG. 1 shows the essential circuit elements of the horizontal deflection circuit known from the German Auslegeschrift (DT-AS) No. 1,537,308 referred to by way of introduction.
Connected in series with a dc voltage source UB is an input inductor Le and a bipolar, controlled switch S2. In the following, this switch will be referred to as the "second switch"; it is usually called the "commutating switch" to indicate its function.
In known circuits, the second switch S2 consists of a controlled rectifier and a diode connected in inverse parallel.
The second switch S2 also forms part of a second circuit which contains, in addition, a commutating inductor Lk, a commutating capacitor Ck, and a first switch S1. The first switch S1, controlling the horizontal sweep, is constructed in the same manner as the above-described second switch S2, consisting of a controlled rectifier and a diode in inverse parallel. Connected in parallel with this first switch is a deflection-coil arrangement AS with a capacitor CA as well as a high voltage generating arrangement (not shown). In FIGS. 1, 2, and 3, this arrangement is only indicated by an arrow and by the reference characters Hsp. The operation of this known horizontal deflection circuit need not be explained here in detail since it is described not only in the German Auslegeschrift referred to by way of introduction, but also in many other publications.
FIGS. 2 and 3 show the horizontal deflection circuit modified in accordance with the present invention. Like circuit elements are designated by the same reference characters as in FIG. 1.
FIG. 2 shows the basic principle of the invention. The two inductors Le and Lk of FIG. 1 have been replaced by a transformer U. To be able to serve as a substitute for the two inductors Le and Lk, the transformer must be proportioned in a special manner. Regardless of the turns ratio, the open-circuit inductance of the transformer is chosen to be essentially equal to the value of the input inductor Le, and the short-circuit inductance of the transformer is essentially equal to the value of the commutating inductor Lk.
To permit the second switch S2 to be utilized for the connection of the dc voltage source UB, it is included in the circuit of that winding U1 of the transformer connected to the dc voltage UB.
In principle, it is of no consequence for the operation of the switch S2 whether it is inserted on that side of the winding U1 connected to the positive operating potential +UB or on the side connected to ground. In practice, however, the solution shown in FIGS. 2 and 3 will be chosen since the gating of the controlled rectifier is less problematic in this case.
In compliance with pertinent safety regulations, the transformer U may be designed as an isolation transformer and can thus provide mains separation, which is necessary for various reasons. It is known from German Offenlegungschrift (DT-OS) No. 2,233,249 to provide dc isolation by designing the commutating inductor as a transformer, but this measure is not suited to attaining the object of the present invention.
If the energy to be taken from the dc voltage source is to be controlled as a function of the energy needed in the horizontal deflection circuit and in following subcircuits, the embodiment of the horizontal deflection circuit of FIG. 3 may be used.
The circuit including the winding U2 of the transformer U contains a third controlled switch S3, which, too, is inserted on the grounded side of the winding U2 for the reasons mentioned above. This third switch S3, just as the second switch S2, is operated at the frequency of a horizontal oscillator HO, but a control circuit RS whose input l is fed with a controlled variable is inserted between the oscillator and the switch S3. Depending on this controlled variable, the controlled rectifier of the third switch S3 can be caused to turn on earlier. A suitable controlled variable containing information on the energy consumption is, for example, the flyback pulse capable of being taken from the high voltage generating circuit (not shown). Details of the operation of this kind of energy control are described in applicant's German Offenlegungsschrift (DT-OS) No. b 2,253,386 and do not form part of the present invention.
With mains isolation, the additional, third switch S3 shown here has the advantage of being on the side isolated from the mains and eliminates the need for an isolation device in the control lead of the controlled rectifier.
As an isolation transformer, the transformer U may also carry additional windings U3 and U4 if power is to be supplied to the audio output stage, for example; in addition, the first switch S1 may be gated via such an additional winding.
The points marked at the windings U1 and U2 indicate the phase relationship between the respective voltages. Connected in parallel with the winding U1 and the second switch S2 is a capacitor CE which completes the circuit for the horizontal-frequency alternating current; this serves in particular to bypass the dc voltage source or the electrolytic capacitors contained therein.
If required, a well-known tuning coil may be inserted, e.g. in series with the second winding U2, without changing the basic operation of the horizontal deflection circuit according to the invention.
GRUNDIG SUPER COLOR W8285 CHASSIS GSC700 Electron beam deflection circuit including thyristors Further Discussion and deepening of knowledge, Thyristor horizontal output circuits GRUNDIG CHASSIS GSC700:
1. An electron beam deflection circuit for a cathode ray tube with electromagnetic deflection by means of a sawtooth current waveform having a trace portion and a retrace portion, said circuit comprising: a deflection winding; a first source of electrical energy formed by a first capacitor; first controllable switching means comprising a parallel combination of a first thyristor and a first diode connected together to conduct in opposite directions, for connecting said winding to said first source during said trace portion, while said first switching means is turned on; a second source of electrical energy including a first inductive energy storage means coupled to a voltage supply; reactive circuit means including a combination of inductive and capacitive reactances for storing the energy supplied by said second source; second controllable switching means, substantially similar to said first one, for completing a circuit including said reactive circuit means and said first switching means, when turned on before the end of said trace portion, so as to pass through said first switching means an oscillatory current in opposite direction to that which passes through said first thyristor from said first source and to turn said first thyristor off after these two currents cancel out, the oscillatory current flowing thereafter through said first diode for an interval termed the circuit turn-off time, which has to be greater than the turn-off time of said first thyristor; wherein the improvement comprises: means for drawing, during at least a part of said trace portion, a substantial amount of additional current through said first switching means, in the direction of conduction of said first diode, whereby to perceptibly shift the waveform of the current flowing through said first switching means towards the negative values by an amount equal to that of said substantial additional current and to lengthen, in proportion thereto, said circuit turn-off time, without altering the values of the reactances in the reactive circuit which intervene in the determination of both the circuit turn-off and retrace portion time intervals.

2. A deflection circuit as claimed in claim 1, wherein said amount of additional current is greater than or equal to 5 per cent of the peak-to-peak value of the current flowing through the deflection winding.
3. A deflection circuit as claimed in claim 1, wherein said means for drawing a substantial amount of additional current through said first switching means comprises a resistor connected in parallel to said first capacitor.
4. A deflection circuit as claimed in claim 1, wherein said means for drawing an additional current is formed by connecting said first and second energy sources in series so that the current charging said reactive circuit means forms the said additional current.
5. A deflection circuit as claimed in claim 1, further including a series combination of an autotransformer winding and a second high-value capacitor, said combination being connected in parallel to said first switching means, wherein said autotransformer comprises an intermediate tap located between its terminals respectively connected to said first switching means and to said second capacitor, said tap delivering, during said trace portion, a suitable DC supply voltage lower than the voltage across said second capacitor; and wherein said means for drawing a substantial amount of additional current comprises a load to be fed by said supply voltage and having one terminal connected to ground; and further controllable switching means controlled to conduct during at least part of said trace portion and to remain cut off during said retrace portion, said further switching means being connected between said tap and the other terminal of said load.

A undirectional reverse blocking triode type thyristor or silicon controlled rectifier (SCR), such as that used in the aformentioned circuit, requires a certain turn-off time between the instant at which the anode current ceases and the instant at which a positive bias may be applied to it without turning it on, due to the fact that there is still a high concentration of free carriers in the vicinity of the middle junction, this concentration being reduced by a process of recombination independently from the reverse polarity applied to the thyristor. This turn-off time of the thyristor is a function of a number of parameters such as the junction temperature, the DC current level, the decay time of the direct current, the peak level of the reverse current applied, the amplitude of the reverse anode to cathode voltage, the external impedance of the gate electrode, and so on, certain of these varying considerably from one thyristor to another.
In horizontal deflection circuits for television receivers, the flyback or retrace time is limited to approximately 20 percent of the horizontal scan period, the retrace time being in the case of the CCIR standard of 625 lines, approximately 12 microseconds and, in the case of the French standard of 819 lines, approximately 9 microseconds. During this relatively short interval, the thyristor has to be rendered non-conducting and the electron beam has to be returned to the origin of the scan. The first thyristor is blocked by means of a series resonant LC circuit which is subject to a certain number of restrictions (limitations as to the component values employed) due to the fact that, inter alia, it simultaneously determines the turn-off time of the circuit which blocks the thyristor and it forms part of the series resonant circuit which is to carry out the retrace. To obtain proper operation of the deflection circuit of the aforementioned Patent, especially when used for the French standard of 819 lines per image, the values of the components used have to subject to very close tolerances (approximately 2%), which results in high costs.
The improved deflection circuit, object of the present invention, allows the lengthening of the turn-off time of the circuit for turning the scan thyristor off, without altering the values of the LC circuit, which are determined by other criteria, and without impairing the operation of the circuit.

A further object of the invention consists in using the supplementary current in the recovery diode of the first switching means to produce a DC voltage which may be used as a power supply for the vertical deflection circuit of the television receiver, for example.
The invention will be better understood and other features and advantages thereof will become apparent from the following description and the accompanying drawings, given by way of example, and in which:
FIG. 1 is a schematic circuit diagram partially in bloc diagram form of a prior art deflection circuit according to the aforementioned Patent;

FIG. 3 is a schematic diagram of a deflection circuit according to the invention which allows the principle of the improvement to be explained;
FIG. 4 is a diagram of the waveforms of the current through the first switching means 4, 5 of the circuit of FIG. 3;
FIG. 5 is a circuit diagram of another embodiment of the circuit according to the invention;
FIG. 6 is a schematic representation of the preferred embodiment of the circuit according to the invention; and
FIG. 7 shows voltage waveforms at various points of the high voltage autotransformer 21 of FIG. 6.
In all these Figures the same reference numerals refer to the same components.

The deflection circuit also includes a drive stage for this final stage which here controls the turning off of the first thyristor 4 to produce the retrace or fly-back portion of the scan during the line-blanking intervals i.e. while the picture signal is not transmitted. This driver stage comprises a second voltage source in the shape of a DC power supply 6 which delivers a constant high voltage E. The negative terminal of the power supply 6 is connected to ground and its positive terminal to one of the terminals of a second inductance 7 of relatively high value, which draws a substantially lineraly varying current from the power supply 6 to avoid its overloading. The other terminal of the second inductance 7 is connected, on the one hand, to the junction of the deflection winding 1 and the first switching means 3 by means of a second inductance 8 and a second capacitor 9 in series and, on the other hand, to one of the terminals of a second controllable bi-directionally conducting switching means 10, similar to the first one 3, including a parallel combination of a second thyristor 11 and a second recovery diode 12 also arranged to conduct in opposite directions.
The respective values of the third inductance 8 (L 8 ) and of the second capacitor 9 (C 9 ) are principally selected so that, on the one hand, one half-cycle of oscillation of the first series resonant circuit L 8 - C 9 , (i.e. π √ L 8 . C 9 ) is longer than the turn-off time of the first thyristor 4, but still is as short as possible since this time interval determines the speed of the commutation of the thyristor 4, and, on the other hand, one half-cycle of oscillation of another series resonant circuit formed by L 1 , L 8 and C 9 , i.e. π √ (L 1 + L 8 ) . C 9 , is substantially equal to the required retrace time interval (i.e. shorter than the horizontal blanking interval).
T
he gate (control electrode) of the second thyristor 11 is coupled to the output of the horizontal oscillator 13 of the television receiver by means of a first pulse transformer 14 and a first pulse shaping circuit 15 so that it is fed short triggering pulses which are to turn it on.
The gate of the first thyristor 4 fed with signals of a substantially rectangular waveform which are negative during the horizontal blanking intervals, is coupled to a winding 16 by means of a second pulse shaping circuit 17, the winding 16 being magnetically coupled to the second inductance 7 to make up the secondary winding of a transformer of which the inductance 7 forms the primary winding. It will be noted here that it is also possible to couple the secondary winding 16 magnetically to a primary winding connected to a suitable output (not shown) of the horizontal oscillator 13.
The operation of a circuit of this type will be explained below with reference to FIG. 2 which shows the waveforms at various points in the circuit of FIG. 1 during approximately one line period.

Waveform A shows the form of the current i L1 passing through deflection winding 1, this current having a sawtooth waveform substantially linear from t 0 to t 3 and from t 5 to t 7 , and crossing zero at time instants t 0 and t 7 , and reaching values of + I 1m and - I 1m , at time instants t 3 and t 5 respectively, these being its maximum positive and negative amplitudes.
During the second half of the trace portion of the horizontal deflection cycle, that is to say from t 0 to t 3 , the thyristor 4 of the first switching means 3 is conductive and makes the high value capacitor 2 discharge through the deflector winding 1, which has a high inductance, so that current i L1 increases linearly.
A few microseconds (5 to 8 μ s) before the end of the trace portion, i.e. at time instant t 1 , the trigger of the second thyristor 11 receives a short voltage pulse V G11 which causes it to turn on as its anode is at this instant at a positive potential with respect to ground, which is due to the charging of the second capacitor 9 through inductances 7 and 8 by the voltage E from the power supply 6.
When thyristor 11 is made conductive at time t 1 , on the one hand, inductance 7 is connected between ground and the voltage source 6 and a linearly increasing current flows through it and, on the other hand, the reactive circuit 8, 9 forms a loop through the second and first switching means 10 and 3, thus forming a resonant circuit which draws an oscillatory current i 8 ,9 of frequency ##EQU1##
This oscillatory current i 8 ,9 will pass through the first switching means 3, i.e. thyristor 4 and diode 5, in the opposite direction to that of current i L1 . Since the frequency f 1 is high, current i 8 ,9 will increase more rapidly than i L1 and will reach the same level at time t 2 , that is to say i 8 ,9 (t 2 ) = -i L1 (t 2 ) and these currents will cancel out in the thyristor 4 in accordance with the well known principle of forced commutation. After time instant t 2 , current i 8 ,9 continues to increase more rapidly than i L1 , but the difference between them (i 8 ,9 - i L1 ) passes the diode 5 (see wave form B) until it becomes zero at time instant t 3 which is the turn off time instant of the first switching means 3, at which the retrace begins.
The interval between the time instant t 2 and t 3 , i.e. (t 3 -t 2 ), during which diode 5 is conductive and the thyristor is reverse biased will be termed in what follows the circuit turn-off time and it should be greater than the turn-off time of the thyristor 4 itself since the latter will subsequently become foward biased (i.e. from t 3 to t 5 ) by the retrace or flyback pulse (see waveform E) which should not trigger it.
At time instant t 3 , the switching means 3 is opened (i 4 and i 5 are both zero -- see waveforms B and C) and the reactive circuit 8, 9 forms a loop through capacitor 2 and the deflection coil 1 and thus a series resonant circuit including (L 1 + L 8 ) and C 9 , C 2 being of high value and representing a short circuit for the flyback frequency ##EQU2## thus obtained.
The retrace which stated at time t 3 takes place during one half-cycle of the resonant circuit formed by reactances L 1 , L 8 and C 9 , i.e. during the interval between t 3 and t 5 . In the middle of this interval i.e. at time instant t 4 , both i L1 (waveform A) and i 8 ,9 (waveform D) pass through zero and change their sign, whereas the voltage at the terminals of the first switching means 3 (V 3 , waveform E) passes through a maximum. Thus, from t 4 onwards, thyristor 11 will be reverse biased and diode 12 will conduct the current from the resonant circuit 1, 8 and 9 in order to turn the second thyristor 11 off.
At time instant t 5 , when current i L1 has reached - I 1m and when voltage v 3 falls to zero, diode 5 of the first switching means 3 becomes conductive and the trace portion of scan begins.
Current i 8 ,9 nevertheless continues to flow in the resonant circuit 8, 9 through diodes 5 and 12, which causes a break to appear in waveform D at t 5 , and a negative peak to appear in waveform D and a positive one in waveform B in the interval between t 5 and t 6 , these being principally due to the distributed capacities of coil 1 or to an eventual capacitor (not shown) connected in parallel to the first switching means 3.
At time instant t 6 , diode 12 of the second switching means 10 ceases to conduct after having allowed thyristor 11 time to become turned off completely.
The level of current i 8 ,9 at time instant t 5 (i.e. I c ) as well as the negative peak I D12 in i 8 ,9 and the positive peak I D5 in i 5 depend on the values of L 8 and C 9 in the same way as does the turn-off time of the circuit (t 3 - t 2 ). If, for example, L 8 and C 9 , are increased I D5 increases towards zero and this could cause diode 5 to be cut off in an undesirable fashion. I c also increases towards zero, which is liable to cause diode 12 to be blocked and thyristor 11 to trigger prematurely.
From the foregoing it can be clearly seen that the choice of values for L 8 and C 9 is subject to four limitations which prevent the values from being increased to lengthen the turn-off time of the driver circuit of first switching thyristor 4 so as to forestall its spurious triggering.
Waveform F shows the voltage v G4 obtained at the gate of thyristor 4 from the secondary winding 16 coupled to the inductor 7. This voltage is positive from t 0 to t 1 and from t 6 to t 7 and is negative between t 2 and t 6 i.e. while the second switching means 10 is conducting.
The present invention makes the lengthening of the turn-off time of thyristor 4 possible without altering the parameters of the circuit such as inductance 8 and capacitor 9.

In FIG. 4, the broken lines show the waveform of the current in the first switch device 3 in the circuit of FIG. 1, this waveform being produced by adding waveforms B and C of FIG. 2. The current i 4 above the axis flows through thyristor 4 and current i 5 below the axis flows through diode 5. When the capacitance C 20 of the capacitor in series with the deflector coil is increased to some tens of microfarads (C 2 having been of the order of 1 μ F) and when there is connected in parallel with capacitor 20 a resistor 18 the value of which is calculated to draw a strong current I R18 from capacitor 20, that is to say a current at least equal to 0,1 I m (I m being of the order of some tens of amperes), current I R18 is added to that i 5 which flows through diode 5 without in any way altering the linearity of the trace portion nor the oscillatory commutation of thyristor 4 which is brought about by the resonant circuit L 8 , C 9 .
The fact of loading capacitor C 20 by means of a resistor 18 thus has the effect of permanently displacing the waveform of the current in the negative direction by I R18 . Thus, during the trace portion of the scan, the transfer of the current from the diode 5 to the thyristor 4 begins at time t 10 instead of t 0 , that is to say with a delay proportional to I R18 . The effect of the triggering pulse delivered by the horizontal oscillator (13 FIG. 1) to the second thyristor 11 at time instant t 1 , will be to start the commutation process of the first thyristor 4 when the current it draws is less by I R18 than that i 4 (t 1 ) which it would have been drawing had there been no resistor 18.
Because of this, the turn-off time of the thyristor 4 proper, which as has been mentioned increases with the maximum current level passing throught it, is slightly reduced. Moreover, because the oscillatory current i 8 ,9 (FIG. 2) from circuit L 8 , C 9 which flows through thyristor 4 in the opposite direction is unchanged, it reaches a value equal to that of the current i L1 (FIG. 1) flowing in the coil 1 in a shorter time, that is to say at time t 12 . Diode 5 will thus take the oscillatory current i 8 ,9 (FIG. 2) over in advance with respect ro time instant t 2 and will conduct it until it reaches zero value at a time instant t 13 later than t 3 , the amounts of advance (t 2 - t 12 ) and delay (t 13 - t 3 ) being practically equal.

It should be noted at this point that the current I R18 produces a voltage drop at the terminals of the resistor the only effect of which is to heat up the resistor since the level of this voltage (40 to 60 volts) does not necessarily have a suitable value to be used as a voltage supply for other circuits in an existing transistorised television receiver.
In accordance with one embodiment of the invention, illustrated in FIG. 5, an application is proposed for the additional current which is to be drawn through diode 5. In FIG. 5, the positive terminal of capacitor 20 is connected by a conductor 19 to the negative pole of the power supply 6 and the voltage at the terminals of capacitor 20 is thus added to that E from the source 6.
In the preferred embodiment of the present invention, which is shown in FIG. 6, it is possible to cause a supplementary current of a desired value to flow through the first diode 5 while obtaining a voltage which has a suitable value for use in another circuit in the television receiver.
If the voltage at the terminals of capacitor 20 in FIG. 3 is not a usable value, it is possible to connect in parallel with the series circuit comprising the deflector coil 1 and the capacitor 2 in FIG. 1, i.e. in parallel with the terminals of the first switching means 3, a series combination of an autotransformer 21 and a high value capacitor 22 (comparable with capacitor 20 in FIGS. 3 and 5). The autotransformer 21 has a tap 23 is suitably positioned between the terminal connected to capacitor 22 at the tap 24 connected to the first switching means 3. This autotransformer 21 may be formed by the one conventionally used for supplying a very high voltage to the cathode ray tube, as described for example in U.S. Pat. No. 3,452,244; such a transformer comprises a voltage step-up winding between taps 24 and 25, which latter is connected to a high voltage rectifier (not shown).
The waveform of the voltage at the various points in the autotransformer is shown in FIG. 7, in which waveform A shows the voltage at the terminals of capacitor 22, waveform B the voltage at tap 24 and waveform C the voltage at tap 23 of the autotransformer 21.
The voltage V c22 at the terminals of capacitor 22 varies slightly about a mean value V cm . It is increasing while diode 5 is conducting and decreasing during the conduction of the thyristor 4.
The voltage v 24 at tap 24 follows substantially the same curve as waveform E in FIG. 2, that is to say that during the retrace time interval from t 13 to t 5 to a positive pulse called the flyback pulse is produced and, during the time interval while the first switching means 3 is conducting, the voltage is zero. The mean valve of the voltage v 24 at tap 24 of the auto-transformer 21 is equal to the mean value V cm of the voltage at the terminals of capacitors 2 and 22.
Thus, there is obtained at tap 23 a waveform which is made up, during the retrace portion, of a positive pulse whose maximum amplitude is less than that of v 24 at tap 24 and, during the trace portion, of a substantially constant positive voltage, the level V of which is less than the mean value V cm of the voltage v c22 at the terminals of capacitor 22. By moving tap 23 towards terminals 24 the amplitude of the pulse during fly-back increases while voltage V falls and conversely by moving tap 23 towards capacitor 22 voltage V increases and the amplitude of the pulse drops.
In more exact terms, the voltage V at tap 23 is such that the means value of v 23 is equal to V cm . It has thus been shown that by choosing carefully the position of tape 23, a voltage V may be obtained during the trace portion of the scan, which may be of any value between V cm and zero.
This voltage V is thus obtained by periodically controlled rectification during the trace portion of the scan. For this purpose an electronic switch is used to periodically connect the tap 23 of trnasformer winding 21 to a load. This switch is made up of a power transistor 26 whose collector is connected to tap 23 and the emitter to a parallel combination formed by a high value filtering capacitor 27 and the load which it is desired to supply, which is represented by a resistor 28. The base of the transistor 26 receives a control voltage to block it during retrace and to unblock it during the whole or part of the trace period. A control voltage of this type may be obtained from a second winding 29 magnetically coupled to the inductance 7 of the deflection circuit and it may be transmitted to the base of transistor 26 by means of a coupling capacitor 30 and a resistor 31 connected between the base and the emitter of transistor 26.
It may easily be seen that the DC collector/emitter current in transistor 26 flows through the first diode 5 of the first switching means 3 via a resistor 28 and the part of the winding of auto-transformer 21 located between taps 23 and 24.
Experience has shown that a circuit as shown in FIG. 6 can supply 24 volts with a current of 2 amperes to the vertical deflection circuit of the same television set, the voltage at the terminals of capacitor 22 being from 50 to 60 volts.
It should be mentioned that, when the circuit which forms the load of the controlled rectifier 26, 27 does not draw enough current to sufficiently lengthen the circuit turn-off time T R , an additional resistor (not shown) may be connected between the emitter of transistor 26 and ground or in parallel to capacitor 22, which resistor will draw the additional current required.
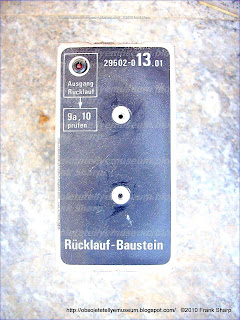



GRUNDIG SUPER COLOR W8285 CHASSIS GSC700 Gating circuit for television SCR deflection system AND REGULATION / stabilization of horizontal deflection NETWORK CIRCUIT with Transductor reactor / Reverse thyristor energy recovery circuit.In a television deflection system employing a first SCR for coupling a deflection winding across a source of energy during a trace interval of each deflection cycle and a second SCR for replenishing energy to the source of energy during a commutation interval of each deflection cycle, a gating circuit for triggering the first SCR. The gating circuit employs a voltage divider coupled in parallel with the second SCR which develops gating signals proportional to the voltage across the second SCR.

1. In a television deflection system in which a first switching means couples a deflection winding across a source of energy during a trace interval of each deflection cycle and a second switching means replenishes energy to said source of energy during a commutation interval of each deflection cycle, a gating circuit for said first switching means, comprising:
capacitive voltage divider means coupled in parallel with said second switching means for developing gating signals proportional to the voltage across said second switching means; and
means for coupling said voltage divider means to said first switching means to provide for conduction of said first switching means in response to said gating signals.
2. A gating circuit according to claim 1 wherein said voltage divider includes first and second capacitors coupled in series and providing said gating signals at the common terminal of said capacitors. 3. A gating circuit according to claim 2 wherein said first and second capacitors are proportional in value to provide for the desired magnitude of gating signals. 4. A gating circuit according to claim 3 wherein said means for coupling said voltage divider means to said first switching means includes an inductor. 5. A gating circuit according to claim 4 wherein said inductor and said first and second capacitors comprise a resonant circuit having a resonant frequency chosen to shape said gating signal to improve switching of said first switching means.




Various deflection system designs have been utilized in television receivers. One design employing two bidirectional conducting switches and utilizing SCR's (thyristors) as part of the switches is disclosed in U.S. Pat. No. 3,452,244. In this type deflection system, a first SCR is
employed for coupling a deflection winding across a source of energy during a trace interval of each deflection cycle, and a second SCR is employed for replenishing energy during a commutation interval of each deflection cycle. The first SCR is commonly provided with gating voltage by means of a separate winding or tap of an input reactor coupling a source of B+ to the second SCR.
Various regulator system designs have been utilized in conjunction with the afore described deflection system to provide for uniform high voltage production as well as uniform picture width with varying line voltage and kinescope beam current conditions.
One type regulator system design alters the amount of energy stored in a commutating capacitor coupled between the first and second SCR's during the commutating interval. A regulator design of this type may employ a regulating SCR and diode for coupling the input reactor to the source of B+. With this type regulator a notch, the width of which depends upon the regulation requirements, is created in the current supplied through the reactor and which notch shows up in the voltage waveform developed on the separate winding or tap of the input reactor which provides the gating voltage for the first SCR. The presence of the notch, even though de-emphasized by a waveshaping circuit coupling the gating voltage to the first SCR, causes erratic control of the first SCR.
SUMMARY OF THE INVENTION

A more detailed description of a preferred embodiment of the invention is given in the following description and accompanying drawing of which:
FIG. 1 is a schematic diagram, partially in block form, of a prior art SCR deflection system;
FIG. 2 is a schematic diagram, partially in block form, of an SCR deflection system of the type shown in FIG. 1 including a gating circuit embodying the invention;
FIG. 3 is a schematic diagram, partially in block form, of one type of a regulator system which employs an SCR as a control device and which is suitable for use with the SCR deflection system of FIG.2;
FIG. 4 is a schematic diagram, partially in block form, of another type of a regulator system suitable for use with the deflection circuit of FIG. 2; and
FIG. 5 is a schematic diagram, partially in block form, of still another type of a regulator system suitable for use with the SCR deflection system of FIG. 2.
DESCRIPTION OF THE PREFERRED EMBODIMENT


An auxiliary winding 38c of transformer 38 is coupled to a high voltage sensing and control circuit 42 which transforms the level of flyback pulses into a pulse width modulated signal. The control circuit 42 is coupled to the regulator network 20.
A horizontal oscillator 44 is coupled to the gate electrode of commutating SCR 14 and produces a pulse during each deflection cycle slightly before the end of the trace interval at T0 of curve 21 to turn on SCR 14 to initiate the commutating interval. The commutating interval occurs between T0 and T3 of curve 21. A resonant waveshaping network 46 comprising a series combination of a capacitor 48 and an inductor 50 coupled between a winding 18b of input choke 18 and the gate electrode of trace SCR 28 and a damping resistor 52 coupled between the junction of capacitor 48 and inductor 50 and ground shapes the signal developed at winding 18b (i.e. voltage waveform 53) to form a gating signal voltage waveform 55 to enable SCR 28 for conduction during the second half of the trace interval occurring between T2 and T1' of curve 41.


A series combination of resistor 22, capacitor 23 and a capacitor 62 is coupled in parallel with commutating switch 12, one terminal of capacitor 62 being coupled to ground. The junction of capacitors 23 and 62 is coupled to the gate electrode of SCR 28 by means of the inductor 50. The resistor 52 is coupled in parallel with capacitor 62.
Capacitors 23 and 62 form a capacitance voltage divider which provides a suitable portion of the voltage across commutating switch 12 for gating SCR 28 via inductor 50. The magnitude of the voltage at the junction of capacitors 23 and 62 is typically 25 to 35 volts. It can, therefore, be seen that the ratio of values of capacitors 23 and 62 will vary depending on the B+ voltage utilized to energize the deflection system. Capacitors 23 and 62 and inductor 50 form a resonant circuit tuned in a manner which provides for peaking of the curve 64 between T4 and T5. This peaking effect further enhances gating of SCR 28 between T4 and T5.
Since the waveshape of the voltage across commutating switch 12 (curve 21) is relatively independent of the type of regulator system employed in conjunction with the deflection system, the curve 64 also is independent of the type of regulator system.
When commutating switch 12 switches off during the interval T3 to T0' curve 21, the voltage across capacitor 62 increases and the voltage at the gate electrode of SCR 28 increases as shown in curve 64. As will be noted, no slump of curve 64 occurs between T3 and T5 because there is no interruption of the voltage across commutating switch 12.






The horizontal deflection circuit 60 produces a flyback pulse in winding 38a of the flyback transformer 38 which is coupled to winding 38c. The magnitude of the pulse on winding 38c determines how long the signal required to switch SCR 66 on is delayed after T4 curve 21 FIG. 1. If the flyback pulse is greater than desirable, the SCR 66 turns on sooner than if the flyback pulse is less than desirable and provides a discharge path for current in commutating capacitor 25 back to the B+ supply. In this manner a relatively constant amplitude flyback pulse is maintained.

Flyback pulse variations are obtained from winding 38c of the horizontal output transformer 38 and applied to a voltage divider comprising resistors 76, 78 and 80 of the high voltage sensing and control circuit 42. A portion of the pulse produced by winding 38c is selected by the position of the wiper terminal on potentiometer 78 and coupled to the base electrode of a transistor 82 by means of a zener diode 84. The emitter electrode of transistor 82 is grounded and a DC stabilization resistor 85 is coupled in parallel with the base-emitter junction of transistor 82. When the pulse magnitude on winding 38c exceeds a level which results in forward biasing the base-emitter junction of transistor 82, current flows from B+ through a resistor 86, a winding 70c of saturable reactor 70 and transistor 82 to ground. Due to the exponential increase of current in winding 70c during the period of conduction of transistor 82, the duration of conduction of transistor 82 determines the magnitude of current flowing in winding 70c and thus the total inductance of windings 70a and 70b. The current in winding 70c is sustained during the remaining deflection period by means of a diode 88 coupled in parallel with winding 70c and poled not to conduct current from B+ to the collector electrode of transistor 82. A capacitor 90 coupled to the cathode of diode 88 provides a bypass for B+. Windings 70a and 70b are in parallel with input reactor 18a and thereby affect the total input inductance of the deflection circuit and thereby controls the transfer of energy to the deflection circuit. The dotted waveforms shown in conjunction with a curve 21' indicate variations from a nominal waveform provided at the input of horizontal deflection circuit 60 by the windings 70a and 70b.



FIG. 5 is a schematic diagram of yet another type of a regulator system which may be used in conjunction with the invention. B+ is coupled through a winding 92a and a winding 92b of a saturable reactor to the horizontal deflection circuit 60. Windings 92a and 92b are used to replace the input choke 18 shown in FIGS. 1 and 2 while also providing for a regulating function corresponding to that provided by regulating network 20.
Flyback pulse variations are obtained from winding 38c and applied to the high voltage sensing and control circuit 42 as in FIG. 4. Current flows from B+ through resistor 86, a winding 92c and transistor 82 to ground. As in FIG. 4 the duration of the conduction of transistor 82 determines the energy stored in winding 92c and thus the total inductance of windings 92a and 92b which control the amount of energy transferred to the deflection circuit during each horizontal deflection cycle. The variations in waveforms of curve 21', shown in conjunction with FIG. 4, are also provided at the input of horizontal deflection circuit 60 by windings 92a and 92b.
For various reasons including cost or performance, a manufacturer may wish to utilize a particular one of the regulators illustrated in FIGS. 3, 4 and 5. Regardless of the choice, the gating circuit according to the invention may be utilized therewith advantageously by providing improved performance and the possibility of cost savings by eliminating taps or extra windings on the wound components which heretofore normally provided a source of SCR gating waveforms.
GRUNDIG SUPER COLOR 8285 CHASSIS GSC700 UNITS VIEW.
TUNER 29502.001.09
IF UNIT 29502.002.01
CHROMA (FARB BAUSTEIN) 29502.004.01
RGB MATRIX (RGB BAUSTEIN) 29502.005.02
SOUND AMPLIFIER (NF BAUSTEIN) 29502.007.01
LINE RETURN (RUECKLAUF BAUSTEIN) 29502.013.01
TRACE SCAN (HINLAUF BAUSTEIN) 29502.014.01
FRAME UNIT (VERTIKAL BAUSTEIN) 29502.011.01
E/W CORRECTION UNIT (OST/WEST BAUSTEIN) 29502.012.01
COMMAND UNIT (STEUER BAUSTEIN) 29502.010.01
SUPPLY UNIT (NETZTEIL BAUSTEIN) 29502.009.01




















The tuning circuits here are Highly sophisticated and complex circuit.
A PLL frequency synthesizer + OSD without a Microprocessor feature and even no ROM chip.
The entire system is based on a complex ASIC from SIEMENS a SM575 toghether with SO356 + SM311 + SO358 + SM577
and 2 TMS3529 (The entire circuit was known as the "GRUNDIG SYNTHESIZER")






























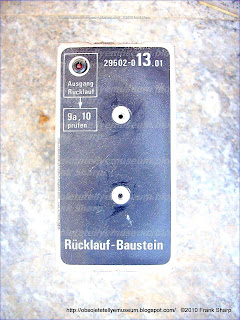
















TDA1082
East-West correction driver circuit
East-West correction driver circuit TDA1082:

GENERAL DESCRIPTION
The TDA1082 is a monolithic integrated circuit driving east-west correction of colour tubes in television receivers.
The circuit can be used for class-A and class-D operation and incorporates the following functions:
· differential input amplifier
· squaring stage
· differential output amplifier with driver stage
· protection stage with threshold
· switching off the correction during flyback
· voltage stabilizer
QUICK REFERENCE DATA
PACKAGE OUTLINE
16-lead DIL; plastic (SOT38); SOT38-1;
Supply voltage (pin 1) VP typ. 12 V
Current consumption IP typ. 17 mA
Total power dissipation Ptot max. 600 mW
Operating ambient temperature range Tamb 0 to + 70 °C
- - - - - - - - - - - - - - - - - - - - - - - - - - - - - - - - -- - - - - - - - - - - - - - - - - - - - - - - - - - - - -










TUNER 29502.001.09
IF UNIT 29502.002.01
CHROMA (FARB BAUSTEIN) 29502.004.01
RGB MATRIX (RGB BAUSTEIN) 29502.005.02
SOUND AMPLIFIER (NF BAUSTEIN) 29502.007.01
LINE RETURN (RUECKLAUF BAUSTEIN) 29502.013.01
TRACE SCAN (HINLAUF BAUSTEIN) 29502.014.01
FRAME UNIT (VERTIKAL BAUSTEIN) 29502.011.01
E/W CORRECTION UNIT (OST/WEST BAUSTEIN) 29502.012.01
COMMAND UNIT (STEUER BAUSTEIN) 29502.010.01
SUPPLY UNIT (NETZTEIL BAUSTEIN) 29502.009.01

TDA3501 VIDEO CONTROL COMBINATION:
The TDA3501 is a monolithic integrated circuit performing the control functions in a PAL/SECAM
decoder which additionally comprises the integrated circuits TDA3510 (PAL decoder) and/or
TDA3520 (SECAM decoder).
The required input signals are: luminance and colour difference —(R-Y) and —(B-Y),
while linear RGB signals can be inserted from an external source.
RGB signals are provided at the output to drive the video output stages.
The TDA3501 has the following features:
- capacitive coupling of the input signals
- linear saturation control
- (G-Y) and RGB matrix insertion possibility of linear RGB signals,
e.g. video text, video games, picture-in-picture, camera or
slidescanner
- equal black level for inserted and matrixed signals by clamping
- 3 identical channels for the RGB signals
- linear contrast and brightness control, operating on both the inserted and matrixed RGB signals
- horizontal and vertical blanking (black and ultra-black respectively) and black-level clamping
obtained via a 3-level sandcastle pulse
- differential amplifiers with feedback-inputs for stabilization of the RGB output stages
- 2 d.c. gain controls for the green and blue output signals (white point adjustment)
- beam current limiting possibility
QUICK REFERENCE DATA
Supply voltage V524 typ. 12 V
Supply current I5 typ. 100 mA
Luminance input signal (peak-to-peak value) V15_24(p_p) typ. 0,45 V
Luminance input resistance R15_24 typ. 12 kfl
Colour difference input signals (peak-to-peak values)
—(B-Y) V1g_24(p_p) typ. 1,33 V
R-Y) V17-24cp-pi tvr>- 1.05 V
Inserted RGB signals (peak-to-peak values) V12,13'-|4_24(p_p) typ. 1 V
Three level sandcastle pulse detector V1Q_24 typ. 2,5/4,5/8,0 V
Control voltage ranges
brightness V2024 I to 3 V
contrast V19_24 2 to 4 V
saturation V16_24 2,1 to 4 V
TDA2593 HORIZONTAL DEFLECTION CONTROL FOR COLOR TV SET
DESCRIPTION
The TDA2593 isa circuit intended for the horizontal
deflectionof color TVsets, suppliedwith transistors
or SCR’S.
.LINE OSCILLATOR(two levels switching)
.PHASE COMPARISON BETWEEN SYNCHRO-
PULSE AND OSCILLATOR VOLTAGE
Ø 1, ENABLED BY AN INTERNAL PULSE,
(better parasitic immunity)
.PHASE COMPARISON BETWEEN THE FLYBACK
PULSES AND THE OSCILLATORVOLTAGE
Ø2
.COINCIDENCE DETECTOR PROVIDING A
LARGE HOLD-IN-RANGE .FILTER CHARACTERISTICS AND GATE
SWITCHING FOR VIDEO RECORDER APPLICATION
.NOISE GATED SYNCHRO SEPARATOR
.FRAME PULSE SEPARATOR
.BLANKING AND SAND CASTLE OUTPUT
PULSES
.HORIZONTAL POWER STAGE PHASE LAGGING
CIRCUIT
.SWITCHING OF CONTROL OUTPUT PULSE
WIDTH
.SEPARATED SUPPLY VOLTAGE OUTPUT
STAGE ALLOWING DIRECT DRIVE OF
SCR’S CIRCUIT .SECURITY CIRCUIT MAKES THE OUTPUT
PULSE SUPPRESSED WHEN LOW SUPPLY
VOLTAGE.



TDA2030 DESCRIPTION
The TDA2030 is a monolithic integrated circuit in
Pentawatt package, intended for use as a low
frequency class AB amplifier. Typically it provides
14W output power (d = 0.5%) at 14V/4Ω;at ± 14V
the guaranteedoutput poweris 12W on a 4Ω load
and 8Won a 8Ω (DIN45500).
TheTDA2030provideshighoutputcurrentandhas
very lowharmonic and cross-over distortion.
Further the device incorporates an original (and
patented) short circuit protection system compris-
ing an arrangement for automatically limiting the
dissipated power so as to keep the working point
of the outputtransistorswithin their safe operating
area.A conventionalthermal shut-downsystem is
also included.
SHORT CIRCUIT PROTECTION
The TDA2030 has an original circuit which limitsthe
current of the output transistors , the maximum output current is a function of the
collector emitter voltage; hence the output transis-
tors work within their safe operating area .
This functioncan thereforebe consideredas being
peak power limiting rather than simple current lim-
iting.
It reducesthe possibility that the devicegetsdam-
aged during an accidental short circuit from AC
output to ground.
Tone Control IC TDA4290
TDA4290-2
Bipolar IC
Tone control IC for the DC voltage control of volume, treble, and bass. The volume characteristic
can be changed from linear to physiological.
For mono application we recommend the TDA 4290-2, while the TDA 4290-2 S is especially
suitable for stereo application.
Features
Few external components
High signal—to—noise ratio
Low total harmonic distortion
Complies with the IEC 268-3 standards
Maximum ratings
Supply voltage V5 18 V
Control inputs V5, V5, V14 0 to vs V
Input signal V8,,“ 3 V
Load current I; 10 mA
Junction temperature 7; 150 “C
Storage temperature range Ts,g -40 to 125 “C
Thermal resistance (sysIem—air) Rm SA 90 K/W
Operating range
Supply voltage vs 10.5 to 18 V
Volume control V5 0 to 0.51 x V2 V
Frequency (—1 dB) fi 20 to 20,000 Hz
Ambienttemperature TA 0 to 70 ‘ “C
Current consumption Is 35 50 I mA
Relerence voltage V; 45 485 5.2 ‘ V
Input resistance Rig 2.9 3.9 kfl
Output resistance Ru 3/5 200 Q
Changeover current [4 3.5 mA
Input current for set inputs ‘I5/em 4 20 pix


No comments:
Post a Comment
The most important thing to remember about the Comment Rules is this:
The determination of whether any comment is in compliance is at the sole discretion of this blog’s owner.
Comments on this blog may be blocked or deleted at any time.
Fair people are getting fair reply. Spam and useless crap and filthy comments / scrapers / observations goes all directly to My Private HELL without even appearing in public !!!
The fact that a comment is permitted in no way constitutes an endorsement of any view expressed, fact alleged, or link provided in that comment by the administrator of this site.
This means that there may be a delay between the submission and the eventual appearance of your comment.
Requiring blog comments to obey well-defined rules does not infringe on the free speech of commenters.
Resisting the tide of post-modernity may be difficult, but I will attempt it anyway.
Your choice.........Live or DIE.
That indeed is where your liberty lies.
Note: Only a member of this blog may post a comment.